Did you know that modern CNC machining can achieve tolerances as tight as ±0.002 inches? In the fast-paced world of manufacturing, precision is not just a luxury; it is a necessity. Many industries, including aerospace, automotive, and medical device manufacturing, depend heavily on the ability to produce components that meet exact specifications. In this article, we will dive deep into the world of CNC (Computer Numerical Control) machining, examining how it ensures consistent precision and dimensional tolerances in mass production. We will analyze the methods, technologies, and best practices that make CNC machining an indispensable asset for manufacturers.
CNC machining refers to a manufacturing process where pre-programmed computer software dictates the movement of factory tools and machinery, replacing the need for manual control. This technology not only improves precision but also enhances productivity and efficiency. The popularity of CNC machining has surged due to its ability to produce high-quality parts with minimal human intervention, making it a reliable asset for numerous applications.
1.1 The Process of CNC Machining
The CNC machining process typically includes several stages:
1.2 Importance of Precision and Dimensional Tolerances
Precision in CNC machining is crucial because even minor variations in dimensions can lead to significant problems during assembly or operation. Industries that require high precision include:
Several techniques and technologies help CNC machining achieve the desired precision and dimensional tolerances. Understanding these techniques aids in optimizing machining processes and maintaining high-quality standards.
2.1 Rigid and Stable Machines
The foundation of precision in CNC machining starts with the machines themselves. CNC machines must be rigid and stable to withstand the forces generated during cutting. Key considerations include:
2.2 Advanced Tooling and Cutting Techniques
The right tools play a critical role in ensuring dimensional accuracy. Advanced machining techniques and tool technologies contribute significantly to achieving desired tolerances:
2.3 Regular Maintenance and Calibration
Like any piece of complex machinery, CNC machines need regular maintenance, calibration, and inspection. This essential practice ensures that the machinery continues to operate at high precision. Key points include:
2.4 Advanced Software Solutions
Modern CNC machines come equipped with sophisticated software that enhances precision machining by providing:
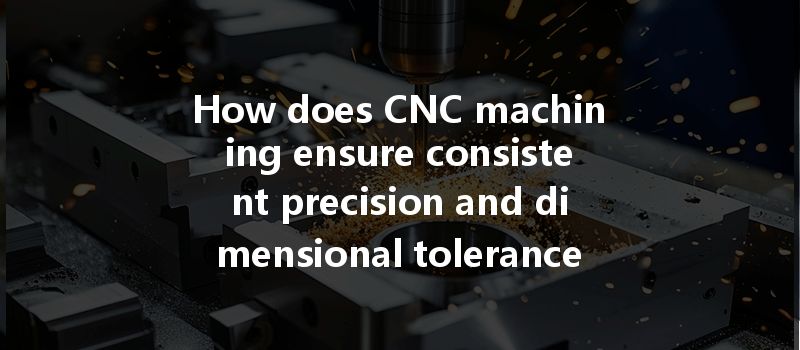
2.5 Quality Assurance Techniques
Quality assurance protocols are integral to maintaining precision in mass production. These techniques ensure that parts meet specified dimensional tolerances consistently throughout the manufacturing process. Important methods include:
Despite the advancements in CNC machining technology, numerous challenges can impact precision and dimensional tolerances during mass production.
3.1 Material Variability
Different materials exhibit various physical properties and behaviors during machining. Material changes, such as inconsistent density, can affect the machining process. Strategies to mitigate these issues include:
3.2 Human Influence
Even though CNC systems are automated, human intervention is still often required. Operator skill, training, and experience play a critical role in maintaining production quality. Solutions for mitigating human factors include:
3.3 Environmental Factors
Temperature and humidity can affect both machines and materials during production. Variables like thermal expansion can lead to changes in dimensions. Steps to counter environmental effects include:
To ensure high precision and consistent dimensional tolerances in mass production, manufacturers should implement the following best practices:
4.1 Automation and Control Systems
Investing in automated systems for manufacturing can significantly enhance precision. Automation reduces operator-induced errors and provides consistent production rates.
4.2 Continuous Improvement Methodologies
Embrace continuous improvement methodologies such as Lean and Six Sigma to identify inefficiencies and enhance production processes. Regularly seek feedback from operators and implement changes to improve precision.
4.3 Robust Documentation Systems
Maintaining meticulous records across all processes—including CAD designs, machine settings, and quality inspections—allows for tracking issues and understanding performance trends.
4.4 Supplier Management
Assess and select suppliers based on their ability to provide consistent material quality. Effective supplier management can mitigate variability in the raw materials used for CNC machining.
4.5 Collaboration Across Departments
Fostering collaboration among design, engineering, and production teams allows for proactive problem-solving and minimizes risks that can affect precision.
Achieving consistent precision and dimensional tolerances in CNC machining is a multifaceted endeavor involving advanced technology, skilled operators, and meticulous processes. By focusing on the techniques and best practices outlined in this article, manufacturers can consistently produce high-quality parts that meet stringent industry standards.
As industries evolve and demand for precision manufacturing increases, understanding how CNC machining ensures tolerances takes on newfound importance. The integration of state-of-the-art technology, continuous improvements, and robust quality assurance techniques solidifies CNC machining as an indispensable component of modern manufacturing.
In summary, ensuring consistent precision is not merely a goal; it is a commitment to quality that shapes the future of manufacturing. As we continue to innovate and refine these processes, the potential for CNC machining to enhance product performance and reliability remains immense. By considering these strategies and practices, organizations can thrive in an ever-demanding manufacturing landscape—one that consistently values precision.
This blog serves as a reminder of the importance of precision in CNC machining and why it deserves careful thought in every manufacturing operation. Whether you are an industry professional or a curious newcomer, understanding these principles can lead to more successful and quality-oriented production processes.