Have you ever wondered why some machined parts maintain their precision while others seem to warp or miss specifications right after being processed? In the realm of CNC turning, one of the most significant challenges manufacturers face is material deformation. According to a study by the International Journal of Advanced Manufacturing Technology, as much as 30% of defects in precision machining can be attributed to material deformation during the processing phase. In this comprehensive guide, we will explore the causes of this problem in CNC turning and present effective solutions to mitigate the risk of deformation.
Understanding CNC Turning
CNC (Computer Numerical Control) turning is a subtractive manufacturing process that utilizes a lathe to remove material from a workpiece. The workpiece is rotated against a cutting tool, allowing for the creation of cylindrical shapes. This process is widely used in industries that require high precision, such as aerospace, automotive, and medical devices. Given the critical need for accuracy, understanding how to prevent material deformation is of utmost importance.
Causes of Material Deformation in CNC Turning
Before we delve into the solutions, it’s crucial to understand what causes material deformation during CNC turning. Here are some primary factors that contribute to this issue:
During the cutting process, the friction generated between the cutting tool and the workpiece releases heat. This heat can cause the workpiece material to expand, which, upon cooling, may lead to warping.
The forces exerted during machining operations can induce stress in the material. If these forces exceed the material’s yield strength, permanent deformation will occur.
Using the wrong tool geometry can lead to ineffective cutting, resulting in excessive stress at the cutting edge, which can, in turn, deform the workpiece.
If the workpiece is not adequately supported, vibrations and movement during machining can lead to inaccuracies. This can cause the material to bend or deform under the cutting load.
Different materials react differently to machining operations. Some may be more prone to deformation based on their hardness, brittleness, or thermal conductivity.
Strategies to Avoid Material Deformation
Now that we’ve identified the potential causes of material deformation in CNC turning, let’s explore effective strategies to mitigate these risks.
Choosing the right cutting tools is fundamental to reducing deformation. Consider the following factors when selecting tools:
Adjusting the spindle speed and feed rate can significantly impact the thermal and mechanical stresses on the workpiece:
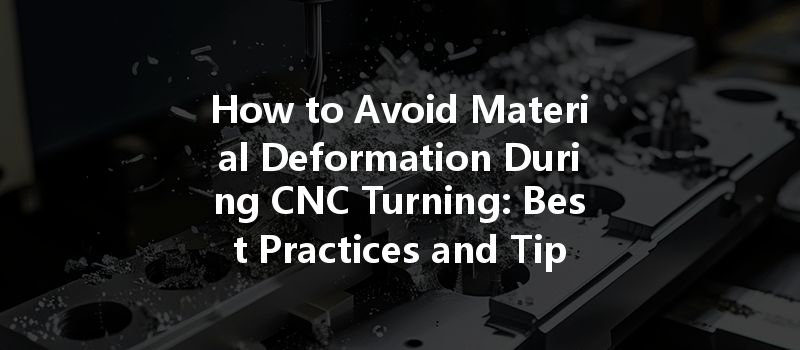
Implement methods to manage heat during the cutting process:
Effective fixturing is crucial for minimizing deformation:
Incorporating specific material treatments can enhance performance during machining and prevent deformation:
To achieve a reliable CNC turning operation, ensure that the CNC machine is properly set up and calibrated:
Implementing real-time monitoring and process control mechanisms can assist in identifying potential deformation issues before they escalate:
Material deformation during CNC turning is a critical issue that can lead to decreased product quality, wasted materials, and increased costs. However, by employing a combination of effective strategies and techniques, manufacturers can significantly reduce the risk of deformation.
By selecting appropriate tools, controlling machining parameters, ensuring proper fixturing, and integrating heat management and monitoring systems, success in CNC turning is achievable. Each of these techniques contributes to maintaining material integrity and achieving high-precision outcomes in machined parts.
In today’s competitive manufacturing landscape, it is essential to continuously evaluate and improve CNC processes to remain profitable and efficient. Understanding how to avoid material deformation is not only a technical challenge, but it is also an opportunity for growth and innovation in manufacturing.
This blog serves as a comprehensive resource for anyone looking to deepen their understanding of CNC turning and mitigate the risks associated with material deformation. By implementing these strategies effectively, businesses can secure a competitive advantage in their respective industries. Don’t underestimate the importance of these practices—they could be the difference between mediocre performance and exceptional precision in your machining operations.