Opening:
Did you know that in the fast-paced world of CNC (Computer Numerical Control) manufacturing, a staggering 70% of manufacturers report that agile order management is critical to their success? In an age where expectations for swift delivery and accurate updates are at an all-time high, the ability to track order progress in real time has become not just beneficial but essential. In this blog, we will delve deep into the innovative solutions that CNC processing manufacturers employ to ensure that both they and their customers are always in the loop regarding order status.
CNC processing is revolutionizing the manufacturing industry by automating the production of precision parts. However, with this technology comes the complexity of managing multiple orders simultaneously. Each customer expects consistent updates on their order, from initial processing to completion and delivery. Therefore, CNC manufacturers must create efficient systems that allow for accurate tracking of orders.
Real-time order tracking plays an essential role in:
3.
ERP systems serve as the backbone for many CNC manufacturers. These integrated software systems manage core business processes, including inventory, order management, and production scheduling.
3.
Manufacturing Execution Systems provide detailed insights into the production process, from raw materials to finished products.
3.
The integration of IoT technologies into CNC manufacturing is poised to bring a revolution in order tracking.
3.
Cloud computing has become a game-changer for manufacturies that want to access data anytime, anywhere.
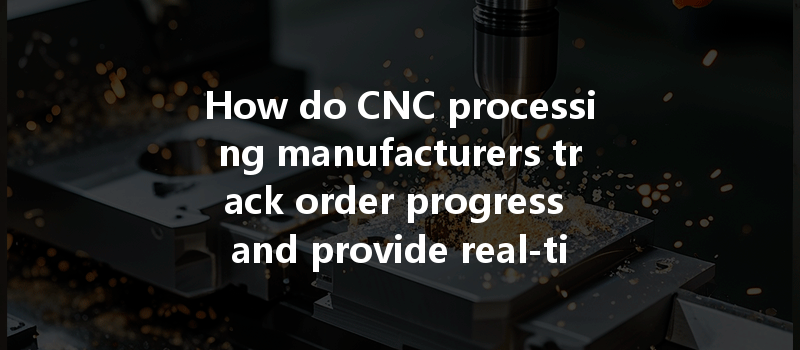
To maximize the efficiency and effectiveness of order tracking, CNC manufacturers often implement a combination of technologies—a hybrid approach.
4.
Implementing an integrated platform where ERP, MES, and IoT data can be shared freely ensures that everyone—manufacturers, staff, and customers—are on the same page.
4.
Training employees on these systems is crucial for ensuring that order tracking processes run smoothly. Regular workshops and updating training programs can keep everyone informed on the latest features and best practices.
While robust systems are vital, manufacturers must also address potential challenges, such as:
To illustrate the impact of effective order tracking, let’s look at a few successful CNC manufacturers that have integrated these technologies:
6.
By implementing an ERP system with real-time customer portals, Company A reported a 50% decrease in customer inquiries about order status. Customers now have access to real-time updates, which has significantly improved satisfaction rates.
6.
After integrating an MES with IoT capabilities, Company B gained visibility over every step of the manufacturing process. This allowed for immediate alerts when an order was behind schedule, enabling proactive communication with customers.
6.
Utilizing cloud technology has allowed Company C’s sales team to access order progress from remote locations, leading to a more agile customer service response. This flexibility has resulted in an increase in repeat business.
: The Future of CNC Order Tracking
The landscape of CNC manufacturing order tracking is evolving rapidly with technological advances. The combination of ERP, MES, IoT, and cloud computing is providing a robust framework for real-time updates, ultimately leading to improved customer satisfaction and operational efficiency. As CNC processing manufacturers continue to innovate, the emphasis on transparency and communication will be critical in securing long-term relationships with customers.
In summary, understanding how CNC processing manufacturers track order progress and update customers in real time is essential for businesses aiming to thrive in this competitive market. As manufacturers adopt these technologies, they will discover significant benefits that not only improve service delivery but also foster lasting trust with their clients. For industry stakeholders, the time to rethink order tracking strategies is now—embracing change is the first step toward a more successful future in CNC machining.