Did you know that over 70% of product failures occur due to inadequate surface treatments? This staggering statistic underscores the critical role that surface treatment technologies play in product performance and longevity. Whether you are manufacturing automotive components, electronic devices, or even medical equipment, making an informed choice about surface treatments can significantly enhance your product’s functionality, durability, and aesthetic appeal. In this comprehensive guide, we will explore the intricacies of various surface treatment technologies and outline how to select the most appropriate one based on specific product characteristics.
Surface treatment encompasses various processes aimed at altering the surface characteristics of a material to enhance its physical properties and overall lifespan. These techniques can improve corrosion resistance, wear resistance, adhesion properties, and aesthetic appeal. With the advent of advanced manufacturing technologies and changing consumer demands, the importance of selecting the right surface treatment technology has never been more critical.
In a market that emphasizes quality, durability, and cost-effectiveness, understanding how to select the most suitable surface treatment technology is not just necessary—it can define a product’s success or failure.
There is a myriad of surface treatment technologies available today. Here, we breakdown the leading types to provide you a clear understanding of what each entails.
2.1 Coating
Coating involves applying a layer of material to the surface of a product. This can include paints, varnishes, or polymer films. Coatings can serve functional purposes aside from aesthetic enhancement, such as providing waterproofing or UV resistance.
2.2 Electroplating
Electroplating is a process that uses electrical current to reduce metal cations from a solution, forming a thin layer of metal on the substrate. Applications often include decorative plating and enhancing corrosion resistance, especially in the automotive and jewelry industries.
2.3 Anodizing
Anodizing is an electrolytic process that converts the surface of a metal into a decorative, durable, corrosion-resistant anodic oxide finish. Particularly popular among aluminum products, anodizing improves surface hardness and facilitates better adhesion for paints and coatings.
2.4 Thermal Spray Coating
Thermal spray coating involves melting materials and spraying them onto a substrate to form a coating. It is highly effective in applications that require high wear and corrosion resistance, such as in diesel engine components.
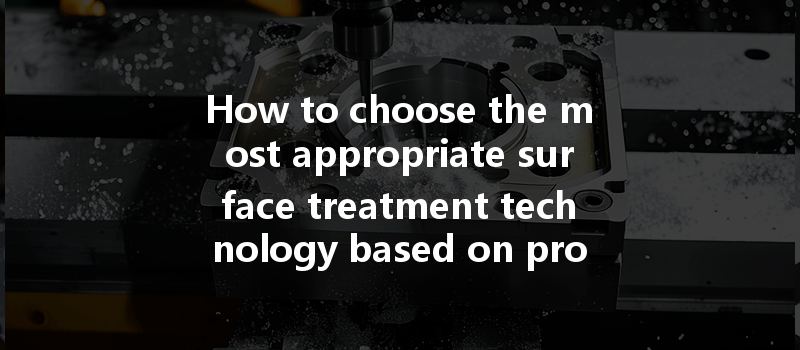
2.5 Chemical Treatments
Chemical treatments involve various chemical processes, including phosphating and pickling. These techniques clean the substrate surface and can add corrosion resistance or promote better bonding for subsequent coatings.
Choosing the right surface treatment is a multifaceted decision influenced by numerous factors. Below, we delve deeper into the critical elements that should guide your decision-making.
3.1 Material Properties
Understanding the base material is fundamental when considering surface treatments. Different materials react distinctively to various treatments. For instance, aluminum may require anodizing for optimal corrosion resistance, while steel may be more suited to galvanizing.
3.2 Environmental Conditions
The environment in which the product will be used plays a significant role in treatment selection. Products exposed to harsh conditions—like high humidity, extreme temperatures, or chemical exposure—will need surface treatments specifically designed for durability under such conditions.
3.3 Functionality Requirements
The intended functionality of the product will heavily dictate the type of surface treatment selected. If the part is designed for electrical conductivity, a non-conductive coating would be detrimental, highlighting the need to align treatment choice with product functionality.
3.4 Aesthetic Considerations
In many industries, the visual appeal of a product is just as important as its functionality. Surface treatments can significantly enhance appearance, so consider colors, gloss levels, and textures that complement the product design.
3.5 Regulatory and Compliance Factors
Certain industries are governed by strict regulations regarding surface treatments. For example, medical devices must adhere to biocompatibility standards. Understanding these requirements is essential to avoid costly regulatory issues later in production.
Product characteristics play a crucial role in surface treatment selection. Below, we categorize some of the most common materials and summarize the considerations for each.
4.1 Metal Components
For metal components, mechanical properties such as tensile strength and hardness must be assessed, along with potential exposure to corrosive environments. Surface treatments like anodizing or electroplating may be beneficial here.
4.2 Plastics
Plastics require precise surface treatments to enhance adhesion for paint or coatings. Techniques such as flame treatment or plasma treatment can be effective for improving surface esthetics and performance.
4.3 Rubber
For rubber components, treatments focusing on adhesion and wear resistance can be considered. Coatings and surface modifiers that improve flexibility and reduce friction are often used.
4.4 Electronically Conductive Surfaces
Surface treatments for electrically conductive surfaces require further consideration as they must maintain conductivity while offering protection from oxidation. Treatments like electroplating with gold or silver can be suitable options.
5.1 Automotive Industry
In the automotive sector, where components like gears, engine parts, and exterior finishes must endure extreme conditions, the choice of surface treatment is vital. For example, electroplating can enhance the corrosion resistance of exposed automotive parts, while anodizing aluminum components can improve both durability and aesthetics.
5.2 Electronics Industry
Electronic devices demand surface treatments that ensure proper conductivity and minimal interference. Anodized aluminum is becoming increasingly popular for electronic enclosures due to its combination of durability and lightweight characteristics.
5.3 Medical Devices
In the medical field, surface treatments can significantly impact the safety and effectiveness of devices. Materials used in surgery must be biocompatible, and surface treatments that reduce bacterial adhesion, such as hydrophilic coatings, are becoming standard.
In sum, selecting the proper surface treatment technology based on product characteristics is an intricate yet vital task that involves examining various factors, including material properties, environmental conditions, functionality, aesthetic values, and compliance needs.
Correctly implemented surface treatments not only enhance product performance but also extend the lifespan of components, ultimately leading to greater customer satisfaction and reduced costs over time.
As industries evolve and consumer expectations rise, the need for a thorough understanding of surface treatment technologies and their implications on product performance cannot be overstated.
Why This Blog Matters
The information and strategies discussed in this blog are designed to guide engineers, designers, and manufacturers through the complex landscape of surface treatment technologies. By understanding how to effectively choose the right surface treatment, businesses can drive efficiencies, ensure quality, and improve their bottom line—principles that are crucial to maintaining competitiveness in today’s market. Your choice of surface treatment will significantly impact not just your product’s end-use performance but also its marketability and success.
For further reading, you may want to explore additional resources on industry-specific treatments or the latest innovations in surface treatment technologies. Remember, investing in the right surface treatment is investing in the future of your products.