Did you know that even a minuscule error in machining can result in a product that fails to meet specifications, potentially costing firms thousands of dollars? In the world of manufacturing, precision is paramount. With the rise of advanced technologies, ensuring machining accuracy has become more crucial than ever. This is especially true in sectors like aerospace, automotive, and medical devices, where even the smallest deviations from specifications can have catastrophic consequences.
In this blog, we will explore how to guarantee machining accuracy for CNC (Computer Numerical Control) machined parts by adhering to quality inspection standards. As we delve into this topic, we’ll cover various quality inspection standards, techniques, and best practices that can help businesses achieve high accuracy levels in their CNC operations.
Understanding the Importance of Machining Accuracy
Machining accuracy is not merely a goal; it is a necessity. Parts that do not meet precision standards can lead to:
One of the pivotal factors in achieving machining accuracy is implementing stringent quality inspection standards throughout the CNC machining process.
Quality Inspection Standards: An Overview
Quality inspection standards serve as frameworks for ensuring that manufactured parts meet specific criteria of quality and performance. Some of the most notable standards include:
Understanding these standards is only the first step. The real challenge lies in implementing them consistently throughout the CNC machining process.
Best Practices for Ensuring Machining Accuracy
Before machining begins, it’s essential to define clear and precise specifications for the parts to be produced. These specifications should detail dimensions, tolerances, material types, and surface finishes required. Stakeholders must communicate these details effectively to avoid any misunderstandings.
As mentioned, having a quality management system in place is crucial. A QMS ensures that quality is embedded in every aspect of the machining process. Regularly review and update this system to reflect any new quality standards or industry regulations.
Different CNC machines and tools have unique capabilities and limitations. Understanding the requirements of your specific applications will allow you to choose the right machinery and tooling to meet those needs effectively.
Incorporating advanced technology can enhance machining accuracy. Technologies like CAD (Computer-Aided Design), CAM (Computer-Aided Manufacturing), and CNC coordinate measuring machines (CMM) allow for better design visualization, automated machining processes, and precise dimensional measurements, respectively.
Performing in-process inspections allows you to catch any deviation from specifications early on. This can be achieved by integrating measurement tools directly into the production process.
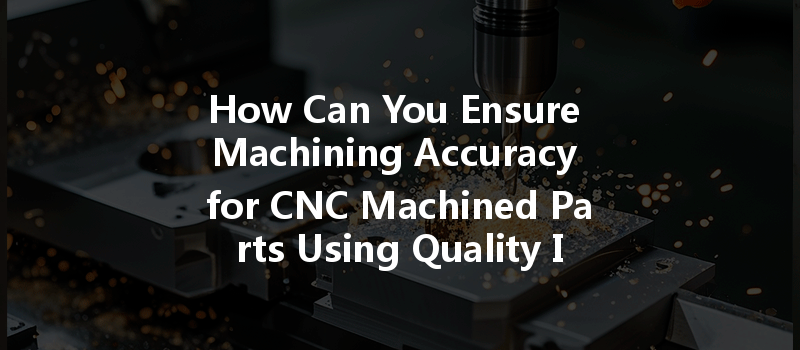
Your measurement tools must be precise to ensure that machining accuracy can be maintained. Regularly calibrate tools like micrometers, calipers, and CMMs against known standards to confirm their accuracy.
Within a robust QMS, employing SPC techniques can further enhance machining accuracy. This involves creating control charts to monitor key process parameters and detect variations or trends that may signal deviations from expected performance levels.
Training staff on quality inspection standards, measurement techniques, and operational processes can significantly influence machining accuracy. Investing in employee development ensures they fully understand their role in maintaining quality.
Automation is not just beneficial for production; it can also be applied to quality inspection. Automated inspection systems can provide quicker and more accurate measurements while reducing human error.
The commitment to accuracy should permeate the company culture, encouraging all employees to prioritize quality in their daily operations. Implement regular meetings, training, and incentive programs to instill an enthusiasm for quality.
Techniques for Improvement
Once the foundational practices are in place, several advanced techniques can be adopted to continually enhance machining accuracy.
Lean Manufacturing
Lean principles focus on reducing waste and improving process efficiency. By refining workflows and eliminating unnecessary steps, companies can enhance precision without compromising productivity.
Root Cause Analysis
Whenever machining errors occur, a detailed root cause analysis can help identify the underlying issues, whether they stem from equipment, processes, or human error. Addressing these root causes can reduce the likelihood of recurrence.
Continuous Improvement Programs
Establishing continuous improvement programs that embrace methodologies like Kaizen can lead to sustained enhancements in machining accuracy. These programs focus on small, incremental changes driven by employee input.
Evaluating Machining Accuracy
Measuring machining accuracy involves various techniques and tools:
The Role of Feedback Loops
Creating a robust feedback loop that allows operators and quality inspectors to communicate about defects or concerns encourages continuous learning and improvement. Capturing data on machining outcomes can help in refining production processes iteratively.
Ensuring machining accuracy for CNC machined parts using quality inspection standards is a multifaceted challenge that combines knowledge, strategy, technology, and culture. By relying on meticulous inspection standards and adopting best practices, businesses can greatly improve machining accuracy, reduce waste, and enhance overall quality.
Remember, precision in machining is the cornerstone of a successful manufacturing process. By investing in quality inspection standards and emphasizing continuous improvement, organizations can bolster their reputations and gain a competitive edge in the market.
This blog serves as a valuable resource for anyone in manufacturing, especially those involved in CNC machining. It emphasizes the importance of quality and precision while providing actionable strategies to mitigate risks and optimize outcomes.
Let’s strive for machining excellence and ensure that our products stand the test of time!