Did you know that the CNC machining industry is projected to reach a market value of over $100 billion by 2026? As technology evolves, precision machining becomes more crucial, ensuring accuracy and efficiency in producing complex parts across various industries. If you’re a manufacturer, engineer, or someone involved in CNC machining, understanding how to select the right machining methods based on the characteristics of your parts can dramatically improve your production efficiency and product quality. This comprehensive guide will dive into the key factors affecting your choice of CNC machining methods and provide detailed solutions to optimize your machining processes.
Understanding CNC Machining Basics
Before delving deeper into the selection process, let’s quickly review what CNC machining entails. CNC stands for Computer Numerical Control, and it refers to the automated control of machining tools via a computer. CNC machining encompasses various processes such as milling, turning, drilling, and grinding, allowing for high precision and repeatability in manufacturing components.
Given the wide range of capabilities in CNC machining, factors such as part geometry, material type, volume, and tolerances play essential roles in determining which method to choose for effective production.
Part Geometry
The shape and size of the part you’re working on significantly influence the machining method you choose. Here’s a breakdown of how different geometries can dictate your choice:
Material Type
The material from which a part is made plays a crucial role in machining selection as different materials possess unique properties that affect how they are processed:
Production Volume
Your production volume affects not just the method but also the setup time and tool wear. Here’s how to align machining processes with production needs:
Analysis of Tolerances
Tolerances refer to the allowable variations in part dimensions. Depending on the required accuracy for a component, the machining method must be compatible:
Detailed Solutions for Choosing CNC Machining Methods
Step 1: Define Part Specifications
Before settling on a machining method, document part specifications clearly. This includes measurements, tolerances, operational features, and material selection.
Example: Documenting Specifications for an Aerospace Component
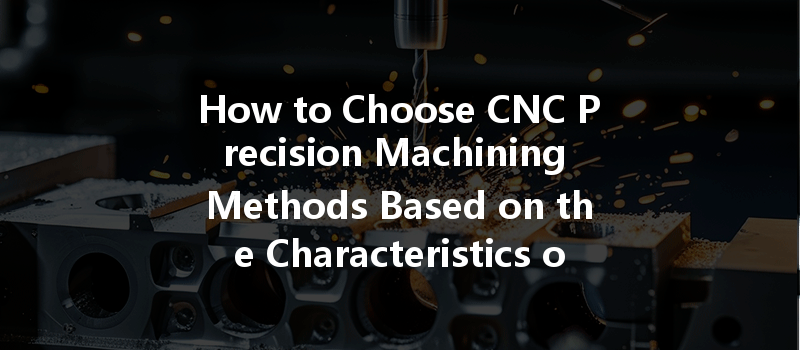
Step 2: Match Geometries to Suitable Machining Methods
After specification planning, select the machining process based on the part geometry listed in your documentation.
Step 3: Assess Material Compatibility
Understanding your material properties is crucial for choosing suitable tools and processes. Consider factors like thermal properties, strength, and machinability ratings.
Example: Evaluating Aluminum 7075 for Machining
Step 4: Consider Production Volume and Cost
Align machining techniques with production needs and costs. For our example, if there’s a demand for a small batch of 30 components, a flexible setup in CNC milling would be ideal.
Step 5: Evaluate Tolerance Requirements
Specify final tolerances first to understand what is achievable with each machining method. The tighter the tolerance, the more it may dictate the machining method chosen.
Choosing the correct CNC precision machining method based on the characteristics of your parts is critical to optimizing manufacturing efficiency, ensuring product quality, and managing costs.
Key techniques to remember:
In an industry where precision and efficiency are critical, understanding how to choose CNC machining methods smartly can set your project apart. Whether you’re working in aerospace, automotive, or any sector requiring precision parts, these insights will not only guide your selection process but also promote innovation and success in your manufacturing endeavors.
Remember, the landscape of CNC machining is ever-evolving; staying informed about advancements and best practices is essential for your enterprise’s growth and competitiveness.