Did you know that aluminum has made a significant mark on the aerospace industry due to its impressive strength-to-weight ratio? As reported by the Aluminum Association, over 80% of airframes in modern aircraft are made from aluminum or its alloys. But what happens when you delve deeper into the mechanical and thermal properties of aluminum, specifically its melting point? Understanding how this parameter influences CNC (Computer Numerical Control) machining is crucial, especially in aerospace applications where precision and safety are paramount.
In this comprehensive blog, we will explore the melting point of aluminum, its significance in CNC machining, and how it affects various aspects of aerospace manufacturing processes. We’ll also analyze challenges related to machining aluminum alloys, optimal CNC parameters, and potential solutions to improve outcome efficiency.
Understanding Aluminum and Its Melting Point
Aluminum exhibits a melting point ranging from approximately 660°C (1220°F) to 680°C (1256°F) depending on the specific alloy. This relatively low melting point compared to other metals makes aluminum highly malleable, allowing for intricate machining while maintaining dimensional accuracy. However, the melting point also introduces certain considerations that CNC machinists must address to optimize their processes, particularly when producing components for the aerospace sector.
The aerospace industry encompasses a range of applications, from aircraft bodies to engine components. Knowing the melting point helps machinists ensure that materials do not lose their structural integrity during machining processes. For instance:
To avoid overheating, machine operators should consider the following CNC machining parameters:
CNC machining of aluminum in aerospace applications requires addressing potential thermal challenges. Here are effective strategies:
A. Proper Tool Selection
The choice of tools significantly impacts the machining process. Coated carbide tools, known for their heat resistance and durability, typically offer a better alternative for aluminum machining. These coatings enhance the tool’s lifespan by reducing friction, which also helps minimize heat generation.
B. Optimized Tool Geometry
Choosing tool geometries specifically designed for aluminum alloys can further improve heat dissipation. These tools often feature more favorable chip removal designs, allowing chips to exit quickly and reducing heat buildup around the cutting area.
C. Adaptive Feed Rate Control
Implementing adaptive machining techniques, which automatically adjust feed rates based on cutting conditions, helps minimize thermal impact. This responsive control can help maintain optimal machining temperatures and prevent overheating.
D. Effective Cooling Techniques
Incorporating strategies such as flood cooling, mist cooling, or even air cooling can significantly reduce the risk of overheating during machining. Selection of a suitable coolant is also essential. Water-soluble coolants or specialized lubricants can provide additional cooling and reduce friction.
The Role of Aluminum Alloys in Machining
Aluminum alloys are categorized primarily into two groups: wrought and cast. In aerospace applications, the following wrought alloys are particularly prevalent:
Different aluminum alloys exhibit varying machinability due to their alloying elements. For example:
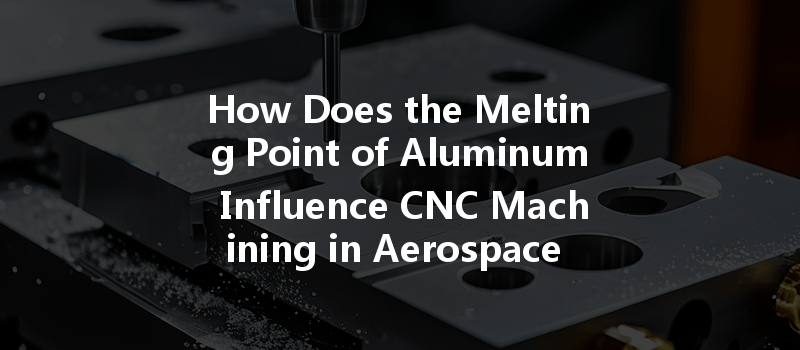
Understanding these properties can help machinists anticipate challenges and adapt their processes accordingly.
CNC Machining Techniques to Optimize Performance
A. Advanced CNC Technologies
Leveraging advanced CNC technologies can greatly enhance machining outcomes. For example:
B. Continuous Process Monitoring and Control
Implementing real-time monitoring systems can provide feedback on machining parameters, ensuring they remain within ideal ranges to prevent overheating. Data collected from such systems can lead to actionable insights that improve future machining operations.
C. Use of Simulation Software
Utilizing software that simulates the machining process allows manufacturers to test different parameters and tool paths before actual machining. This virtual environment helps identify optimal conditions for reducing thermal impact on aluminum alloys.
Training and Expertise in CNC Machining
Continuous education and training programs are critical for CNC operators, especially regarding the unique challenges associated with aluminum machining. Workshops focusing on tools, techniques, and materials can significantly improve operator expertise.
Encouraging a culture of collaboration and communication within machining teams can lead to shared solutions and innovative approaches to overcoming machining difficulties. Regular team meetings can highlight successes and areas for improvement.
Challenges and Solutions in CNC Machining of Aluminum
While machining aluminum has numerous advantages, it does come with its set of challenges. Here are some common ones along with suggested solutions:
A. Chip Formation
Challenge: Aluminum tends to form long, stringy chips, which can impact cycle times and potentially cause tool breakage.
Solution: Implementing a chip breaker strategy through appropriate tool angles and geometries can help generate shorter chips that facilitate smoother machining operations.
B. Surface Finish Quality
Challenge: Achieving high-quality surface finishes on aluminum components can be difficult due to its ductility.
Solution: Incorporating finish machining processes at the correct stage of production and optimizing coolant application can significantly improve the final surface quality.
C. Cost-Effectiveness
Challenge: Maintaining cost-effective machining processes while using expensive materials and ensuring high precision.
Solution: Streamlining processes through lean manufacturing principles and employing multi-functional tools can help reduce operational costs while maintaining quality.
In summary, understanding how the melting point of aluminum influences CNC machining is critical in aerospace applications. From managing heat generation to making astute decisions on tool selection and machining parameters, every aspect revolves around the aluminum alloy’s melting characteristics. By focusing on appropriate strategies such as effective coolant application, adaptive feed rate control, and expert training, the industry can enhance efficiency while ensuring the safety and reliability of aerospace components.
Before embarking on CNC machining processes, manufacturers must take time to analyze the specific aluminum alloys they seek to use, their melting points, and subsequent implications. This thorough analysis not only leads to better quality parts but also positions companies ahead of the competition in an ever-evolving industry.
CNC machining is more than just a manufacturing method; it represents a critical component in modern production systems, especially in aviation, where precision, efficiency, and safety reign supreme. So, whether you are a manufacturer, engineer, or simply a technology enthusiast, recognizing the intricate relationship between melting points and CNC processes should be of utmost importance in advancing your knowledge of this field.