: The Importance of Precision in Manufacturing
Did you know that approximately 35% of all manufacturing costs are attributed to inaccuracies in component production? The significance of precision cannot be overstated, particularly in industries such as aerospace, automotive, and medical devices, where even the smallest deviation can lead to catastrophic results. One of the most effective solutions to achieve that precision is through Computer Numerical Control (CNC) machining. This process revolutionizes manufacturing by converting precise digital designs into actual parts with remarkable accuracy. But how does CNC machining ensure the accuracy and consistency of its produced components?
In this comprehensive blog, we will delve into the world of CNC machining, exploring its various features, technologies, and techniques to provide you with a deeper understanding of how it achieves unmatched precision and consistency.
Section 1: Understanding CNC Machining
1.1 What is CNC Machining?
CNC machining is an automated manufacturing process that utilizes computerized controls to operate machinery such as mills, lathes, routers, and grinders. Unlike traditional manual machining, which relies heavily on human dexterity and skill, CNC machining operates based on pre-programmed computer software, ensuring precise movements and consistent results.
1.2 The Components of CNC Systems
A CNC machine comprises several essential components:
Section 2: CNC Machining Process and Techniques
2.1 The CNC Machining Workflow
The CNC machining process can be broken down into several stages:
2.2 Types of CNC Machining Techniques
CNC machining encompasses various techniques, each suited to different applications:
Section 3: How CNC Machining Ensures Accuracy and Consistency
3.1 Quality Control Measures
CNC machining incorporates multiple quality control measures at various stages to maintain accuracy and consistency:
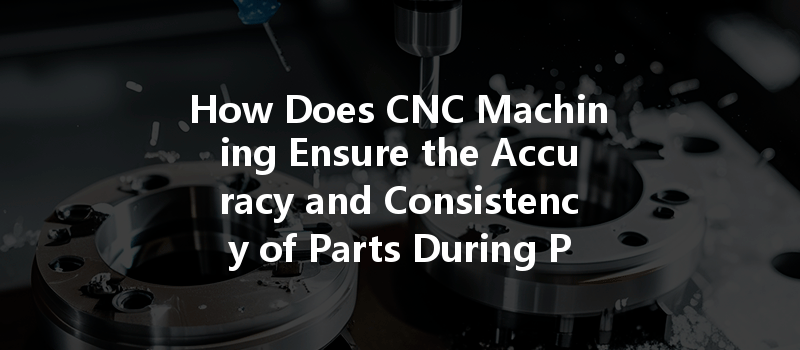
3.2 Tolerance Management
CNC machining processes often achieve tolerances within ±0.001 inches or even tighter, depending on the machinery and materials used.
3.3 Material Considerations
Selecting the right material for CNC machining can significantly impact the accuracy and consistency of the final product. Key factors include:
Section 4: Advanced Technologies Enhancing CNC Accuracy
4.1 Optical and Laser Measurement
Emerging technologies, such as optical and laser measurement systems, provide highly accurate assessments of part dimensions, monitoring changes during machining, and ensuring real-time adjustments.
4.2 Artificial Intelligence (AI) in CNC Machining
AI-driven machine learning algorithms can analyze vast amounts of data relating to machining processes to optimize settings and predict maintenance needs.
Section 5: Challenges and Solutions in Achieving Precision
5.1 Challenges
While CNC machining offers numerous advantages in accuracy and consistency, there are still challenges:
5.2 Solutions
Section 6: Case Studies
6.1 Aerospace Industry
In the aerospace industry, CNC machining is crucial for producing high-precision components, such as turbine blades. The combination of advanced materials and CNC processes allows for the fabrication of complex geometries that meet stringent aerospace standards.
6.2 Medical Device Manufacturing
Medical devices demand extreme accuracy in their manufacturing processes due to their direct impact on patients. CNC machining has played a pivotal role in producing highly consistent parts that meet regulatory compliance while focusing on reliability.
: The CNC Advantage in Precision Machining
To summarize, CNC machining is a cornerstone of modern manufacturing due to its ability to ensure accuracy and consistency of parts during production. By leveraging advanced technologies, continued quality control measures, and careful material selection, CNC machining offers an unparalleled solution to the challenges associated with traditional manufacturing processes.
As industries continue to demand higher precision and efficiency, the relevance of CNC machining will only grow. Understanding these core techniques and implementing best practices can lead to significant performance improvements in manufacturing operations.
CNC machining not only minimizes waste and reduces costs but also enhances the reputation of manufacturers by ensuring that every product meets stringent quality and performance standards. For anyone in the manufacturing sector, recognizing the importance of accuracy and consistency in CNC machining is not just advantageous; it’s essential for thriving in a competitive landscape.