It is estimated that the global demand for aluminum will reach 60 million metric tons by 2030, with much of this demand influenced by the automotive, aerospace, and construction industries. As industries increasingly lean on aluminum due to its lightweight and durable nature, it’s crucial to understand how aluminum processing, particularly CNC (Computer Numerical Control) processing, affects the environment. This blog aims to provide a comprehensive breakdown of evaluating the environmental impact of aluminum CNC processing, detailing methods, metrics, and practices to reduce its ecological footprint.
Understanding CNC Processing of Aluminum
CNC machining is a manufacturing process that utilizes computer-controlled tools to remove material from a workpiece to create parts with high precision. This technology has revolutionized the manufacturing landscape, offering superior accuracy and efficiency. When dealing with aluminum, CNC machining can result in products that are both lightweight and strong, attributes highly sought in a variety of applications.
Environmental Concerns Associated with Aluminum CNC Processing
Despite its benefits, aluminum CNC processing raises several environmental concerns:
Step-by-Step Guide to Evaluate Environmental Impact
The first step in evaluating the environmental impact of aluminum CNC processing is gathering relevant data. This will include:
Life Cycle Assessment (LCA) is a comprehensive method to evaluate the environmental impacts associated with all stages of a product’s life, from raw material extraction through processing, use, and disposal.
Key Stages of LCA:
Calculating the carbon footprint of aluminum CNC processing involves compiling emissions released throughout every stage of production. This typically encompasses:
Utilizing carbon footprint analysis software will streamline this process and yield more accurate results.
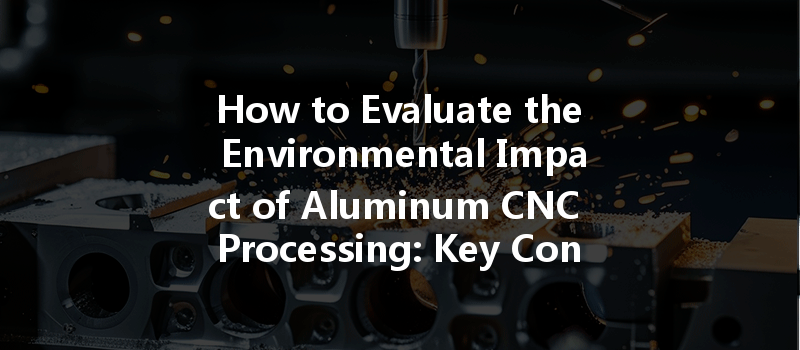
An effective evaluation involves comparing aluminum CNC processing with alternative manufacturing techniques. Aspects to consider include:
Familiarity with environmental regulations and standards is paramount in evaluating the impact. This involves understanding:
Engaging stakeholders—employees, suppliers, customers, and community members—is fundamental for holistic impact assessment.
To mitigate adverse impacts found during the assessment, implement viable reduction strategies, including:
Monitoring the implemented strategies’ effectiveness is essential for ongoing improvement. Utilize performance metrics regularly, and adjust processes based on findings.
The Importance of Evaluating Environmental Impact
Understanding and assessing the environmental impact of aluminum CNC processing is not merely a compliance exercise. It represents a critical commitment to responsible manufacturing practices that yield benefits in several arenas:
Evaluating the environmental impact of aluminum CNC processing is essential for responsible manufacturing and sustainability practices. By following the steps detailed in this blog—starting with thorough data collection, conducting a life cycle assessment, and implementing effective reduction strategies—companies can mitigate negative environmental effects associated with their operations. Moreover, continuous monitoring and improvement ensure that these practices evolve with emerging technologies and environmental standards.
In a world where sustainability is no longer optional but imperative, manufacturers have a significant opportunity to lead the change toward a cleaner and more efficient future. As industries adopt these methods, they not only improve their operations but contribute positively to the planet. This blog serves as a guide to navigating that intricate landscape and emphasizes the importance of conscious manufacturing in today’s world. It is worth pondering how each of us—manufacturers, consumers, and stakeholders—can collectively make a difference. Every small step toward sustainability counts for our planet’s future.