—
Welcome to the world of precision engineering; welcome to YL Machining! As you navigate through this ever-evolving landscape, you will discover the remarkable intricacies of CNC (Computer Numerical Control) machining. This technology has become fundamental in manufacturing, beloved for its ability to deliver consistency, precision, and efficiency. But herein lies a question that echoes through workshops and factories: How do specific material properties affect the CNC machining process?
In this article, we will embark on an extensive journey of exploration, dissecting not just the “what” but the “how” and “why.” Through clear and structured exploration, we’ll uncover the myriad factors that dictate machining performance, the nuances of various materials, and the implications for manufacturers like you. With insights that range from the basics to intricate technicalities, you’ll be better equipped to make informed decisions. So, grab a cup of coffee; let’s start the journey!
—
Chapter 1: Understanding CNC Machining
Before we delve into the specifics of material properties, let’s lay a foundational understanding of CNC machining.
1.1 What is CNC Machining?
CNC machining is a form of subtractive manufacturing where pre-programmed computer software controls the movement of machinery and tools. This process is responsible for automating the control of machining tools—including lathes, mills, and grinders. With CNC machining, you can produce components with tight tolerances and complex geometries.
1.2 Key Advantages of CNC Machining
—
Chapter 2: The Interplay of Material Properties and Machining
Now that we have a grasp of CNC machining, let’s examine how specific material properties influence the machining process.
2.1 Mechanical Properties
The mechanical properties of materials directly impact how they respond to machining operations. Let’s explore these properties in detail.
2.2 Thermal Properties
Thermal properties, including thermal conductivity and thermal expansion, also affect CNC machining processes.
2.3 Chemical Properties
Material properties such as corrosion resistance and reactivity are crucial in selecting the right materials for CNC machining.
—
Chapter 3: Material Selection Matrix
With our understanding of how properties influence machining, let’s create a comprehensive material selection matrix. This matrix categorizes materials based on specific machining conditions, providing a tailored approach to CNC machining operations.
| Material | Hardness | Toughness | Ductility | Thermal Conductivity | Corrosion Resistance | Recommended Machining Method |
|———————|————–|—————|—————|————————–|————————–|————————————|
| Aluminum 6061 | Medium | High | Very High | Medium | Good | High-Speed Machining |
| 4140 Steel | High | Medium | Medium | Low | Fair | Conventional Machining |
| Titanium Alloys | Very High | Low | Medium | Medium | Good | Specialized CNC |
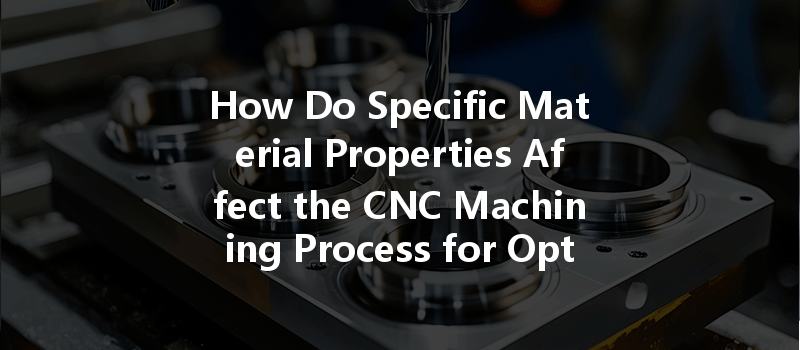
| Stainless Steel 316 | Medium | Medium | Low | Low | Very High | Slow, Controlled Machining |
| Copper | Medium | High | Very High | Very High | Fair | Precision Machining |
—
Chapter 4: Tools and Techniques
Proper tooling and methodologies are integral to overcoming challenges posed by different material properties.
4.1 Tool Selection
The choice of tool is directly influenced by the material’s properties. Here are key considerations:
4.2 Machining Techniques
Utilizing the appropriate machining techniques can drastically affect the outcome of the machining operation.
—
Chapter 5: Practical Implications for Manufacturers
Understanding the interplay between material properties and the CNC machining process directly translates to manufacturing efficiencies and competitiveness. Manufacturers can benefit significantly from this knowledge through several avenues.
5.1 Cost Savings
Choosing the right materials and tools can dramatically reduce cycle times and tool wear, leading to significant cost savings. For instance, replacing conventional tools with coated alternatives can increase tool life by up to 300%, thereby reducing replacement costs.
5.2 Quality Control
Implementing rigorous quality control processes at the intersection of material properties and machining practices can help reduce defects, yielding higher quality products and improved customer satisfaction.
5.3 Innovation and R&D
Continued research and development into material science opens opportunities for manufacturers to utilize emergent materials that can offer superior properties. Exploring novel composites and alloys can offer competitive advantages in specialized industries.
—
Chapter 6: Case Studies
To solidify our understanding, let’s explore a couple of case studies that illustrate the impact of material properties on CNC machining.
6.1 Case Study 1: Aluminum in Aerospace
A premier aerospace company faced challenges with machining aluminum alloy 7075, known for its high strength but also low machinability. By utilizing advanced milling strategies and using coated carbide tools, the company was able to improve its machining efficiency by 40%, significantly reducing production costs.
6.2 Case Study 2: Titanium Components
A medical device manufacturer required precise titanium components with stringent tolerance requirements. Through specialized high-speed machining and the implementation of a vaporization coolant, they achieved an impressive 30% reduction in cycle times while maintaining the integrity of the parts.
—
In summary, specific material properties exert a profound influence on the CNC machining process. Understanding these properties allows manufacturers to select the right materials and tailor their machining practices to achieve optimal performance.
At YL Machining, we embrace these complexities to deliver precision-engineered components tailored to your unique specifications. Our commitment to innovation, quality, and efficiency assures our partners of unparalleled results in every machining project.
Whether you are a seasoned engineer or a newcomer to the world of machining, the insights shared in this article are meant to enlighten and inspire. Remember, the key to machining excellence lies not just in technology but in an intimate understanding of the materials we work with.
—
At YL Machining, we specialize in high-precision CNC machining, ensuring that quality and precision meet your manufacturing needs. Our mission is to provide innovative solutions tailored to the demands of multiple industries while upholding the highest standards of craftsmanship. Contact us today to explore how we can assist you in achieving machining excellence!
—
This concludes our deep dive into the interaction of material properties and CNC machining processes. By understanding these elements, you are better equipped to tackle challenges that arise in the machining world and drive your projects toward success. Thank you for joining us on this journey!