Did you know that approximately 70% of manufacturing defects can be traced back to poor quality control measures? In a world where precision and quality are paramount, especially in CNC (Computer Numerical Control) machining, ensuring material certification and quality control is not just a recommendation—it’s a necessity. How do we ensure that our machining processes keep up with these high standards? Let’s delve into the intricacies of material certification and quality control in CNC machining, providing you with detailed solutions and techniques to implement in your operations.
Understanding CNC Machining
Before we dive deeper into material certification and quality control, it is essential to understand CNC machining. CNC machining is a process where pre-programmed computer software commands machine tools and equipment to perform specific tasks. These tasks can include a range of operations, such as drilling, milling, turning, and laser cutting.
CNC machining offers numerous advantages ranging from high precision and repeatability to the ability to work with a variety of materials, including metals, plastics, and composites. However, the effectiveness of CNC machining relies heavily on the quality of the materials used and the processes followed during production.
The Importance of Material Certification
Material certification ensures that the raw materials used in manufacturing meet specific standards. It is a crucial step to verify that materials are safe, reliable, and suitable for their intended application. In CNC machining, the importance of material certification comes down to several critical factors:
Navigating the Maze of Quality Control
Quality control in CNC machining involves a systematic procedure to ensure that the manufacturing process produces components that meet specific requirements. Here are the core components of an effective quality control system in CNC machining:
Implementing standardized protocols helps create consistency in the quality of machine outputs. Establishing quality control standards will involve the following steps:
Before any material is used in the CNC machining process, it’s essential to perform proper inspections and testing. The following methodologies can be applied:
Quality control should not be limited to just raw materials. Implement in-process checks at various stages of the CNC machining process. Key practices include:
After production, components should undergo a final inspection before delivery. Steps to consider:
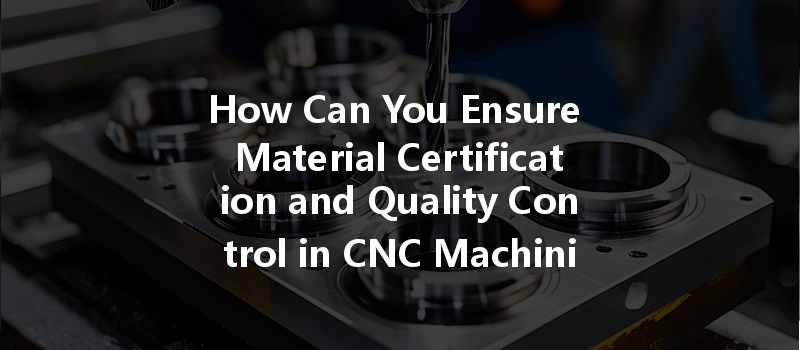
A well-trained workforce is critical to maintaining quality assurance in CNC machining. Continuous training programs should equip employees with the latest knowledge in quality control techniques, tools, and technologies.
Techniques for Implementing Material Certification and Quality Control
Establishing strong relationships with certified suppliers is crucial. It is advisable to:
Implementing a QMS can streamline processes, documentation, and compliance. Consider systems like ISO 9001:2015, which is globally recognized for establishing quality management principles.
New technologies such as Automation, IoT (Internet of Things), and AI (Artificial Intelligence) can drastically improve the quality control process. Key implementations may include:
SPC involves the use of statistical methods to monitor and control manufacturing processes. Techniques include:
Establishing a feedback loop where insights from quality control efforts inform process improvements is crucial. Key actions include:
As we recap the journey into the realms of CNC machining, material certification, and quality control, it becomes evident that these elements are not just mere formalities—they are the backbone of successful manufacturing processes. From pre-production inspections to in-process quality checks and post-production validations, every step plays a pivotal role in ensuring the final product meets the required standards.
By prioritizing material certification and adopting robust quality control practices, manufacturers not only mitigate risks but also foster trust and confidence with their clients. With the continued evolution of technology, the future of CNC machining is set to embrace even more innovative solutions for quality assurance—making it an exciting time for the industry.
This blog serves as a comprehensive guide for all stakeholders in the CNC machining sector. Whether you are a seasoned manufacturer or a newcomer, understanding these essential quality assurance elements is vital for staying competitive in today’s market. Remember, the quality of your products directly impacts your reputation and success in the long run. So, reinforce your processes, stay certified, and continue striving for excellence!