In a world where precision manufacturing and time efficiency are paramount, CNC (Computer Numerical Control) machining stands out as a vital technology that helps industries transform their ideas into tangible products. Whether you are an engineer or a manufacturing leader at YL Machining, understanding how to navigate the intricacies of CNC processing with complex part structures is essential for maintaining a competitive edge.
—
Understanding CNC Machining
What is CNC Machining?
CNC machining is a process that uses computer technology to control machine tools, allowing for the precise manufacture of components and parts. The CNC machine automates the movement and operation of tools, enabling higher levels of productivity compared to manual machining.
The Role of CNC in Modern Manufacturing
YL Machining utilizes CNC technology to cater to various industries, including aerospace, automotive, and medical, where precision and intricacy are non-negotiable. CNC machining has transformed traditional manufacturing into a more dynamic, scalable, and efficient system.
—
The Complexity of Part Structures
Characteristics of Complex Part Structures
Complex part structures often involve multiple features such as intricate geometric shapes, tight tolerances, and varying thicknesses, demanding exceptional precision. Examples include:
Challenges Faced in Machining Complex Parts
—
Enhancing Efficiency in CNC Processing
Advanced CNC Technology and Tools
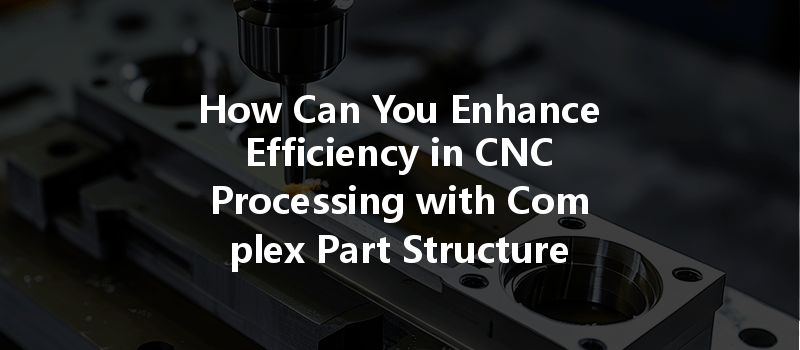
Investing in state-of-the-art CNC machines equipped with advanced features like multi-axis capabilities and adaptive control systems can significantly boost operational efficiency. For instance:
Process Optimization Techniques
Importance of Material Selection
Selecting the right materials for complex part structures is crucial in mitigating manufacturing challenges. Factors to consider include:
—
Best Practices for Working with Complex Geometries
Design Considerations
Design plays a crucial role in the efficiency of CNC machining:
Tool Path Strategies
Machine Calibration and Maintenance
Regular calibration and maintenance of CNC machines maintain operational integrity, ensuring that complex geometries are produced consistently. Implementing a predictive maintenance program can help identify issues before they become critical.
—
Implementing Innovation in CNC Processing
The Role of Software in Workflow Optimization
Software solutions that integrate CAD and CAM functionalities can significantly simplify the workflow, facilitating better design communications and reducing errors. Some important software features include:
The Significance of Automation
Automation plays a critical role in enhancing efficiency, especially in high-volume production settings. Key automation benefits include:
Case Studies: Companies Excelling in CNC Efficiency
To understand practical applications, we look at successful companies effectively implementing these strategies. For instance, a leading aerospace manufacturer adopted a combination of 5-axis machining and advanced programming tools, leading to a 30% reduction in lead time for intricate components.
—
Future Trends in CNC Machining
Integrating Industry 4.0
As we progress into the era of Industry 4.0, the integration of IoT (Internet of Things) and smart technologies will redefine CNC machining. Smart machines equipped with sensors will optimize processes automatically, reducing the need for manual adjustments.
Sustainability in CNC Processing
With increasing pressure on manufacturers to adopt sustainable practices, techniques such as recycling cutting tools, reducing material waste, and energy-efficient machinery are gaining traction.
Global Market Insights and Predictions
The CNC machining market is expected to grow significantly, with advancements in automation and artificial intelligence leading the charge. Companies that adapt to technological innovations will continue to thrive.
—
Navigating the complexities of CNC processing requires not only technical expertise but also an unwavering commitment to innovation and efficiency. At YL Machining, we believe that by embracing advanced tools, software, and best practices, we can set new benchmarks for quality and efficiency in CNC machining. As the industry continues to evolve, our focus remains on adapting and serving our clients with unparalleled precision and excellence.
As you embark on your CNC machining journey, remember that staying ahead requires continuous learning, adaptation, and a collective effort toward embracing efficient practices. The future looks promising, and the choices you make today will pave the way for a successful tomorrow.