Did you know that the choice of metal alloy in CNC machining can have a significant impact on production efficiency, cost, and overall quality? In fact, studies show that selecting the right alloy can enhance machining speed by up to 30%, dramatically affecting the turnaround time for production processes. As industries continue to evolve and demand higher efficiencies, the importance of machinability in various metal alloys is becoming ever more critical.
But what exactly is machinability? It refers to ease of cutting a material into desired shapes and dimensions using machining processes. In CNC machining, different metal alloys exhibit varying levels of machinability, affecting factors such as tool wear, surface finish, and dimensional accuracy. In this article, we will explore how different metal alloys compare in terms of machinability, delve into the factors influencing this characteristic, and provide detailed solutions for optimizing performance based on material selection.
—
Understanding Machinability: The Definition
Machinability is often assessed through several criteria:
With these criteria in mind, it’s important to recognize how different metal alloys interact with machining processes. Let’s take a closer look at how various alloys stack up against each other.
—
Common Metal Alloys Used in CNC Machining
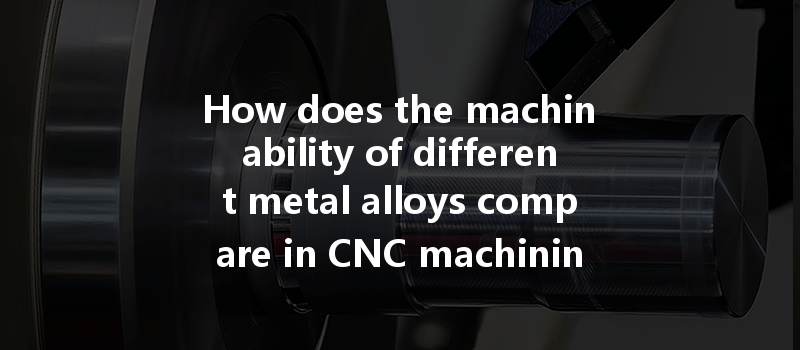
—
Comparing Machinability Factors
When comparing the machinability of different metal alloys, several factors come into play. Here are some of the core aspects that should be considered:
Cutting Tool Material
The type of cutting tool used plays a critical role in machinability. For example, carbide tools are favored when machining harder alloys, as they maintain sharp edges for longer, improving efficiency and surface quality.
Cutting Speed and Feed Rate
Cutting speed refers to how fast the cutting tool engages the material, while feed rate signifies how quickly the tool moves. The proper balance between these two factors leads to efficient cutting, particularly with tougher alloys like titanium or high-carbon steels.
Chip Management
Effective chip management can enhance machining efficiency and tool life. Alloys that produce long chips can lead to issues such as jamming and overheating, while those generating short chips ease chip removal and minimize re-cutting.
Thermal Conductivity
Alloys with higher thermal conductivity dissipate heat more efficiently, reducing wear on cutting tools and improving surface finish. Metals like copper are excellent in this regard, making them easy to machine.
Plasticity and Ductility
Materials that are more ductile, such as aluminum, tend to deform easier and result in better machined parts. Conversely, lower ductility in some steel alloys may lead to chipping or tool wear.
—
Detailed Solutions for Optimizing Machinability Based on Metal Selection
Understanding the intended application and production volume can guide you in selecting the most suitable alloy. Evaluate your product requirements and assess the properties of various metals before finalizing your choice.
Choose tools made of materials suited for the metallic alloys being machined. For harder materials like titanium or high-carbon steels, consider using coated carbide tools designed for high-performance machining.
Adjust cutting speeds and feed rates according to the alloy’s properties. Monitor parameters closely and adjust during machining processes to find the best combination for efficiency and quality.
Utilize steady tooling systems that absorb vibration during the machining process, especially for metals with a tendency to chatter. Enhanced tool stability can drastically improve surface finish and tool life.
Employ effective coolant methods to reduce heat generation. Techniques like through-tool coolant delivery can optimize heat dissipation and enhance tool life, particularly when working with high-temperature alloys.
Implement chip control measures to manage and mitigate chip formation effectively. Use chip breakers on tools and consider incorporating ambient air or coolant blasts to keep chips manageable and away from the cutting zone.
—
In summary, understanding the machinability of different metal alloys is a crucial element for anyone engaged in CNC machining. The choice of material can significantly influence the machining process, affecting tool life, production efficiency, and ultimately, the quality of the finished product. By analyzing key factors affecting machinability, selecting the right materials, and adopting optimal machining practices, manufacturers can not only improve their processes but also enhance product reliability and performance.
As industries continue to demand precision and speed, the importance of choosing the right alloy in CNC machining cannot be overstated. Understanding these dynamics encourages engineers and manufacturers to think critically about their material selections and machining methodologies.
Whether you are a beginner in CNC machining or an experienced professional, this discussion serves to remind you that a well-informed choice in alloy selection positively affects your production process. In today’s fast-paced manufacturing landscape, where quality means everything, considering the machinability of different metal alloys is a cornerstone of effective operations. So, take a moment to reflect on the alloys you’re working with and consider how they can be optimized for better, more efficient outcomes in your machining endeavors.