Did you know that approximately 70% of manufacturing costs are influenced by the choice of materials? This stunning statistic underscores the importance of selecting the right alloy for your machining processes, especially when it comes to steel. A fundamental aspect of this decision-making process is understanding machinability — the ease with which a material can be cut, shaped, or drilled. In this blog, we will explore how to effectively compare the machinability of different steel alloys in manufacturing.
Understanding machinability can drastically reduce production costs, improve product quality, and enhance the efficiency of the machining processes. Let’s delve deep into the essential factors, techniques, and tools you need to compare steel alloys effectively.
—
—
Definition and Importance
Machinability refers to the ease with which a material can be cut or shaped using various machining processes. It’s a pivotal characteristic for manufacturing engineers and machinists, as it directly influences production efficiency and costs. The importance of machinability is reflected in several aspects:
Factors Influencing Machinability
Several factors come into play when assessing the machinability of a steel alloy:
—
Overview of Steel Alloys
Steel alloys are composed of iron and varying percentages of carbon and other alloying elements, which impart different properties. Common categories include:
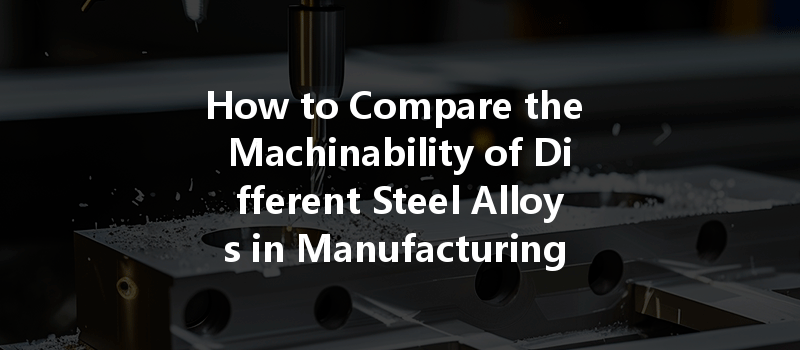
Popular Choices for CNC Machining
Each category has its champions for CNC machining:
—
Standardized Tests
To measure the machinability of different steel alloys, several standardized tests and metrics are employed:
Key Metrics
Several key metrics should be monitored during comparison:
—
When comparing machinability among different steel alloys, it’s important to consider:
Composition and Mechanical Properties
The specific composition directly affects hardness, tensile strength, and toughness. Tools must be selected accordingly.
Cost Considerations
Material costs strongly influence machining budgets. While some alloys exhibit superior machinability, they may come with significantly higher price tags.
Environmental Impact
Consider the sustainability factors of each alloy in terms of recyclability and energy consumption during machining.
—
Experimental Approaches
Conducting controlled experiments under standardized conditions is essential for obtaining quantitative data on machinability.
Simulation Software
Utilizing advanced simulation software can predict the behavior of different alloys under various machining conditions, leading to informed decisions.
Machinability Data and Charts
Refer to reputable machinability data published by industry organizations to compare alloys and determine suitability for specific applications.
—
Case Studies in Manufacturing
Consider real-world applications in companies that followed a structured approach for comparing alloys:
Lessons Learned from Industry Leaders
Learn from top manufacturers who routinely engage in materials research to stay ahead of their competition, offering insights into best practices and innovative solutions.
—
In conclusion, comparing the machinability of different steel alloys is a critical step in effective manufacturing. By understanding the fundamental aspects of machinability, including alloy types, measurement techniques, and practical applications, manufacturers can make informed decisions that lead to cost savings, improved product quality, and operational efficiency.
As we have covered, embracing a systematic approach to evaluating machinability will empower manufacturers to select the optimal steel alloy for their specific needs. Continuous learning in materials science is essential; it not only ensures competitive advantage but also fosters innovation within the industry.
Thus, the next time you face a decision regarding material selection in production, remember the significance of machinability at every level of your manufacturing process. The future of efficient and cost-effective manufacturing lies in these important choices.