Did you know that approximately 88% of engineers report experiencing dimensional challenges during their prototype development process? Complex designs, material inconsistencies, and manufacturing tolerances often lead to miscalculations that can derail even the most innovative ideas. In the world of precision engineering, where a mere fraction of a millimeter can make the difference between success and failure, understanding how CNC (Computer Numerical Control) turning can enhance dimensional stability is crucial.
Understanding CNC Turning
CNC turning is a precision machining process that rotates a workpiece against a cutting tool to remove material and create specific shapes and dimensions. This technology has transformed the manufacturing landscape, allowing for exceptional precision, repeatability, and efficiency in producing complex prototypes.
In this blog, we will delve deeper into how CNC turning contributes to the dimensional stability of prototypes. We will explore techniques, processes, tools, and design considerations that make CNC turning an indispensable method in the realm of prototype manufacturing.
Dimensional stability refers to a material’s ability to maintain its shape and measurements under varying conditions. It is a critical factor during the lifecycle of prototypes, particularly in the following areas:
Given these factors, achieving dimensional stability via CNC turning becomes essential.
The CNC turning process involves several key stages:
3.1 Precision Engineering
CNC turning utilizes advanced computer algorithms that dictate the machine’s movements, ensuring that the cutting tool operates with extreme precision. This capability allows manufacturers to achieve tight tolerances, often within a few thousandths of an inch. The precise positioning of the cutting tool reduces errors caused by human operation, leading to a higher degree of accuracy in finished prototypes.
3.2 Material Selection
Choosing the right materials for CNC turning is vital for dimensional stability. Different materials exhibit varying degrees of thermal expansion and contraction, which can affect measurements. Metal alloys, such as aluminum and steel, are popularly selected for their mechanical properties and stability under temperature variations. When designing prototypes, considering the material’s characteristics can mitigate dimensional variances.
3.3 Tooling and Setup
The right tooling is essential for maintaining dimensional stability. The cutting tools’ configuration, angle, and wear can have direct effects on the final dimensions of a prototype. CNC turning often uses multiple types of tools for varied operations, including:
Careful setup before machining, including tool calibration and fixture alignment, ensures consistent cutting and dimensional integrity.
3.4 Speed and Feed Rates
Speed and feed rates play a critical role in CNC turning. The speed (RPM) at which the workpiece rotates, combined with the feed rate (the rate at which the tool moves through the material), directly influences the thermal dynamics of the machining process. Incorrect speeds and feeds can cause tool wear, resulting in inaccuracies. Setting optimal parameters based on material and tool specifications allows for efficient cutting while maintaining dimensional accuracy.
3.5 Environmental Control
Manufacturing environments can significantly affect the stability of prototypes. CNC machines should ideally operate in controlled environments where temperature and humidity are regulated. Fluctuations in environmental conditions can lead to thermal expansion of both materials and machines. Investing in temperature-regulated shop floors can enhance the overall process of CNC turning.
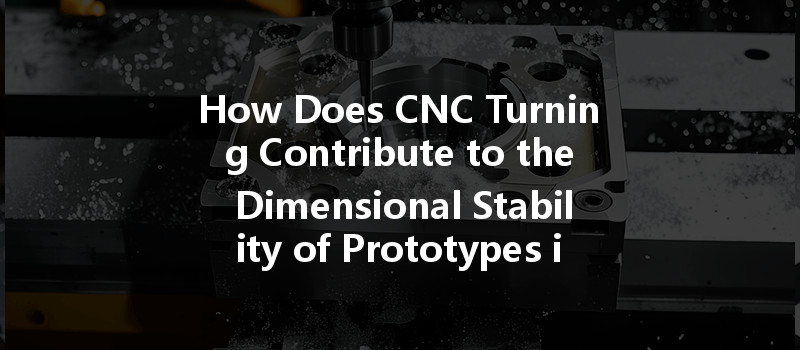
With a solid foundation in CNC turning, manufacturers are continually seeking methods to push the boundaries of dimensional stability. Here, we explore advanced technologies and techniques that optimize the traditional CNC turning process.
4.1 Adaptive Control Systems
Adaptive control systems allow CNC machines to monitor and adjust cutting conditions in real time. By analyzing feedback from sensors, these systems can alter machine parameters to accommodate changes in material behavior, ensuring consistent dimensional outcomes.
4.2 Multi-Axis CNC Turning
Multi-axis CNC turning machines provide greater flexibility and precision by allowing complex movements. Instead of just rotation along one axis, these machines can operate along vertical and horizontal planes as well, enabling the creation of intricate shapes with tight tolerances that are difficult to achieve with traditional methods.
4.3 Finite Element Analysis (FEA)
Employing Finite Element Analysis during the design phase ensures that potential deformation or instability issues can be identified before production. Analyzing how forces will affect the component allows engineers to adapt designs to counteract dimensional instability.
4.4 Computer-Aided Manufacturing (CAM) Integration
Integration between CAD and CAM systems streamlines the transition from design to manufacturing. CAM software can simulate the machining process, allowing engineers to identify and resolve potential dimensional discrepancies before physical production begins.
To illustrate the effectiveness of CNC turning in ensuring dimensional stability, let’s explore a few notable case studies:
Case Study 1: Aerospace Component Manufacturing
In the aerospace industry, a leading manufacturer faced challenges producing turbine components that required incredibly precise dimensional tolerances. By implementing CNC turning and incorporating adaptive control systems, the manufacturer achieved a dimensional accuracy of ±0.005 mm. This success not only improved component performance but also resulted in significant cost savings by reducing rework.
Case Study 2: Medical Device Prototyping
A medical device company developed a new prototype for a surgical instrument that demanded exceptional precision. Using multi-axis CNC turning, the engineering team was able to produce complex geometries with the necessary tolerances. The result was a prototype that passed FDA standards on the first submission, speeding up the time-to-market dramatically.
While CNC turning offers unparalleled advantages in achieving dimensional stability, several challenges persist in the process. Here’s a review of common obstacles, along with potential solutions:
6.1 Tool Wear
Challenge: Over time, cutting tools can wear out, leading to inaccuracies.
Solution: Regularly monitor tool conditions and implement scheduled replacement plans. Employing high-quality, durable materials can also reduce wear rates.
6.2 Programming Errors
Challenge: Programming codes generated for CNC machines are complex and can contain errors.
Solution: Ensure rigorous testing of the programming code using simulation software before actual machining. Conducting thorough inspections post-machining can also help catch errors.
6.3 Inconsistent Material Properties
Challenge: Variations in material properties can lead to unpredictable outcomes.
Solution: Source materials from reputable suppliers and perform thorough pre-inspections to ensure consistency in quality.
The importance of maintaining dimensional stability in prototype manufacturing cannot be understated. CNC turning provides engineers and manufacturers with a robust solution to achieve high precision and consistency in the production of complex geometries. By delving into the techniques, best practices, and advanced technologies discussed in this blog, readers can grasp how CNC turning operates effectively in safeguarding dimensional integrity.
In the fast-paced realm of innovation and engineering, understanding the intricacies of CNC turning offers valuable insights. As we continue to push the limits of design and manufacturing, the adaptability and precision provided by CNC turning will remain central to success.
From aerospace to medical devices, the journey of numerous industries begins with a prototype, and dimensional stability is its backbone. Engaging with this knowledge empowers manufacturers to create better, more reliable products that ultimately enhance our lives. In the world of manufacturing, excellence in prototype production is worth aiming for, and CNC turning may be the tool that gets them there.