CNC (Computer Numerical Control) machining has revolutionized the manufacturing industry by offering precision, efficiency, and flexibility. However, as businesses strive for profitability, understanding the costs associated with CNC machining, particularly the hourly rate, becomes critical. This comprehensive guide aims to unravel the intricacies of calculating the hourly cost of CNC machining and present strategies for optimizing these costs. At YL Machining, we understand the significance of these factors, and we’re eager to share our expertise to help you maximize efficiency and profitability in your operations.
—
Understanding the Components of CNC Machining Costs
Before diving into the calculations, it’s essential to recognize that the hourly cost of CNC machining isn’t a standalone figure; it encompasses various components. The primary elements include:
Step-by-Step Calculation of the Hourly Cost
Step 1: Determine Machine Hourly Rate
To calculate the machine hourly rate:
Calculation:
[
text{Machine Hourly Rate} = frac{ text{Purchase Price} }{ text{Useful Life in Hours} }
]
Where:
So,
[
text{Machine Hourly Rate} = frac{100,000}{20,000} = $5
]
Step 2: Calculate Labor Costs
Labor costs depend on the wage of the CNC machinist. If the average wage is $25 per hour plus benefits, which amount to 30% of wages, the calculation is as follows:
Step 3: Evaluate Material Costs
Material costs can fluctuate based on market conditions. It’s beneficial to source raw materials from multiple suppliers for competitive pricing. For instance, if you need aluminum at a cost of $7.00 per kg, you can estimate your required material based on the project specifics and multiply the total kg needed by the unit price.
Step 4: Assess Overhead Costs
To estimate overhead costs:
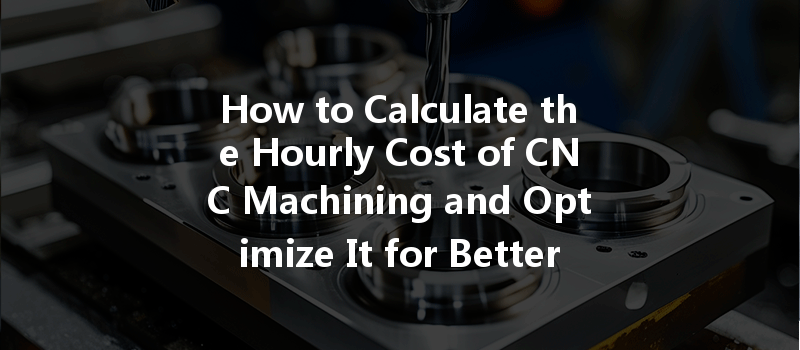
[
text{Overhead Cost Per Hour} = frac{Total Fixed Costs}{Operating Hours Per Year} = frac{50,000}{2,000} = $25
]
Step 5: Combine Costs for Total Hourly Rate
Finally, sum all components to find the total hourly cost of CNC machining:
[
text{Total Hourly Cost} = text{Machine Hourly Rate} + text{Labor Cost} + text{Material Cost} + text{Overhead Cost}
]
Assuming:
So,
[
text{Total Hourly Cost} = 5 + 32.50 + 20 + 25 = $82.50
]
Strategies for Optimizing CNC Machining Costs
After calculating your hourly rate, consider these strategies for cost optimization:
The Importance of Benchmarking
Understanding your costs in isolation is useful, but benchmarking against industry standards gives you a holistic perspective. Organizations like the National Tooling and Machining Association (NTMA) or the Precision Metalforming Association (PMA) provide resources and data that can help you better gauge where your costs stand compared to competitors in the CNC machining sector.
Case Study: YL Machining
At YL Machining, we have adopted these principles to maintain our competitive edge. Through a focus on process optimization and workforce training, we have successfully reduced our machine downtime by 25%, leading to a significant decrease in total hourly machining costs. We also engage with suppliers consistently to negotiate favorable pricing agreements, which has enabled us to keep material costs predictable and manageable.
Calculating and optimizing the hourly cost of CNC machining is a multi-faceted task that requires a thorough understanding of various cost components. By implementing systematic strategies and leveraging industry best practices, manufacturers can not only reduce costs but also increase productivity and profitability. At YL Machining, we are committed to excellence in CNC machining and share these insights to help you achieve success in your manufacturing endeavors.
As the CNC landscape continues to evolve, remaining agile and informed is paramount. By staying focused on cost analysis and optimization, your business will not only survive but thrive in an increasingly competitive environment. Explore further opportunities for improvement, continuously assess your processes, and leverage technological advancements; the rewards exceed just cost savings—they enhance your overall product quality and customer satisfaction.