Did you know that improper clamping can lead to a staggering 37% increase in machining errors? In the world of CNC machining, this statistic serves as a wake-up call for manufacturers seeking to enhance precision and efficiency. Every shift in a workpiece—even by a fraction of a millimeter—can translate into significant discrepancies, affecting both quality and production schedules. Whether you’re new to CNC machining or seeking to refine your processes, recognizing the importance of effective workpiece clamping and positioning is fundamental to achieving optimal results.
In this blog post, we will delve deeply into the nuances of optimizing workpiece clamping and positioning in CNC machining. From understanding the significance of clamping types to exploring advanced positioning techniques, we’ll provide a comprehensive guide filled with actionable insights. Our goal is to empower you to improve accuracy, minimize errors, and maximize efficiency in your machining operations.
The Importance of Workpiece Clamping and Positioning
Effective clamping and positioning are crucial in CNC machining for several reasons:
Types of Clamping Systems
Understanding the various types of clamping systems available is the first step in selecting the right one for your operations. Here are some common types:
Mechanical clamps utilize physical mechanisms to secure the workpiece. These can include:
Hydraulic clamps use fluid pressure to apply force to the workpiece. They offer multiple benefits:
Vacuum clamping relies on suction to hold the workpiece in place. This method is best for flat and thin materials and is excellent for high-precision applications.
Magnetic clamps utilize magnetic force for holding ferromagnetic materials. They are quick to set up and often used in applications requiring frequent changes.
Choosing the Right Clamping System
Selecting the right clamping system requires careful consideration:
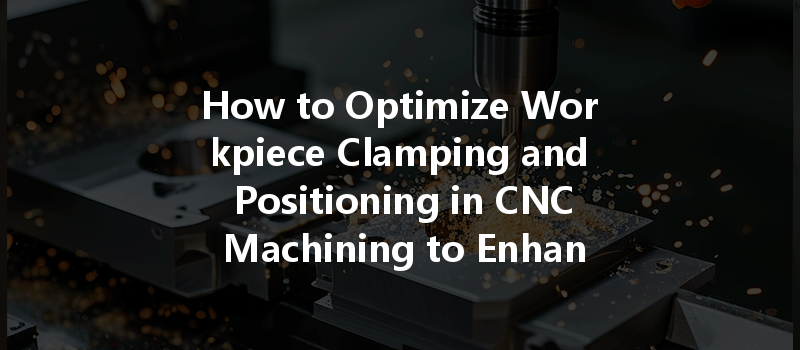
Advanced Positioning Techniques
Once you’ve selected an appropriate clamping system, optimizing positioning techniques is key to achieving accuracy.
Custom fixtures can be integrated to ensure precise positioning of the workpiece relative to the cutting tool. Fixtures reduce setup times and ensure repeatability across production runs.
Incorporating CMM technology into the machining process allows for accurate measurement of part dimensions before, during, and after machining. This technology can identify any misalignments and prevent defective parts from leaving the shop.
Using software to simulate tool paths can provide insights into where clamping and positioning adjustments might improve accuracy. By visualizing the process, you can avoid potential conflicts and errors.
Best Practices for Clamping and Positioning
Here are some effective practices to enhance clamping and positioning accuracy:
Routine checks on clamping systems ensure they are in optimal condition. Replace worn parts and ensure hydraulic systems are leak-free.
For larger workpieces, using multiple clamps can help distribute forces more evenly, preventing distortion during machining.
Establishing standardized setup procedures can lead to more consistent and repeatable results. Training operators on proper clamping and positioning techniques will further enhance productivity.
Implement real-time monitoring systems to detect deviations in machining accuracy. Addressing issues as they arise can prevent costly errors.
Case Studies: Successful Clamping Optimization
To illustrate the effectiveness of these techniques, consider the following case studies:
Case Study 1: Aerospace Components Manufacturing
A machining facility producing aerospace components faced challenges with dimensional accuracy due to improper clamping. By implementing hydraulic clamps and custom fixtures, the facility achieved a 40% reduction in machining errors and improved delivery timelines.
Case Study 2: Automotive Parts Production
An automotive manufacturer struggled with excessive tool wear rates driven by inefficient clamping methods. By switching to magnetic clamps and integrating CMM technology alongside intensified operator training, they improved tool life by 30% and doubled their production output.
Minimizing errors in CNC machining through optimized workpiece clamping and positioning is no small feat; however, it is an achievable goal with the right knowledge, tools, and techniques. By understanding the various types of clamping systems, employing advanced positioning techniques, and implementing best practices, manufacturers can significantly enhance precision and efficiency.
The importance of precise clamping and positioning in CNC machining cannot be overstated. It affects not just the outcome of individual jobs but also the overarching performance and reliability of manufacturing operations. Enhancing accuracy requires ongoing effort and adaptability, making it crucial for professionals in the field to stay informed on the latest techniques and technologies.
As you reflect on the content shared in this blog, consider how these insights can be applied in your operation. Embracing these practices will not only improve your manufacturing capabilities but also secure your reputation for quality in a competitive industry. Take the steps necessary to optimize your clamping and positioning techniques today, and experience the transformative benefits it can yield for your CNC machining operations.