Have you ever wondered how precision tools made from metals and plastics, are routinely manufactured with such accuracy that they fit into complex machines seamlessly? In the world of manufacturing, especially in industries like aerospace, automotive, and medical devices, the slightest deviation in part dimensions can lead to catastrophic failures or inefficiencies. As industries continue to push the limits of technology, the accuracy and consistency of CNC (Computer Numerical Control) machining become paramount in delivering quality products.
The Importance of CNC Machining Accuracy
According to a report by the World Economic Forum, over 80% of manufacturing companies believe that precision is crucial for competitiveness in the industry. CNC machining, with its ability to produce intricate and high-tolerance components, plays a pivotal role in achieving that precision. It reduces human error, increases repeatability, and produces complex shapes that would be nearly impossible to achieve using traditional machining methods.
Yet, ensuring accuracy and consistency during CNC machining isn’t as straightforward as it may seem. Let’s delve into the various aspects that affect machining accuracy and explore effective solutions for each.
Factors Influencing CNC Machining Accuracy
Let’s break down these factors further and identify solutions to mitigate potential issues.
Understanding the Issue:
Machine calibration refers to the process of adjusting the CNC machine to ensure it is operating within its specified tolerances. Machines can drift over time, leading to errors in the dimensions of machined parts.
Solution:
Regular calibration of CNC machines is vital. Establish a calibration schedule based on the manufacturer’s recommendations and the intensity of machine usage. Utilize laser calibration tools to assess positional accuracy and make adjustments as needed. Training operators in proper calibration techniques can also yield substantial benefits.
Understanding the Issue:
The cutting tools used in CNC machining experience wear over time due to friction and heat. This wear can lead to inconsistencies in machining processes, which ultimately affects the quality of the parts.
Solution:
Monitor tool wear with precision. Implement a preventive tool maintenance program that includes regular inspections and replacements based on specific wear indicators. Additionally, invest in high-quality cutting tools designed for the materials you are machining. Using advanced coatings on cutting tools can also minimize wear and increase their lifespan, further ensuring machining consistency.
Understanding the Issue:
Different materials have different machining characteristics. Properties like hardness, brittleness, and thermal expansion can affect machining accuracy.
Solution:
Perform thorough material analysis before starting production. Choose the appropriate cutting parameters (speed, feed rate, depth of cut) suitable for the specific material. For sensitive materials, consider pre-conditioning processes to ensure better consistency during machining.
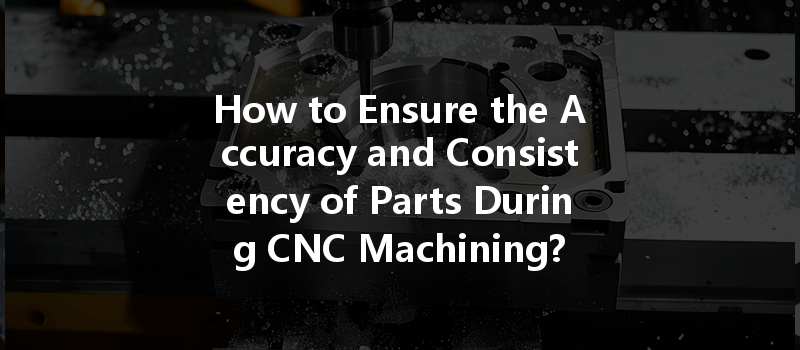
Understanding the Issue:
Fluctuations in temperature, humidity, and other environmental factors can lead to dimensional changes in both the CNC machine and the workpieces, affecting accuracy.
Solution:
Maintain stable environmental conditions in the machining area. Ideally, the temperature should be kept within a specific range using climate control measures. Humidity should also be monitored to prevent material deformation.
Understanding the Issue:
The software controlling the CNC machine plays a crucial role in achieving the desired machining results. Poorly written code or programming errors can lead to inaccuracies in the finished products.
Solution:
Invest in high-quality CAD/CAM (Computer-Aided Design/Computer-Aided Manufacturing) software. Validate and simulate machining programs before actual production. Regular training sessions for programmers and operators on advanced machining techniques can enhance their skills and minimize errors.
Understanding the Issue:
Quality control is critical for ensuring machined parts meet specifications. Inconsistent inspection processes can lead to defective parts passing through production.
Solution:
Implement a robust quality control system that includes in-process inspection and post-machining audits. Utilize advanced measurement technologies such as Coordinate Measuring Machines (CMM) or laser scanning for precise dimensional checks. Engage in Statistical Process Control (SPC) methods to monitor machining processes and identify variations in real-time.
Best Practices for Achieving Accuracy
To achieve accuracy and consistency in CNC machining, here are some additional best practices:
Ensuring accuracy and consistency in CNC machining isn’t merely a technical challenge; it’s a critical necessity in achieving high-quality manufacturing outcomes. By understanding the key factors that influence accuracy—such as machine calibration, tool wear, workpiece materials, environmental conditions, software errors, and quality control—you can take decisive action to optimize your CNC processes.
The practices and solutions recommended in this blog will guide manufacturers toward adopting a more systematic approach to CNC machining, ultimately leading to superior quality and productivity. Remember, in the competitive landscape of manufacturing, precision isn’t just a goal; it’s a vital component of operational excellence.
Reflect & Act
Understanding these various elements and implementing solutions not only enhances your production quality but also instills confidence in your processes and products. By prioritizing accuracy in CNC machining, you position your business for success and sustainability in a rapidly evolving industry. Let this serve as a reminder that quality matters and proactive measures today can lead to unparalleled precision tomorrow.