Have you ever wondered how intricate brass components—such as those found in musical instruments, plumbing fixtures, or intricate machinery—are created with such precision? In fact, modern machining processes allow for a level of accuracy that was unimaginable just a few decades ago. The rise of Computer Numerical Control (CNC) machining technology has revolutionized the manufacturing landscape, making it possible to produce high-quality brass parts that meet stringent design requirements. In this comprehensive blog, we will explore how CNC machining specifically impacts the accuracy and quality of brass part production processes.
The Evolution of CNC Machining
A Brief History
Computer Numerical Control (CNC) machining emerged in the 1940s and 1950s, primarily in the aerospace and defense industries, where precision was paramount. Early machines relied on punched cards and tape to direct machining tools, which limited their capabilities. However, with advancements in computing technology, CNC machines evolved to allow for more intricate designs and greater automation.
The Role of CNC in Modern Manufacturing
Today, CNC machining involves the use of sophisticated computer software that allows manufacturers to create highly complex parts with impressive speed and accuracy. CNC machines can handle a wide range of materials, including metals, plastics, and composites, but one of the standout materials in CNC machining is brass. Brass is known for its exceptional machinability, corrosion resistance, and aesthetic appeal, making it ideal for various applications.
Why Choose Brass for CNC Machining?
Properties of Brass
Brass is an alloy of copper and zinc, and its various compositions can lead to different characteristics. Here are some reasons why brass is a popular choice for CNC machining:
Applications of CNC Machined Brass Parts
Brass parts are ubiquitous in a range of industries. Common applications include:
How CNC Machining Enhances Accuracy and Quality
Precision Tooling
One of the most significant advantages of CNC machining is its ability to produce parts with tight tolerances. CNC machines operate based on digital designs that dictate every movement of the cutting tool. This means that the margin for error is minimized, resulting in high-precision brass parts.
Advanced Software Solutions
Modern CNC machines utilize sophisticated software that plays a critical role in ensuring accuracy and quality in brass part production. Here are some ways that software aids the machining process:
Use of High-Quality Tools
The right tooling is essential for achieving high-quality brass parts. CNC machining involves various tools, including drills, end mills, and lathes, and the quality of these tools directly influences the final product.
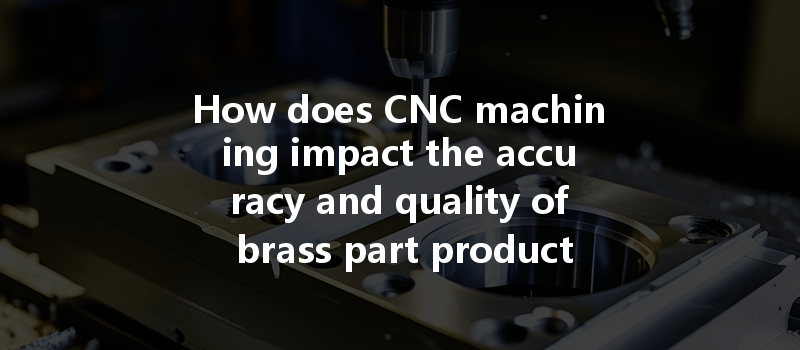
Optimizing Machining Parameters
To achieve the best results in CNC machining brass, several parameters need to be optimized:
Quality Assurance Processes
Quality assurance is vital in CNC machining to ensure that the produced parts meet specifications. Several techniques are implemented:
Challenges in CNC Machining Brass Parts
While CNC machining offers many benefits, it’s not without its challenges. Understanding these can help manufacturers optimize their processes:
Tool Wear and Breakage
Brass can be abrasive, leading to quicker tool wear. Regular tool inspection and replacement are necessary to maintain machining accuracy. Using advanced coatings on tools can also mitigate wear.
Cost Considerations
Savings on larger production runs often come at the cost of initial investment in high-quality CNC machines and software. Manufacturers must weigh the long-term benefits against initial costs.
Supply Chain Management
A reliable supply of quality brass can affect production timelines and costs. Establishing good relationships with suppliers is crucial for ensuring that the right materials are available when needed.
Environmental Considerations
Machining processes can produce waste materials and emissions. New processes and technologies should be evaluated to minimize the environmental impact.
Future Trends in CNC Machining Brass Parts
CNC machining is on the verge of exciting advancements that will further enhance the accuracy and quality of brass parts. Here are a few trends to watch for:
Integration with AI and Machine Learning
Artificial intelligence can help optimize machining processes by learning and predicting the best parameters for tool performance, leading to improved quality and reduced waste.
Sustainable Practices
The machining industry is increasingly focusing on sustainability. Efforts include using environmentally friendly cutting fluids and optimizing production to reduce waste.
Advancements in Additive Manufacturing
While CNC machining remains predominant, the integration of additive manufacturing technologies could complement traditional methods, providing new ways to create complex brass components.
The role of CNC machining in enhancing the accuracy and quality of brass part production cannot be overstated. From its state-of-the-art technology and advanced software solutions to high-quality tooling and comprehensive quality assurance processes, CNC machining has set a new benchmark in manufacturing.
As we look to the future, embracing emerging technologies and sustainability practices will be critical for continuous improvement in CNC machining processes. This blog has highlighted core techniques that not only contribute to the production of high-quality brass parts but also emphasize the importance of precision in modern manufacturing.
In conclusion, considering the ability of CNC machining to produce intricate, high-quality brass components with speed and consistency, it’s essential for manufacturers to embrace these technologies. By doing so, they can meet the growing demands of various industries while maintaining quality and minimizing costs. The journey towards great precision might seem daunting, but with CNC machining, the possibilities are as vast as they are exciting.