Did you know that the melting point of steel can significantly affect not only the quality of the final product but also the efficiency of the smelting process? In metallurgy and CNC machining, understanding the intricacies of steel’s melting point is crucial for optimizing production costs and time while maintaining the desired properties of fabricated components.
The melting point of steel generally ranges between 2,500°F to 2,800°F (1,370°C to 1,540°C) depending on the alloy composition. This high temperature threshold illustrates the challenges manufacturers face during the smelting process. As we delve deeper into this topic, we will uncover how varying melting points influence the overall efficiency of CNC machining operations and explore practical solutions to optimize production.
Understanding the Basics of Steel Melting
What is Steel Melting?
Steel melting involves heating steel to its melting point, allowing it to transition from solid to liquid form. This liquid state is crucial for numerous industrial processes including casting and forging, where precise shaping and forming of metal components occur.
Factors Influencing the Melting Point of Steel
While the general melting point range is well-known, it is essential to recognize that the melting point of steel is influenced by various factors such as:
Understanding these factors is essential for optimizing the smelting process and ensuring the creation of high-quality steel.
The Role of Steel Melting in CNC Machining
With a clear understanding of steel melting, it is essential to explore the relevance of this process in CNC machining.
CNC Machining Explained
CNC (Computer Numerical Control) machining is a method that utilizes computerized controls to operate machines and tools for manufacturing parts. This automated process allows for high precision, repeatability, and the ability to produce complex geometries.
The Importance of Melting Point in CNC Machining
The melting point of steel plays a pivotal role in CNC machining concerning the following aspects:
How Melting Point Interacts with CNC Machining Techniques
As various CNC machining techniques (milling, turning, and grinding) are employed, the melting point directly influences different parameters, such as cutting speed, feed rates, and tooling choices. Understanding how these parameters work in conjunction with melting point data enables manufacturers to select the right equipment and settings to enhance productivity.
The Challenge: Inefficiencies in the Smelting Process
Common Issues Related to Melting Point in Machining
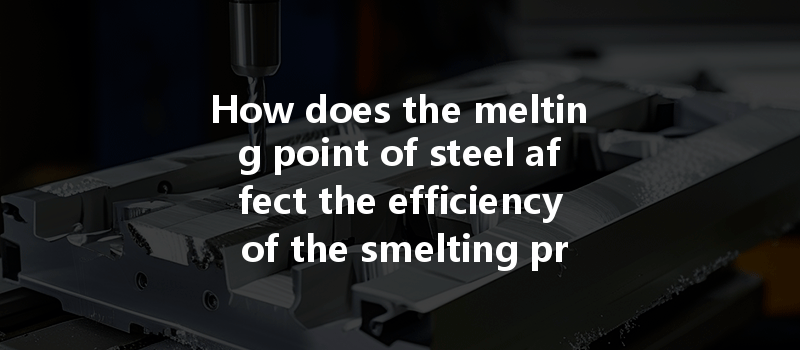
Solutions to Enhance Smelting Efficiency
To tackle the unique challenges posed by the melting point of steel in the smelting process, manufacturers can adopt several strategies.
Innovative Techniques in CNC Machining
Application of Additive Manufacturing
In combination with traditional methods, the integration of additive manufacturing allows for new possibilities in manipulating material properties. The careful control of melting points can enhance layer bonding, achieving superior physical properties.
Advanced Tooling Technologies
Utilizing cutting tools embedded with advanced coatings can reduce wear during high-temperature applications. This ensures precision and prolongs tool life, minimizing operational downtime.
Understanding the melting point of steel and its influence on the smelting process is absolutely critical for achieving efficiency and product quality in CNC machining. From optimizing production processes to ensuring the longevity of equipment, the insights shared in this blog emphasize the intricate relationship between melting point and manufacturing outcomes.
By actively investing in technology, enhancing workforce training, and adopting process innovations, manufacturers can tackle the challenges posed by melting temperatures head-on.
As the industry evolves, so too should our approaches to managing steel’s melting properties. Remember, optimizing the smelting process not only contributes to producing top-tier finished products but also leads to longer-term sustainability and cost-effectiveness in CNC machining operations.
In summary, addressing the melting point of steel should be at the forefront of every manufacturer’s mind, as it lays the foundation for the quality, efficiency, and success of their CNC machining endeavors. The importance of this topic cannot be overstated; it is key to remaining competitive in today’s manufacturing landscape. Let us continue to explore these advancements and work toward a more efficient and innovative future in CNC machining.