Did you know that aluminum is one of the most commonly used metals in the world? In fact, approximately 1.5 million tons of aluminum are consumed annually in the United States alone. Among all the aluminum alloys, the 6061 aluminum alloy stands out due to its excellent mechanical properties, corrosion resistance, and versatility. This raises a vital question for manufacturers and engineers alike: Is 6061 aluminum easy to cut in CNC machining, and what techniques can improve precision?
As manufacturers increasingly turn to CNC (Computer Numerical Control) machining for precision engineering, understanding the characteristics of materials like 6061 aluminum can significantly impact production quality and efficiency. This comprehensive blog will delve deep into the nuances of machining 6061 aluminum, offering high-value insights and practical solutions to enhance CNC machining precision.
—
Understanding 6061 Aluminum
What is 6061 Aluminum?
6061 aluminum is a medium-strength alloy that contains magnesium and silicon as its major alloying elements. This alloy is widely used in structural applications due to its excellent corrosion resistance, weldability, and ability to be heat-treated, which enhances its strength.
Properties of 6061 Aluminum
Given these attributes, 6061 aluminum has secured its place as a staple in the CNC machining industry. But is it easy to machine?
—
Machining 6061 Aluminum: Challenges and Solutions
While 6061 aluminum is overall relatively easy to machine, it presents unique challenges that, if not addressed, can lead to inefficient processes and sub-quality outputs. Let’s explore some of the primary challenges along with actionable solutions.
Challenge: Aluminum, despite being easy to cut, can lead to rapid tool wear, especially if the cutting tools are not appropriately selected or maintained.
Solution:
Challenge: During the CNC machining process, aluminum can create long, stringy chips that may wrap around parts and tools, leading to tool interference and surface finish issues.
Solution:
Challenge: Although aluminum has excellent thermal conductivity, excessive heat can still compromise the material properties and affect precision.
Solution:
Challenge: Achieving a fine surface finish is often crucial for various applications, particularly those in the aerospace and automotive industries.
Solution:
Challenge: Maintaining dimensional accuracy can be challenging, especially in a material that can expand and contract with temperature changes.
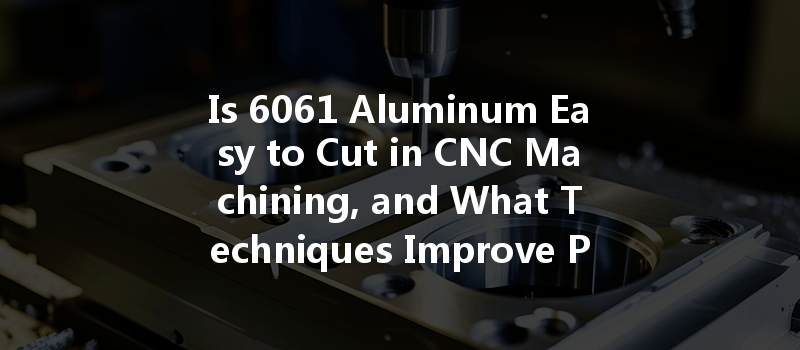
Solution:
—
Tools and Techniques for CNC Machining 6061 Aluminum
To fully leverage the advantages of 6061 aluminum, selecting the right tools and techniques is vital. Below are some fundamental tools, methods, and practices that can enhance CNC machining operations in terms of precision and efficiency.
Choosing the Right Tools
Machining Techniques
Software and Planning
—
Real-World Applications of 6061 Aluminum CNC Machining
The versatility of 6061 aluminum allows for its use in multiple industries. Here are a few notable applications:
—
CNC machining 6061 aluminum can be a seamless process when the correct tools, techniques, and practices are implemented. Understanding the properties of 6061 aluminum, addressing challenges such as tool wear, chip management, and heat generation with targeted solutions can significantly elevate the quality of machined parts.
By leveraging high-quality tools, advanced machining strategies, and real-time adaptations in CNC processes, manufacturers can produce precise, durable, and aesthetically pleasing parts that stand the test of time.
Remember, while 6061 aluminum is easy to machine in theory, mastering the nuances in practice is key to unlocking its full potential in your projects. As technology advances, staying informed about best practices will help you remain competitive in the ever-evolving manufacturing landscape.
This blog serves not only as a guide for enthusiasts and professionals in the field but also as a reminder of the importance of continuous improvement and adaptation. Investment in knowledge and technology can lead to a future where CNC machining not only meets but exceeds expectations.