Did you know that the global market for surface preparation technology, including sandblasting, is projected to reach over $5.9 billion by 2025? With the growth of various manufacturing processes, understanding the role of surface treatment technologies—especially in CNC machining—has never been more critical. As manufacturers seek cost-effective solutions that don’t compromise on quality, a pivotal question emerges: How do the price differences between traditional sandblasting and modern laser sandblasting impact decision-making in CNC machining?
to CNC Machining Technologies
Computer Numerical Control (CNC) machining has revolutionized the manufacturing landscape by allowing for high-precision work on a wide range of materials. However, the effectiveness of CNC machining does not solely depend on the machine and its operations; it also heavily relies on the surface treatment methods utilized afterward. Among these, sandblasting and laser sandblasting are two widely used processes for preparing surfaces, enhancing aesthetics, and improving material properties.
This blog will explore the key differences between traditional sandblasting and laser sandblasting, their respective costs, and how these factors influence CNC machining choices. By understanding these elements, businesses can make informed decisions that enhance their production efficiency and overall quality.
Understanding Sandblasting
Traditional sandblasting, or abrasive blasting, involves propelling abrasive materials at high velocities to clean or etch surfaces. The process is widely used to prepare metal parts for painting or coating and can also remove rust, scale, and contaminants. The key elements of sandblasting include:
Cost Considerations in Sandblasting
When considering sandblasting, there are a few cost factors to keep in mind:
An Overview of Laser Sandblasting
Laser sandblasting, often referred to as laser surface treatment or laser cleaning, employs high-intensity lasers to remove contamination and prepare surfaces without the use of abrasives. The advantages of laser sandblasting include:
Cost Considerations in Laser Sandblasting
Comparing the Costs: Sandblasting vs. Laser Sandblasting
When analyzing the price difference between these two technologies, several factors come into play:
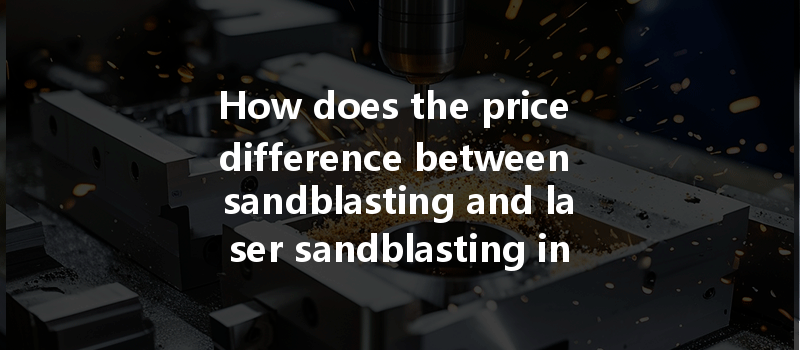
Strategic Decision-Making for CNC Machining
Understanding the price differences between sandblasting and laser sandblasting can significantly influence CNC machining decisions. Here are several key considerations for manufacturers when deciding between these two surface treatment options:
Manufacturers should conduct a comprehensive cost analysis that includes not only initial equipment costs but also long-term operational expenses. The right choice will align with the overall project budget while providing optimal results for the application.
For high-volume production, laser sandblasting may prove more cost-effective due to its time efficiency and lower long-term material costs. Conversely, low-volume operations or one-off projects might find traditional sandblasting adequate and more affordable.
The required surface finish and quality will influence the choice. For applications with strict tolerances, laser sandblasting may be the ideal choice due to its precision and reduced risk of material damage.
Different materials respond uniquely to each treatment. Understanding the interaction between the specific materials being machined and the chosen surface preparation method will greatly affect performance and longevity.
Both methods have different environmental footprints. Laser sandblasting generates less waste, making it a more sustainable option—an increasingly crucial factor for modern manufacturers seeking to adhere to environmental regulations and standards.
Case Studies: Real-World Applications
To gain a deeper understanding of the practical implications of these choices, let’s consider some case studies that highlight the impact of sandblasting vs. laser sandblasting in CNC machining environments.
Case Study 1: Aerospace Component Manufacturing
A leading aerospace manufacturer faced challenges with surface preparation for engine components. Initially relying on traditional sandblasting, they found that the time and costs associated with labor and materials were hindering production efficiency. After evaluating the cost differences, they transitioned to laser sandblasting. This switch not only reduced surface preparation time by over 50% but also improved the quality of the finishes, leading to higher inspection acceptance rates.
Case Study 2: Automotive Industry
An automotive parts manufacturer needed to coat parts with high-performance finishes. Their old sandblasting methods often resulted in inconsistencies that required additional rework and waste of materials. By integrating laser sandblasting, they slashed coating preparation time and improved finish integrity, translating to significant cost savings in both labor and materials. The manufacturer noted an overall increase in customer satisfaction due to the improved consistency of product quality.
: The Bigger Picture
To summarize, understanding the price differences between traditional sandblasting and laser sandblasting is crucial for manufacturers engaged in CNC machining. While sandblasting may initially seem cheaper, laser sandblasting offers significant advantages in terms of efficiency, quality, and long-term operational cost savings.
As you assess your options for surface treatment technologies, consider your unique production needs, budgetary constraints, material types, and desired quality levels. Adopting the right surface treatment method will not only optimize operational performance but will also enhance product quality, boost customer satisfaction, and potentially revolutionize your manufacturing process.
In today’s competitive manufacturing landscape, considering the cost implications of your chosen surface treatments is not just about immediate savings; it’s about positioning your business for future success. By making mindful decisions, you can ensure that your CNC machining processes remain efficient, sustainable, and positioned for growth in an ever-evolving industry.