: The Importance of Precision in CNC Machining
Did you know that the aerospace industry requires dimensional tolerances as tight as ±0.001 inches for their components? This precision, crucial for performance and safety, can only be guaranteed through meticulous CNC (Computer Numerical Control) machining processes. In industries where every millimeter counts, the ability to ensure the dimensional accuracy and machining quality of large CNC parts is paramount.
Whether you are involved in aerospace, automotive, or any high-stakes manufacturing sector, understanding how to achieve and maintain these accuracies will not only enhance the performance of your products but also significantly reduce waste and production costs. In this blog, we dive deep into the best practices, advanced techniques, and technological integrations necessary to secure unmatched machining quality.
—
1.1 What is CNC Machining?
CNC machining is a process in which pre-programmed computer software dictates the movement of factory tools and machinery. This technology has transformed manufacturing and production quality, leading to enhanced efficiency and consistency. Parts are produced by removing material from a solid block until the desired shape and dimensions are achieved.
1.2 The Significance of Dimensional Accuracy
Dimensional accuracy refers to the precise measurement and replication of the specified dimensions in the final product. In CNC machining, it involves ensuring that every part adheres to the detailed specifications outlined in the design phase. Variations even on a microscopic level can lead to catastrophic failures, especially in applications like aerospace.
—
2.1 Rigorous Design Phase
Incorporating Tolerances
During the design phase, it’s essential to define clear tolerances. Utilize CAD software to incorporate tolerances that reflect the functional requirements of the part. Employ techniques like tolerance stacks to predict how tolerances of individual components will impact the final assembly.
2.2 Selecting the Right Materials
The choice of materials significantly impacts machinability. For instance, metals like aluminum and brass are easier to machine due to their properties compared to harder materials like stainless steel. Select materials that reduce tool wear and allow for tighter tolerances.
2.3 Tool Selection and Maintenance
Cutting Tools
Choosing the appropriate cutting tools is crucial. Carbide tools provide excellent durability and can maintain sharp edges over extended periods, leading to better accuracy. However, their cost may be higher, so consider balancing quality and budget.
Tool Maintenance
Regularly inspect and maintain tools to avoid degradation that could compromise machining quality. Dull or worn-out tools lead to incorrect dimensions and increased production times.
2.4 Advanced CNC Technology
Machine Calibration
Ensure regular and precise calibration of CNC machines. Accurate calibration limits discrepancies and maintains the integrity of the machining processes.
Feedback Loops
Incorporate sensors and feedback loops in the CNC machining process. Sensors that monitor force, position, and temperature in real-time can provide crucial data that helps operators adjust parameters dynamically to maintain accuracy.
—
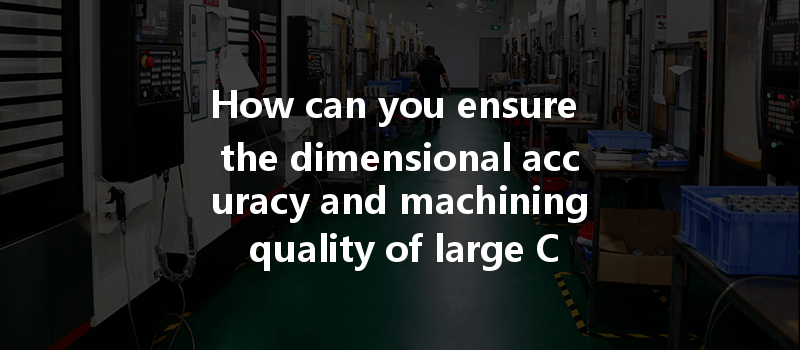
3.1 5-Axis Machining
5-axis CNC machining allows for the creation of complex geometries by providing greater flexibility and options for tool positioning. This ability to approach the workpiece from multiple angles reduces setup times and increases efficiency, leading to higher accuracy, especially in large parts with intricate features.
3.2 High-Speed Machining (HSM)
High-speed machining can dramatically enhance productivity without sacrificing quality. Sharp tools combined with rapid feed rates can result in a smoother finish and increased precision in large components.
3.3 Adaptive Machining Techniques
Implementing adaptive machining techniques supports continuous monitoring and automated adjustments. By developing systems capable of altering machining paths based on real-time feedback, manufacturers can prevent errors associated with tool wear and thermal expansions.
—
4.1 Inspection Techniques
Dimensional Inspection
Using advanced measurement systems like Coordinate Measuring Machines (CMM) ensures that parts are checked against digital specifications post-production. By implementing consistent inspection protocols, deviations from the desired dimensions can be detected and rectified promptly.
Non-Destructive Testing (NDT)
In industries like aerospace and automotive, non-destructive testing is critical. Techniques such as ultrasonic testing or X-ray inspection allow for the identification of internal flaws without damaging the components, providing confidence in the quality and reliability of large parts.
4.2 Process Documentation
Maintaining comprehensive documentation of all processes ensures that machines and operators follow established standards. This practice not only streamlines training for new technicians but also serves as a reference point for troubleshooting and quality assurance.
—
5.1 Workholding Solutions
Utilizing appropriate workholding devices is key to maintaining part stability during machining. Fixtures and vises must be designed to accommodate the geometry of large components, ensuring that they are held securely throughout the machining process.
5.2 Environmental Control
Maintaining a stable environment in the machining area prevents factors like temperature fluctuations from affecting material properties and precision. HVAC systems should regulate air quality and temperature to stay within optimal thresholds.
5.3 Employee Training and Expertise
Continuous professional development for technicians is necessary. Continuous training ensures that operators are up-to-date on the latest technologies, processes, and best practices in CNC machining, fostering a culture of excellence and precision.
—
Ensuring dimensional accuracy and machining quality of large CNC parts is achievable through a blend of meticulous design, advanced technology, stringent quality control, and ongoing technician training. By embracing techniques such as 5-axis machining, high-speed machining, and adaptive methods, manufacturers can significantly enhance the integrity of their production processes.
In sectors where performance is non-negotiable, the investment in these practices pays dividends in quality and reliability. Remember, when you prioritize precision in your manufacturing process, you are not just enhancing the product; you are also ensuring customer satisfaction and cultivating trust in your brand.
Reflecting on this blog, it’s clear that the path to achieving superior dimensional accuracy and machining quality is well paved once the right strategies are implemented. Take these insights to heart and revolutionize your approach to CNC machining today!