*
In the ever-evolving landscape of manufacturing, Computer Numerical Control (CNC) machining stands out as a cornerstone technology that harnesses precision, efficiency, and innovation. At the forefront of this movement is YL Machining, a leader in deploying advanced CNC techniques to produce high-quality parts across various industries. In this article, we will dive deep into a critical question: How do specific material properties impact the CNC machining process and its outcomes?
At YL Machining, we understand that the material properties of the components we work with can be the defining factors in achieving the desired quality, efficiency, and cost-effectiveness in our machining processes. From metals to plastics, each material presents unique characteristics that influence everything from cutting speed to tool selection, and ultimately, the final product’s performance. This comprehensive guide will dissect these material properties in detail and reveal how they shape our CNC machining strategies.
What is CNC Machining?
CNC machining is a subtractive manufacturing process that uses computer-controlled machines to cut, shape, and form materials into precise parts. Utilizing CAD (Computer-Aided Design) files, CNC machines follow programmed commands to perform a variety of operations, including milling, turning, drilling, and grinding.
Key Components of CNC Machining
The fundamental components of CNC machining include:
To truly grasp how material properties influence CNC machining outcomes, it’s essential to break down these properties into manageable categories.
Physical Properties
These are the observable characteristics of a material, including:
Mechanical Properties
Mechanical properties describe how materials react under various forces or loads:
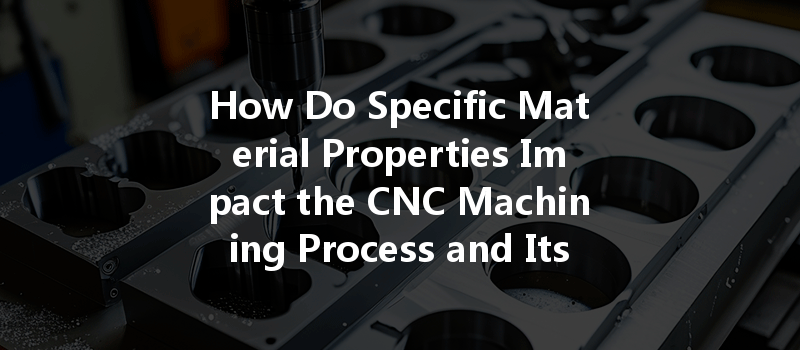
Thermal Properties
These properties denote how materials behave when exposed to heat:
Chemical Properties
Chemical properties refer to a material’s ability to withstand environmental factors:
Understanding how specific material properties affect CNC machining is paramount to achieving optimal results.
Influence on Cutting Tools
The choice of cutting tools is often contingent on the material being machined. Harder materials such as titanium require high-speed steel or carbide tools with sufficient robustness to withstand wear.
Effects on Cutting Speeds
Materials with lower hardness can be machined at higher speeds. For instance, aluminum allows for faster machining rates than steel. Understanding these nuances helps CNC operators optimize production times.
Implications for Surface Finish
The material composition largely impacts the resulting surface finish. Softer materials like plastics often result in smoother finishes, while harder materials may require additional processes to achieve similar results.
Considerations for Tool Wear and Life
Tool wear rates can significantly differ based on the material. For instance, machining high-carbon steels can lead to rapid tool wear, which must be factored into production schedules and budgets.
Different categories of materials exhibit unique properties that directly influence how they are machined.
Metals and Alloys
Plastics
Plastics vary dramatically; for instance, POM (polyoxymethylene) boasts excellent wear resistance, while PET (polyethylene terephthalate) is not as strong but is easier to process. Each plastic type demands unique tooling and cutting strategies.
Composites
Composite materials often exhibit complex machining requirements due to their layered structure. Machining may involve multiple processes to ensure a quality finish on both filament fibers and bonding matrices.
When choosing a material for CNC machining, consider:
Analyzing Design Requirements
Ensure the selected material aligns with the functional requirements of the final product. Consider load-bearing capabilities, aesthetic qualities, and environmental tolerance.
Balancing Cost and Performance
Cost-effectiveness remains critical. Evaluate the trade-offs between material selection, machining processes, and desired performance outcomes.
Steel and Aluminum CNC Machining
At YL Machining, our expertise in CNC machining has allowed us to navigate the complexities of both steel and aluminum. While steel offers unmatched strength and durability, aluminum’s lightweight characteristics make it ideal for aerospace applications.
Precision Machining of Plastics
We have also engaged in the precision machining of various plastics, focusing on the unique properties that each material possesses. Successfully achieving optimal surface finishes in polycarbonate and POM has increased our competitive edge in the market.
As we look towards the future, several exciting trends emerge:
Innovations on the Horizon
Emerging technologies, such as additive manufacturing and smart materials, promise to revolutionize machining processes, opening doors to innovative applications and uncharted territories in manufacturing.
The Role of Smart Materials
Smart materials capable of adapting to their environments pave the way for intelligent design in sensitive and high-precision industries.
Understanding the relationship between material properties and CNC machining is essential for manufacturers aiming for excellence. At YL Machining, we are committed to meticulously evaluating material characteristics and employing cutting-edge techniques to produce precision parts for our clients across various sectors.
As we forge ahead in our pursuit of innovation and excellence, we invite you to join us in exploring the limitless potential of CNC machining. The intersection of material properties, technology, and creativity is where we can truly elevate manufacturing practices and outcomes for the better.
Your journey to exceptional quality and performance begins with YL Machining—where material science meets operational precision.*