When it comes to CNC machining, the versatility of materials is astounding. Did you know that polypropylenes (PP) account for approximately 25% of the global plastic market and are widely used in industries ranging from automotive to medical? With such extensive applications, improving the processing efficiency of CNC machining for PP plastic is not only a technical need but also a significant market opportunity.
In this blog, we will explore critical techniques and best practices to enhance the processing efficiency of CNC machining for PP plastic. We’ll delve into the unique properties of PP, the challenges faced during its machining process, and propose detailed solutions to common constraints.
Understanding Polypropylene (PP)
Characteristics of PP
Polypropylene is renowned for its excellent chemical resistance, low density, and good mechanical properties, making it an ideal choice for CNC machining (Computer Numerical Control). Its resilience against a variety of acids and bases allows it to be widely applied in various industries. However, these advantages come with challenges when it comes to machining.
Common Applications of PP
PP is often utilized in a variety of products including:
Understanding these applications helps in grasping why improving processing efficiency for PP plastic is crucial for manufacturers.
Challenges of CNC Machining PP Plastic
Before diving into solutions, let’s take a closer look at the challenges that affect the efficiency of CNC machining for PP plastic.
Strategies to Improve Machining Efficiency for PP Plastic
Here are detailed strategies and techniques to enhance the processing efficiency of CNC machining specifically for PP plastic:
Cutting Speed and Feed Rate: Understanding the optimal cutting speeds and feed rates for PP is crucial. For instance, a moderate cutting speed often yields the best results due to the structure of PP. Experimenting with various speeds can help find the sweet spot that minimizes heat buildup while maximizing throughput.
Depth of Cut: The depth of cut should be adjusted based on the rigidity of the setup. A shallower depth can reduce potential melting and deformation.
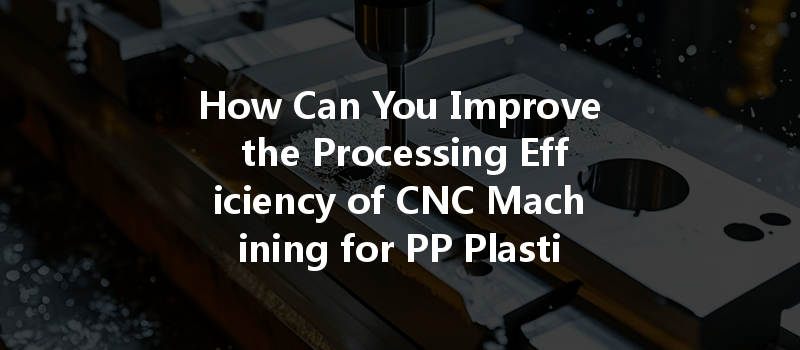
Material of Tooling: Using carbide tools with a sharp edge can significantly improve cutting efficiency. Additionally, tools with a specialized coating can reduce friction and heat generation.
Tool Geometry: The design of the cutting tools should consider the unique characteristics of PP. Consider using tools with a positive rake angle, which can help minimize cutting forces and enhance surface finish.
Coolant Use: Utilize cutting fluids, or air cooling systems when machining PP to help manage heat. Mist cooling can be effective in keeping temperatures down without causing the workpiece to warp.
Machining Environment: Control the ambient temperature to minimize thermal expansion and maintain the integrity of the workpiece throughout the machining process.
High-Speed Machining (HSM): High-speed machining techniques leverage increased spindle speeds to minimize cutting forces and heat buildup, leading to improved precision and efficiency.
Adaptive Machining: Consider an adaptive machining approach where real-time data feedback allows for automated adjustments during the machining process, thus reducing deviations and improving efficiency.
Optimizing Toolpath: Use advanced CAM (Computer-Aided Manufacturing) software to analyze and optimize cutting paths. Efficient tool paths can significantly reduce cutting time and tool wear.
Multi-Axis Machining: Implementing multi-axis CNC machining can reduce the number of setups required and improve accuracy, especially for complex geometries.
Chip Removal Techniques: Incorporating chip breakers or utilizing tools designed to create smaller chips can help mitigate chip entanglement issues, maintaining a smoother machining process.
Vacuum Systems: Implementing efficient vacuum systems to remove chips promptly can prevent interference with the cutting operation.
Routine Checks: Regular inspections of CNC machines ensure they are functioning optimally. Any mechanical issues can lead to inefficiencies in machining accuracy and time.
Calibration: Keep all equipment calibrated regularly to maintain precision and repeatability in machining.
Operator Training: Invest in training programs for operators to ensure they understand the intricacies of working with PP and the importance of adjusting parameters correctly.
Continuous Improvement Culture: Foster a culture of continuous improvement among staff, encouraging innovation and sharing best practices.
Improving the processing efficiency of CNC machining for PP plastic involves a multifaceted approach. By understanding the unique properties of PP, addressing challenges head-on, and implementing strategic solutions that encompass tool selection, cutting parameters, and advanced techniques, manufacturers can significantly enhance their production processes.
As we have explored in this blog, the optimization of CNC machining for PP not only helps in reducing costs but also elevates product quality and operational efficiency. These factors are crucial in staying competitive in today’s fast-paced industrial environment.
By embracing the methods outlined, manufacturers can capitalize on the extensive applications of PP, turning challenges into opportunities for growth. As you reflect on these strategies, consider how they can be integrated into your operations to create lasting improvements and contribute to innovative manufacturing solutions.
Remember, the efficiency of CNC machining in the production of PP plastic may very well set the stage for your company’s success in a competitive landscape. It’s an investment that not only enhances productivity but solidifies your brand as a front-runner in quality and innovation.