Did you know that the demand for high-temperature alloys in various industries—such as aerospace, automotive, and energy—is projected to reach $21.03 billion by 2025? These materials are critical in applications that require exceptional performance under extreme conditions, but they also present unique challenges when it comes to machining.
In this blog, we’ll delve deep into the intricacies of evaluating the machinability of high-temperature alloys in CNC machining. This guide aims to provide you with practical insights and comprehensive solutions to overcome the challenges associated with machining these advanced materials.
—
Understanding High-Temperature Alloys
Before we jump into evaluation methods, let’s clarify what high-temperature alloys are and why they matter.
Definition and Composition
High-temperature alloys are designed to withstand extreme temperatures, typically above 500°F (260°C). They are engineered to maintain their mechanical properties, such as strength and corrosion resistance, even when subject to prolonged exposure to high temperatures. The most common types include:
Applications
These alloys are extensively used in industries such as:
—
The Importance of Machinability Evaluation
Machinability refers to the ease with which a material can be machined to desired specifications. Evaluating the machinability of high-temperature alloys is crucial for several reasons:
—
Key Factors Influencing Machinability
The machinability of high-temperature alloys is influenced by several interrelated factors:
—
Methods for Evaluating Machinability
Conducting empirical cutting tests can provide valuable data. These tests should include:
Key performance indicators (KPIs) to consider include:
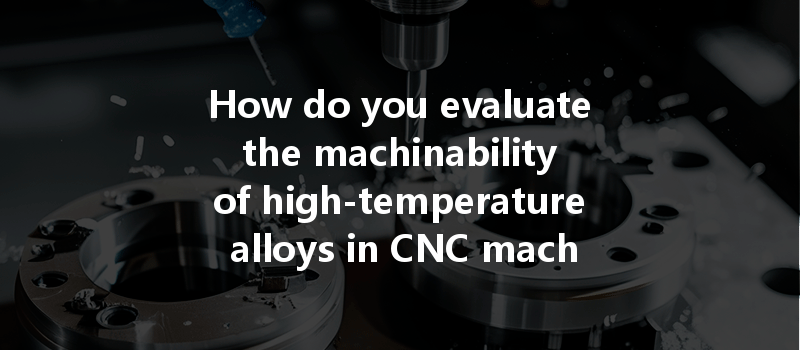
Proper tool selection is vital in successfully machining high-temperature alloys. Points to consider include:
Adjusting machine parameters can yield significant improvements in machining performance. These parameters can include:
—
Addressing Challenges in Machining High-Temperature Alloys
Despite the advantages of high-temperature alloys, they pose unique challenges during machining. Below, we’ll cover solutions for overcoming common issues:
Solution: Using advanced cutting tools with specialized coatings can help combat abrasion and extend tool life. Regular tool inspection and replacement are also essential.
Solution: To achieve a better surface finish, consider using smaller depths of cut and higher speeds. Adjust the feed rate to optimize chip removal and surface integrity.
Solution: Optimize cutting parameters by performing pre-tests to identify ideal combinations of speed, feed, and depth for the alloy being machined.
Solution: Employ a forced cooling system or rethink chip breaking strategies to manage swarf removal.
—
Best Practices for Machining High-Temperature Alloys
Implementing a series of best practices can dramatically improve machining outcomes:
—
In conclusion, evaluating the machinability of high-temperature alloys in CNC machining requires a comprehensive understanding of the materials, vigilant adjustment of machining parameters, and implementation of best practices such as tooling and process optimization.
As industries increasingly turn to advanced materials for performance improvements, mastering the intricacies of CNC machining high-temperature alloys will not only enhance production efficiency but also ensure superior product quality.
This blog serves as a vital resource for manufacturers looking to navigate the complexities of machining high-temperature alloys effectively. Reflecting on the discussed techniques can lead to significant improvements in both process efficiency and cost-effectiveness. Equip yourself with this knowledge and remain at the forefront of modern manufacturing.
—