Did you know that aluminum is the second most widely used metal in the world, after steel? This lightweight and versatile material accounts for nearly 8% of the weight of the Earth’s crust, making it readily available for countless applications—from aerospace to automotive and everything in between. The growing demand for precision aluminum parts in custom applications is challenging manufacturers to innovate and optimize their processes. In this blog, we will delve deep into CNC (Computer Numerical Control) machining and its significant role in enhancing the precision of aluminum parts for custom applications. We will explore techniques, technologies, challenges, and detailed solutions that make CNC machining your go-to method for achieving high-precision results.
The Growing Need for Precision Machining
Rising Demand
As industries evolve and technological advancements emerge, the demand for precision components is at an all-time high. Industries such as aerospace, automotive, and medical are particularly stringent regarding quality, tolerances, and reliability. For instance, in aerospace manufacturing, even the slightest deviation can lead to catastrophic failures. Therefore, employing high-precision manufacturing methods is crucial.
The Role of CNC Machining
CNC machining stands out as the preferred technology for manufacturing precision aluminum parts. Unlike traditional machining, where manual controls can introduce variations due to human error, CNC machining utilizes computer algorithms and automated machinery to produce parts with exceptional precision.
Understanding CNC Machining
What Is CNC Machining?
CNC machining is a subtractive manufacturing process that uses computer-controlled machines to cut, mill, or shape materials according to exact specifications. A CAD (Computer-Aided Design) file is input into the machine, which then interprets the model and produces the final part with high accuracy. CNC machines include lathes, mills, routers, and electrical discharge machines (EDMs), among others.
Benefits of CNC Machining for Aluminum Parts
Techniques in CNC Machining for Precision Aluminum Parts
One of the initial steps in ensuring precision is selecting the appropriate aluminum alloy for your application. Different alloys exhibit varying properties, such as strength, corrosion resistance, and formability. For example, Aluminum 6061 and 7075 are widely used for CNC machining due to their mechanical properties and adaptability for high precision applications.
The type of tools employed in CNC machining plays a vital role in achieving precision. High-speed steel (HSS) and carbide tools provide varying degrees of hardness and durability, impacting the quality of the cut and the finished part. Special coatings, such as titanium nitride (TiN), can be applied to extend tool life and enhance performance.
Programming is essential for determining how the CNC machine will operate. Advanced software can simulate the machining process, allowing engineers to identify potential errors in the design and improve the toolpath before actual machining takes place. This minimizing downtime and errors subsequently translates into higher precision.
Quality control measures in CNC machining involve continuous monitoring of the machining process and final products. Using CMM (Coordinate Measuring Machines) and other inspection tools, manufacturers can ensure components meet established tolerances and specifications.
Common Challenges in CNC Machining of Aluminum Parts
While CNC machining has significantly advanced the manufacturing of precision aluminum components, several challenges persist:
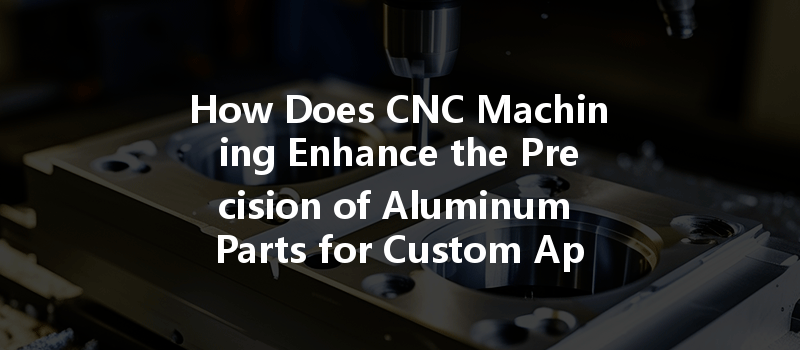
Although CNC tools are designed for durability, they experience wear over time, impacting the precision of machined parts. Regular maintenance, tool replacement, and the selection of appropriate tooling can mitigate this issue.
Aluminum is prone to thermal expansion, and excessive heat generated during machining can cause dimensional changes. Implementing coolant systems and monitoring cutting speeds can help maintain a stable temperature.
Programming errors or software glitches can lead to deviations from the intended design. Regular training for operators and software updates are essential to minimize these risks.
Implementing Solutions for Optimal CNC Machining
To achieve precision, investing in high-quality CNC machines and tools is non-negotiable. These machines should have the latest technology for enhanced performance and accuracy.
Continuous training for CNC operators is crucial for maintaining quality and precision. Knowledgeable operators can recognize potential issues in the machining process and take corrective actions effectively.
Using methodologies like Six Sigma can help eliminate waste and optimize manufacturing processes. A commitment to continual progress ensures that precision is maintained as technologies evolve.
Collaboration between CNC machinists and engineers ensures that designs are feasible for CNC machining. Engineers can provide insights on tolerances and production methods to maximize precision during the manufacturing process.
Future Innovations in CNC Machining
As we look towards the future, various innovations in CNC machining are expected to further enhance precision:
The Internet of Things (IoT) can provide real-time monitoring and data analytics, allowing manufacturers to measure performance, adjust processes, and optimize production dynamically.
Artificial Intelligence can improve CNC programming by predicting tool wear and optimizing machining paths, resulting in greater precision and time savings.
Automated systems and robotics will streamline machining processes while providing consistent quality, reducing the chances of human error.
In summary, CNC machining has revolutionized the manufacturing of precision aluminum parts, addressing the growing demands of various industries for high-quality, reliable components. By choosing the right materials, utilizing advanced tooling, and implementing rigorous quality control, manufacturers can achieve exceptional precision in their custom applications.
Given the complexity and challenges that come with precision machining, it is evident that investing in quality practices, technology, and skill development is essential. As industries continue to evolve, the techniques and solutions discussed in this blog will only become more critical in ensuring precision in CNC machining.
Reflecting on the importance of this knowledge, consider the far-reaching implications of precision-aluminum parts in your industry and manufacturing processes. With the right approach, embracing CNC machining can lead to not just survival, but success in today’s competitive market.