In the world of manufacturing, the utilization of titanium alloys has gained significant traction due to their exceptional strength-to-weight ratio, corrosion resistance, and biocompatibility. If you’re considering embarking on projects involving titanium alloys, knowing their machinability is crucial — it can greatly influence both the quality of the end product and the efficiency of the manufacturing process. At YL Machining, our goal is to empower our readers with comprehensive insights into titanium alloy machining, helping you make informed decisions in your manufacturing endeavors.
So, whether you’re a seasoned engineer or a curious novice, buckle up as we dive deep into the machinability of various titanium alloys, unpacking their properties, cutting behaviors, and best practices for optimal machining processes.
What is Machinability?
Machinability refers to the ease with which a material can be shaped and formed using cutting tools. Several factors play into the machinability of a material, including:
For titanium alloys, machinability can vary widely based on the specific alloy composition, grain structure, and treatment history.
Different Types of Titanium Alloys
Before delving into the machinability of titanium alloys, it is essential to understand that titanium alloys are broadly classified into three categories:
Let’s investigate some common titanium alloys and their machinability.
Ti-6Al-4V is the most widely used titanium alloy. Its alpha-beta microstructure provides a robust mix of strength and ductility. Here are some key points regarding its machinability:
Grade 23 is a variant of Ti-6Al-4V specifically coated for enhanced biocompatibility, making it popular in medical applications. Its machinability is slightly different:
This is a beta titanium alloy known for high strength and low density. Its machinability can be characterized as follows:
Ti-3Al-2.5V is characterized by its exceptional resistance to corrosion and excellent strength-to-weight ratio.
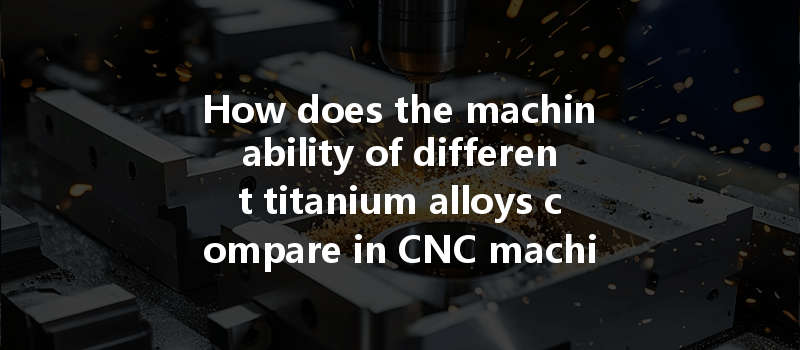
This high-strength beta alloy is notable for its high-temperature capabilities and excellent fatigue strength.
Machinability Parameters
When assessing the machinability of titanium alloys, several parameters are critical:
Challenges in Machining Titanium Alloys
While titanium alloys offer numerous advantages, their machining is not without challenges. Key hurdles include:
Titanium alloys have a propensity for generating heat during machining, which can lead to tool wear and distortion. It’s vital to manage heat through optimized cutting conditions and effective coolant usage.
Titanium’s toughness can lead to rapid wear on cutting tools. It’s vital to select materials that can withstand the stresses involved. Utilizing sharp tools and efficient cooling can mitigate wear rates significantly.
Chips produced from titanium machining can be more problematic than those from conventional materials, leading to blockages and further wear on tools. Employing chip-breaking designs in tooling can alleviate this issue.
Some titanium alloys exhibit work-hardening properties, making them more difficult to machine as the tool progresses through the material. Adjusting cutting parameters to manage this effect is necessary.
Best Practices for Optimal Machining of Titanium Alloys
To ensure successful machining operations, consider the following best practices:
Understanding the machinability of various titanium alloys is critical for any manufacturing scenario involving these unique materials. Each alloy presents its own set of machining characteristics—considerations that can shape project outcomes from cost efficiency to product quality.
At YL Machining, we pride ourselves on staying at the forefront of machining technologies and practices. Equipped with this comprehensive understanding of titanium alloys, you are now ready to make informed decisions regarding your machining processes.
Should you need further assistance or wish to explore titanium machining for your projects, feel free to contact us. Let YL Machining be your trusted partner in tackling even the most challenging projects while optimizing efficiency and quality in your manufacturing operations.
Stay tuned for more insightful articles intended to help you on your machining journey!