Did you know that aluminum has one of the lowest melting points of all metals used in industrial applications? It melts at approximately 660.3 degrees Celsius (1220.5 degrees Fahrenheit). This characteristic makes aluminum highly versatile for various applications, but it also presents unique challenges in CNC (Computer Numerical Control) machining processes. How can the melting point influence machining efficacy, and what strategies can be employed to ensure that the CNC machining process operates smoothly?
CNC machining has revolutionized the manufacturing industry by allowing for precise and repeatable production of complex geometries. As the demand for lightweight and high-strength components continues to rise, aluminum has become a popular choice among manufacturers. However, understanding the impact of aluminum’s melting point on CNC machining is crucial for achieving the best results. In this extensive blog post, we will delve deep into the subject, exploring its implications, challenges, and effective approaches to mitigate potential pitfalls.
2.1 What is CNC Machining?
CNC machining is an automated manufacturing process where pre-programmed computer software controls the movement of factory tools and machinery. It integrates multiple machining operations such as milling, turning, drilling, and grinding to produce parts with high precision. By eliminating human error, CNC machining ensures consistent quality, faster production rates, and the ability to create complex geometries that manual machining cannot achieve.
2.2 Why Aluminum?
Aluminum is often preferred in various industries—especially aerospace, automotive, and electronics—due to its favorable properties:
However, the specific melting point of aluminum plays a crucial role in the outcome of CNC machining processes.
3.1 Understanding Melting Point in Machining Context
The melting point of a material is critical during machining because it can lead to thermal deformation, tool wear, and dimensional inaccuracies in the final product. When CNC machining aluminum, the risk of overheating is particularly pronounced as the machine tools generate frictional heat that can lead to an excessive rise in temperature, potentially compromising the part’s integrity.
3.2 Effects of Melting Point on CNC Machining
To optimize CNC machining processes involving aluminum and minimize issues related to its melting point, manufacturers can implement a variety of solutions. Let’s explore valuable techniques:
4.1 Optimize Cutting Parameters
Carefully selecting cutting speed, feed rate, and depth can significantly impact the heat generated during machining. Here are some considerations:
4.2 Efficient Cooling/Lubrication
The use of cutting fluids or coolants is paramount in maintaining the temperature of the material and tooling. Effective cooling strategies include:
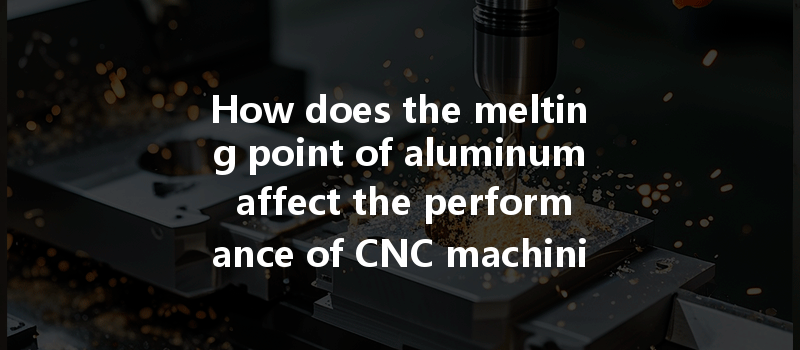
4.3 Tool Selection
Selecting the right tooling can make a significant difference in machining efficiency. Factors to consider include:
4.4 Adaptive Machining Techniques
Adaptive manufacturing involves real-time monitoring and adjustment of machining parameters. The implementation of technologies like IoT (Internet of Things) can significantly assist in:
4.5 Post-Processing Solutions
Implementing effective post-processing solutions can also enhance performance and quality:
Incorporating all of the previously discussed strategies and recommendations will provide a comprehensive approach to CNC machining aluminum:
5.1 Detailed Planning
Every successful machining operation begins with careful planning. Ensure to analyze the design features and how they will affect machining strategies. Plan your cutting parameters, tooling selection, and cooling methods accordingly.
5.2 Simulation and Prototyping
Utilizing simulation software to create a virtual model of the machining process can help identify potential issues before actual machining begins. Rapid prototyping may also provide insights into any design flaws or machining challenges.
5.3 Continuous Monitoring and Feedback
Establishing an ongoing feedback loop during machining operations allows for real-time adjustments and improved overall efficiency. Regularly monitor the tools, coolant, and part temperatures throughout the process.
5.4 Skilled Workforce
Invest in training operators to understand machining dynamics and conditions, enabling them to make informed decisions when operating CNC machines. Their expertise can be vital in troubleshooting and resolving issues related to temperature management and tool wear.
As technology advances, the future of CNC machining involving aluminum looks promising. Innovations such as advanced AI-driven machining systems and enhanced materials science research continue to yield improvements in the machining landscape. These developments will likely encompass:
Understanding how the melting point of aluminum influences CNC machining processes is crucial for achieving optimal results. By addressing thermal challenges through intelligent planning, precise control of cutting parameters, effective cooling, appropriate tooling, and continuous monitoring, manufacturers can mitigate potential issues and enhance the efficiency and effectiveness of their CNC operations.
As industries increasingly pivot towards more lightweight and durable materials like aluminum, staying informed about the critical factors that affect machining performance is vital. Innovations in technology, material sciences, and machining strategies will only continue to enhance the CNC landscape, making it an important area for ongoing learning and development.
This comprehensive guide serves as a crucial resource for manufacturing professionals, providing clear steps and considerations for improving CNC machining processes involving aluminum. Remember, the success of your CNC operations relies not only on the machines themselves but also on understanding and mitigating the unique challenges presented by the materials you work with. Embrace these insights and strengthen the foundation for your future machining endeavors.