Did you know that brass accounts for nearly 80% of all copper alloys used in manufacturing in the United States? With its unique properties, such as durability, corrosion resistance, and excellent machinability, brass is a preferred choice across various industries, from plumbing to electronics. However, selecting the appropriate brass material for CNC machining can be a complex process that significantly affects the quality and performance of the final product. In this comprehensive guide, we will walk you through the essential factors to consider when choosing brass materials for CNC machining, along with practical solutions to ensure optimal performance.
Understanding Brass and Its Properties
Before diving into the specifics of CNC machining and its relationship with brass materials, it’s vital to understand what brass is and why it’s a popular choice.
Brass is an alloy primarily composed of copper and zinc. The proportions of these elements can be adjusted to achieve various mechanical properties, corrosion resistance, and aesthetic qualities. Here are some key properties of brass that make it suitable for CNC machining:
Given these properties, it’s clear that brass can be a valuable material in CNC machining. However, how do you select the right variant of brass for your specific application?
Factors to Consider When Choosing Brass for CNC Machining
Different brass alloys exhibit varying mechanical properties. Some variants might provide higher tensile strength, while others may be more malleable. When selecting brass material, consider the following mechanical properties:
Tensile Strength: Measure of the material’s ability to withstand pulling forces.
Yield Strength: Defines the point at which the material begins to deform permanently.
Hardness: Determines the material’s resistance to deformation.
Elongation: Indicates how much strain a material can handle before it breaks.
High-strength brass alloys might be necessary for load-bearing components, while softer variants may be preferable for detailed, intricate designs.
Brass comes in various compositions, each tailored for specific applications. Some common types include:
C26000 (Cartridge Brass): Contains approximately 70% copper and 30% zinc. This alloy offers excellent cold-working capabilities and good corrosion resistance, making it suitable for tightly toleranced parts.
C36000 (Free-Cutting Brass): Known for its excellent machinability, it contains about 63% copper and 37% zinc. This brass is commonly used for automatic screw machines.
C46400 (Naval Brass): Contains copper, zinc, and a small percentage of tin, giving it superior corrosion resistance and strength, particularly in marine environments.
Identifying the specific requirements of your project will help you select the best composition.
Understanding the end application is crucial when selecting brass. Different applications may require different properties:
Plumbing Fixtures: May require corrosion resistance and strength.
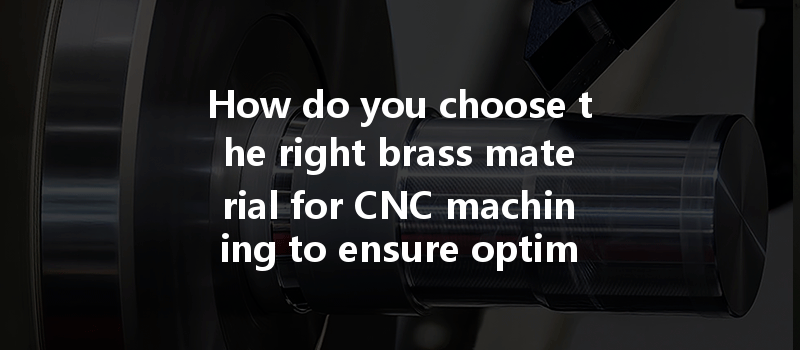
Electronic Connectors: Might necessitate conductivity alongside resistance to tarnishing.
Ornamental Parts: Aesthetic appeal may take precedence over mechanical strength.
Considerations during the CNC machining process can greatly influence the choice of brass material. Here are key factors:
Cutting Speed and Tooling: Some alloys can better withstand high speeds. Free-cutting brass can allow for faster machining rates.
Tool Wear: Some brass materials can cause more tool wear than others. It’s important to choose alloy compositions that align with your machining capabilities.
* Surface Finish: If a specific surface finish is necessary, some brass alloys may be more amenable and will require additional treatment post-machining.
Finally, it’s essential to consider the cost. Brass prices can vary based on alloy composition and current market conditions. While high-performance materials may be more expensive, they can save costs in the long run by reducing machining times and waste.
Practical Solutions for Choosing Brass Material
Now that we’ve outlined the critical factors, let’s discuss practical strategies to help you choose the right brass material for CNC machining:
Step 1: Define the Requirements
Before beginning the selection process, it’s essential to define the requirements of your project clearly. Gather input from stakeholders, engineers, and designers to understand what properties are most critical for your application.
Step 2: Research Brass Alloys
With a clear understanding of requirements, research various brass alloys. Consult material databases or manufacturer specifications to compare the mechanical properties and compositions of different alloys.
Step 3: Consult Machining Experts
Engage with manufacturing and machining experts. They can provide insights into which alloys work best with specific CNC machining processes and tooling. They may also share experiences regarding machining of various brass compositions.
Step 4: Experimentation
Consider conducting small prototype runs with different brass alloys to assess their performance under machining conditions. This practical experimentation can yield invaluable insights regarding the machinability and finish of each alloy.
Step 5: Review Cost and Availability
Once you have narrowed your options down to a few alloys, review their costs and availability from suppliers. Ensure your choice aligns with both your budget and the project timeline.
Step 6: Make an Informed Decision
Armed with all the gathered data, make a decision. Remember that the right choice may yield dividends not only in terms of product performance but also in timelines and costs.
Choosing the right brass material for CNC machining is pivotal in ensuring optimal performance and longevity of the final product. By considering mechanical properties, alloy composition, application requirements, machining characteristics, and cost factors, you can make a well-informed decision that meets your specific needs.
In the competitive world of manufacturing, the choice of material can make a profound difference in quality, efficiency, and durability. Remember to use the practical steps outlined in this guide when navigating your brass selections.
Reflect on the impact of your decisions—choosing the right brass material is not merely a technical choice, but a critical step towards achieving manufacturing excellence. As you move forward, keep in mind that the right material choice today can lead to significant advantages in performance, cost savings, and customer satisfaction down the line.