Did you know that surface hardening treatments can increase the lifespan of components by up to 50%? For manufacturers and engineers, enhancing the durability of machined parts is not just an option but a necessity. This is where surface hardening treatments come into play, especially in the realm of CNC (Computer Numerical Control) machining. As industries push toward more demanding applications, understanding how surface hardening impacts processing effects is crucial.
In this extensive blog, we will explore everything you need to know about surface hardening treatments in CNC processing. From understanding the various methods to their advantages, applications, and impact on part durability, we will break down the complexities involved in this essential topic.
Understanding Surface Hardening Treatment
What is Surface Hardening?
Surface hardening refers to a collection of processes used to increase the hardness of a metal’s surface without altering its core properties. The primary aim is to create a tougher exterior that can withstand wear, abrasion, and fatigue while retaining ductility and toughness in the inner section of the material.
In CNC machining, surface hardening ensures that parts can withstand demanding operational conditions, thus enhancing their functionality and longevity.
Why is Surface Hardening Important?
Methods of Surface Hardening in CNC Machining
CNC machining incorporates several surface hardening treatments, each suitable for different materials and applications. Below, we will discuss some of the most common methods.
Case hardening is a process through which the surface of a metal is hardened while keeping the core soft. The technique involves infusing carbon or nitrogen into the surface layer, leading to the formation of a hardened layer.
Advantages:
Applications:
Nitriding is a heat treatment process that diffuses nitrogen into the surface of a steel part. It is typically performed at lower temperatures than traditional quenching processes, which means minimal distortion and improved wear resistance.
Advantages:
Applications:
Induction hardening is a form of surface hardening that uses high-frequency electromagnetic fields to heat the surface of steel parts quickly and uniformly. Once heated, the part is quenched to form a hardened surface layer.
Advantages:
Applications:
Laser hardening involves using a focused laser beam to heat the surface of a part rapidly to its austenitizing temperature, followed by cooling to create a hardened surface layer. This method provides excellent control over the area being hardened.
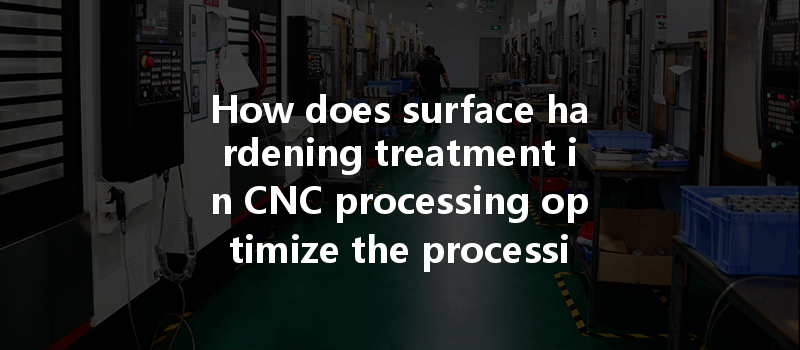
Advantages:
Applications:
Carburizing allows the surface of low-carbon steel to absorb carbon, typically at high temperatures in a carbon-rich environment. When quenched, a hard surface layer forms, providing excellent wear resistance while maintaining a soft core.
Advantages:
Applications:
Optimizing the CNC Machining Process
While surface hardening is crucial, the optimization of the CNC machining process itself is equally important to realize the full potential of surface hardening treatments. Here are some strategies and solutions:
Materials greatly affect the outcome of surface hardening treatments. It is vital to choose base materials that are amenable to the preferred hardening method. For example, steels with a specific content of carbon or alloying elements are best suited for carburizing or nitriding processes.
Optimizing tooling and setup for CNC machining can significantly influence the effectiveness of surface hardening. Ensuring cutting tools are appropriate for the material and that machine settings (such as feed, speed, and temperature) are well-calibrated can reduce wear on both the tools and the parts processed.
Before commencing the machining process, manufacturers can adopt simulation software to visualize and analyze the machining process. This can help identify potential issues, allowing for adjustments to be made in advance, optimizing the machining strategy to fit the needs of surface hardening treatments.
Post-treatment quality control is vital to ensure efficacy. Implementing thorough inspection protocols can help in determining the effectiveness of the hardening process, evaluating surface hardness, and identifying potential failures early on. Techniques such as Rockwell or Vickers hardness testing can be instrumental.
Integrating lean manufacturing principles in CNC machining aimed at surface hardening can help enhance efficiency, reduce waste, and improve turnaround times, all contributing to a more optimized process overall.
Measuring the Impact of Surface Hardening on Part Durability
The effectiveness of surface hardening treatments extends beyond initial performance; it affects the long-term durability and functionality of parts. Measuring these impacts can be achieved through various assessments.
Wear testing provides insights into the longevity of components subjected to friction under various conditions. By analyzing wear rates of surface-hardened parts compared to untreated materials, manufacturers can visually assess the effectiveness of their hardening processes.
Fatigue testing evaluates how parts withstand repeated loads. Surface-hardened components should show significant resistance to fatigue failure, making this a vital measure of part durability.
The evaluation of corrosion resistance in conjunction with surface treatments can be vital for components exposed to harsh environments. Surface hardening methods, such as nitriding, can significantly enhance resistance to corrosion, extending component life in tough conditions.
Case Studies: Success Stories in CNC Surface Hardening Treatments
Case Study 1: Automotive Component Manufacturer
An automotive component manufacturer specializing in gears had been facing issues with premature gear failure. After implementing nitriding as a surface hardening treatment, they observed a 40% increase in gear life and significantly fewer complaints from customers regarding part performance.
Case Study 2: Industrial Machinery Parts Provider
An industrial machinery parts provider employed laser hardening techniques to enhance the performance of mold components. The precision of laser hardening allowed for increased wear resistance while maintaining tight tolerances, resulting in increased productivity and cost savings.
The application of surface hardening treatments in CNC machining represents a critical enhancement for manufacturers seeking to improve the longevity, durability, and performance of their parts. By understanding the various methods available, optimizing the CNC process, and employing strategic quality control measures, it’s possible to achieve remarkable improvements in component effectiveness.
Moreover, the real-life case studies illustrate that organizations adopting these techniques can witness substantial benefits, from higher component lifespans to enhanced customer satisfaction.
As industries continue to encounter rigorous demands for precision and reliability, the importance of surface hardening processes in CNC machining cannot be overstated. Manufacturers need to remain proactive and embrace these technologies, which ultimately lead to optimized production outcomes and reduced operational costs.
In essence, investing thought into surface hardening treatments is not just about enhancing a process; it’s about securing a competitive edge in today’s fast-evolving manufacturing landscape. Therefore, it’s imperative for all stakeholders involved in CNC machining to recognize and leverage the sophisticated techniques outlined in this blog, ensuring that they are prepared to tackle both present and future challenges in part durability and performance.