Have you ever considered how the finish of a manufactured piece can significantly impact its performance and aesthetics? In a world where precision is paramount, achieving a specific surface finish has never been more critical, especially in industries like aerospace, automotive, and mold manufacturing. Did you know that a surface finish designated as RA 0.8 can crucially influence the performance quality of machined components? This blog explores the intricacies, challenges, and the specialized techniques used to achieve this finish in aluminum CNC machining for mold manufacturing.
Understanding Surface Finish in CNC Machining
Surface finish refers to the texture and smoothness of a manufactured surface. It is measured using Ra (Roughness Average) values, where a lower Ra value indicates a smoother finish. In the context of aluminum CNC machining, achieving an RA 0.8 finish is often desired but challenging. As the demand for high-performance components increases, manufacturers need to understand the importance of achieving this finish.
The significance of RA 0.8 lies in its correlation to various mechanical properties, such as wear resistance, fatigue strength, and corrosion resistance. Components with this surface finish display reduced friction during operation, improving efficiency and longevity.
Common Challenges in Achieving RA 0.8 Finish
Achieving an RA 0.8 finish in aluminum CNC machining is often fraught with challenges, including:
Understanding these challenges is the first step toward developing effective solutions.
Strategies for Achieving RA 0.8 Finish
The first step in achieving an RA 0.8 finish is selecting the appropriate aluminum alloy. Alloys such as 6061, 7075, and 2024 are popular choices due to their excellent machinability. Each alloy has distinct properties affecting the final surface finish, including hardness, thermal conductivity, and workability.
Selecting the right cutting tool is crucial for achieving a superior surface finish. Tips for optimizing tool selection include:
Machining parameters have direct implications on the resulting surface finish. Key parameters to consider include:
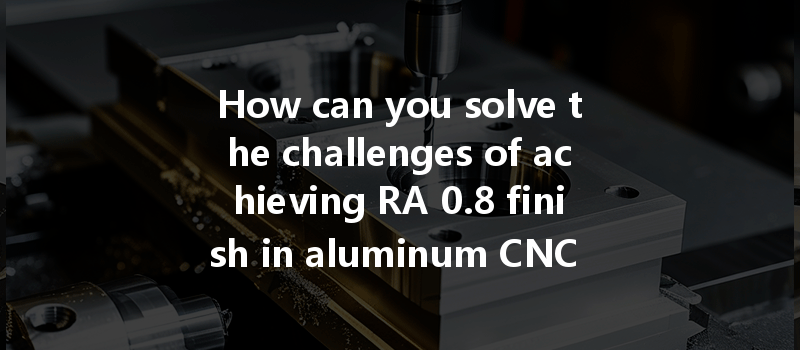
Vibration can severely impact the surface quality of machined components. Strategies for reducing vibration include:
The application of the right coolant can mitigate overheating during machining, which can adversely affect both the material and finish. Considerations include:
Once the machining operation is complete, additional post-processing techniques may be required to achieve the desired RA 0.8 finish:
Incorporating new technology and methodologies in CNC machining can also aid in achieving desired finishes. Adoption of:
Achieving an RA 0.8 finish in aluminum CNC machining for mold manufacturing presents unique challenges; however, it is certainly within reach with the right strategies. By emphasizing material selection, optimizing cutting tools and machining parameters, minimizing vibrations, and leveraging post-processing techniques, manufacturers can realize improved surface finishes that meet modern standards.
Understanding and mastering these techniques not only elevates the quality of manufactured components but also ensures greater performance and longevity. As markets continue to demand such precision, this topic warrant strong attention and implementation in manufacturing practices.
Remember, as we advance into an era of unprecedented technological change, adopting best practices in achieving optimal finishes could well be the key differentiator in the competitive landscape. The importance of meticulous attention to surface finish in CNC machining cannot be overstated; it is a reflection of quality, precision, and excellence in the manufacturing industry.
Investing your time and resources in mastering the art of CNC machining finishes is worth it. Not only will it enhance the quality of your outputs, but it will also position you ahead in a competitive marketplace, ultimately leading to satisfied customers and fruitful business outcomes.
—