Did you know that nearly 70% of all metal components are subject to some form of surface treatment to enhance their properties? This highlights the importance of surface finishing techniques such as anodizing and electroplating, especially in CNC machining, where precision and quality are paramount. As manufacturers continuously strive to produce parts that meet stringent quality standards, understanding the nuances of these processes can significantly influence the success of a product.
Understanding Anodizing and Electroplating
Anodizing is an electrochemical process that converts the surface of a metal (usually aluminum) into a decorative, durable, corrosion-resistant anodic oxide finish. This process not only enhances the aesthetic appeal but also improves the metal’s resistance to wear and corrosion.
Electroplating, on the other hand, involves the deposition of a layer of metal onto a substrate through electrolytic solution. This technique is typically used to enhance a product’s corrosion resistance, conductivity, or appearance. Common metals used in electroplating processes include gold, silver, nickel, and chromium.
Both anodizing and electroplating offer valuable attributes but can significantly affect the quality of CNC machined parts in different ways. Let’s delve deeper into how these processes compare and contrast and what implications they have on final product quality.
The Effects of Anodizing and Electroplating on CNC Machined Parts
Anodizing involves the formation of a protective oxide layer on the surface of the metal, enhancing its resistance to corrosion. For instance, aluminum anodized layers can withstand harsh environmental conditions, making them ideal for applications in the aerospace and automotive industries. In contrast, while electroplating can provide good corrosion resistance depending on the metal used, the quality can vary significantly with thickness and condition of the deposit.
Solution: When deciding which method to employ in CNC machining, consider the environmental conditions the part will encounter. For outdoor applications or exposure to harsh chemicals, anodizing may be the more durable option.
The anodizing process enhances surface hardness due to the increased thickness of the oxide layer, improving wear resistance. This is particularly relevant for components used in high-friction applications, as the hardness of anodized aluminum can exceed that of untreated aluminum.
Electroplating can also improve surface hardness but varies widely depending on the type of metal plated and the conditions during plating. For example, nickel electroplating is often used for improving surface hardness; however, it may not achieve the same level as anodized aluminum.
Solution: For parts requiring high wear resistance, such as those in manufacturing machinery, selecting anodizing over electroplating can be beneficial. Always assess part specifications to match the finishing process with the required durability.
The adhesion of further applied coatings or paints can vary between anodized and electroplated surfaces. Anodized surfaces typically provide better adhesion due to the porous nature of the anodic layer. This characteristic is particularly important in industries where secondary coatings are frequently applied, such as automotive and consumer electronics.
Electroplated surfaces may require surface preparation or treatments (like scuffing) to improve adhesion significantly. This step can add to the processing time and cost.
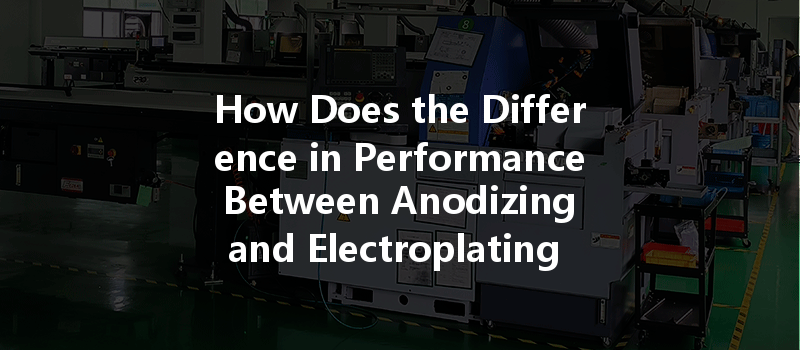
Solution: For components where paint or additional coating is necessary, anodizing might offer a more suitable base due to superior adhesion characteristics.
Appearance matters in many applications, especially in consumer-facing products. Anodized finishes can be dyed in a variety of colors while maintaining their metallic look, providing aesthetic flexibility. It’s worth noting that anodizing allows for a more uniform appearance across mass-produced parts.
Electroplating offers a glossy finish that can enhance the visual appeal of components, particularly in decorative applications. However, the surface can be prone to tarnishing if not adequately protected.
Solution: Consider the visual requirements of the finished product when choosing between the two processes. Anodizing can provide both protection and color variety without sacrificing durability.
An important consideration in many applications, especially in electronics, is the property of conductivity. Anodizing can slightly compromise aluminum’s electrical conductivity due to the oxide layer, making it less suitable for applications requiring optimal conductivity.
Conversely, electroplated layers (particularly those involving copper or silver) offer excellent thermal and electrical conductivity, making them ideal for electrical connections and components.
Solution: If the application demands high electrical or thermal conductivity, opt for electroplating over anodizing.
As industries increasingly adopt sustainable practices, the environmental impact of manufacturing processes must be evaluated. Anodizing is generally considered a greener process since it does not employ hazardous chemicals during surface treatment compared to electroplating, which might involve toxic metals and waste disposal challenges.
Solution: If sustainability is a critical factor in your production, future-oriented organizations may lean toward anodizing processes to minimize environmental footprints.
The choice between anodizing and electroplating for CNC machined parts is not straightforward; each technique comes with its own set of benefits and challenges that affect performance, quality, and environmental implications. By understanding how these finishing processes differ, manufacturers can make informed decisions that improve part quality and functionality.
Ultimately, the proper surface treatment technique should align with part specifications, operational environments, and desired attributes, effectively meeting both performance requirements and aesthetic demands.
In conclusion, whether you lean toward anodizing for its durability and adhesion properties or prefer electroplating for its conductivity and surface finish, it is critical to evaluate the unique requirements of each application. Ultimately, this blog serves as a reminder of the importance of understanding the intricate relationship between surface treatments like anodizing and electroplating and their influence on CNC machined parts’ overall quality.