Did you know that industries that rely on CNC machining for the production of thin-walled parts are growing at an astonishing rate, projected to reach a valuation of over $100 billion by 2025? Thin-walled components contribute critically to sectors like aerospace, automotive, and consumer electronics, where precision and material efficiency are paramount. But what does it take to ensure that these parts maintain their integrity during the high-stakes CNC machining process? This blog delves into the intricacies of CNC machining for thin-walled parts, providing insights into techniques, materials, and best practices to achieve accuracy and quality.
Understanding Thin-Walled Parts in CNC Machining
Definition and Importance
Thin-walled parts generally refer to components with a wall thickness that is less than 10% of their overall size. These parts are characterized by their lightweight nature, which provides significant advantages in applications where weight reduction is critical. The aerospace and automotive industries, for example, utilize thin-walled structures for components like aircraft fuselages and engine mounts, which must be sturdy yet lightweight.
Challenges in Producing Thin-Walled Parts
Techniques for Maintaining Quality and Accuracy
Machinability Considerations
Selecting the appropriate material plays a vital role in CNC machining thin-walled parts. Materials like aluminum alloys, titanium, and even high-strength plastics are preferred due to their favorable strength-to-weight ratios.
Material Treatments
Consider pre-treatment processes such as annealing or aging, which can optimize the material’s properties prior to machining. For instance, heat treatment can improve ductility, paving the way for better machinability.
Features to Consider
When designing for CNC machining, features such as fillets, ribs, and appropriate wall thickness should be strategically included to enhance the structural integrity of thin-walled components.
Simulation Software
Utilizing CAD (Computer-Aided Design) and CAM (Computer-Aided Manufacturing) software allows for comprehensive simulation of machining processes. This helps in identifying potential issues before actual production.
Choosing the Right Tools
Using specialized cutting tools designed for machining thin-walled materials can significantly reduce the risk of deformation. For example, tools with sharper edges and appropriate geometry are crucial for effective cutting.
Toolpath Optimization
An optimized toolpath reduces the forces applied to the part during machining. Techniques such as adaptive toolpath strategies allow adjustments based on the material removal rate, minimizing the risk of bending.
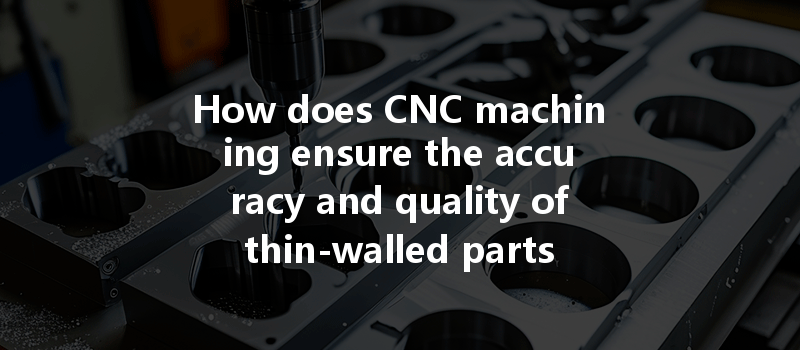
Fixed vs. Variable Feed Rate
Implementing a variable feed rate based on the geometry and thickness of the part can help maintain material integrity during machining. Lower feed rates may be used in critical areas to minimize deformation.
Coolant Usage
Effective use of coolant not only serves to reduce tool wear but also helps maintain thermal stability within the material, further preventing deformation.
Importance of Proper Fixturing
Stability during machining is paramount for thin-walled components. Utilizing advanced fixturing systems that hold the part firmly without applying excessive force can mitigate deformation.
Customized Fixtures
Investing in customized fixtures that align with the unique shape of the part could increase stability and ensure better machining precision.
Real-Time Sensors
Modern CNC machines are often equipped with sensors that monitor cutting forces and vibrations during machining. Incorporating these sensors allows for dynamic adjustments to be made in real-time, enhancing precision.
Feedback Loops
Implement feedback mechanisms that utilize data from the sensors to adjust parameters such as spindle speed and feed rates dynamically.
Inspection Techniques
Using technologies such as coordinate measuring machines (CMM) or laser scanning can allow for accurate dimensional inspection after machining. This is crucial to verify that the component meets tolerance requirements.
Surface Treatment
Post-machining surface treatments, such as anodizing or coating, not only improve aesthetics but can also enhance material properties, reducing the likelihood of deformation during application.
: Striving for Excellence in CNC Machining Thin-Walled Parts
CNC machining of thin-walled parts presents unique challenges that require specialized techniques for successful production. By carefully considering material selection, employing effective design strategies, utilizing optimized machining processes, and integrating advanced monitoring techniques, manufacturers can achieve the high accuracy and exceptional quality they seek.
As we navigate through this thoroughly detailed approach, it becomes clear that the importance of understanding and implementing the aforementioned techniques cannot be overstated. The growth of industries relying on thin-walled components spells importance for optimal machining practices.
In summary, the future of CNC machining lies not only in advanced technology but also in adopting a comprehensive approach, integrating craftsmanship with innovation. Businesses that prioritize these techniques will not only meet but exceed industry standards, ensuring their products are lightweight, reliable, and high-quality—a necessity in today’s ever-evolving market. As you reflect on the insights provided in this blog, consider how your own production processes can evolve to embrace these essential methodologies.