Did you know that nearly 60% of companies report vendor-related delays as one of the primary causes of project holdups? In a world where businesses are striving for faster turnaround times and impeccable quality, delivery delays in CNC (Computer Numerical Control) processing can seriously impact project outcomes. Whether you are a fabricator, manufacturer, or designer, understanding how to avoid these delays is crucial for timely and successful project completion.
Understanding CNC Processing
CNC processing is an advanced manufacturing technique that uses computer-controlled machines to produce intricate parts with high precision. From automotive components to aerospace assemblies, CNC machining is ubiquitous across various industries. Despite its efficiency and capabilities, imperfections in supply timelines can lead to significant setbacks in production workflows.
While some delays may be unavoidable, many can be mitigated with a careful strategy. Here’s an in-depth look into practical solutions that can help you limit delivery delays in CNC processing.
Evaluate Credentials and Capabilities
When choosing a CNC service provider, you should investigate their credibility and capacity. Look for:
Establish Clear Communication Channels
From the get-go, ensure that there are channels for transparent communication. Regular check-ins and updates can help you stay informed about the progress and any potential issues that could arise.
Define Scope and Specifications
To avoid misunderstandings, it’s essential to articulate clear specifications for the project:
Create Buffer Times
In planning, incorporate buffer periods to accommodate unforeseen delays. By allocating extra time, project managers can better absorb hiccups without jeopardizing the delivery date.
Source Materials Early
Delays often stem from material shortages or backorders. Address this by:
Utilize Advanced Inventory Management Systems
Implementing advanced inventory systems allows for real-time tracking of stock levels, ensuring you are always prepared. It also facilitates better communication with suppliers and needs forecasting.
Regular Maintenance Checks
Operational inefficiencies or equipment failure can lead to significant slowdowns. Perform regular maintenance to keep machinery running smoothly:
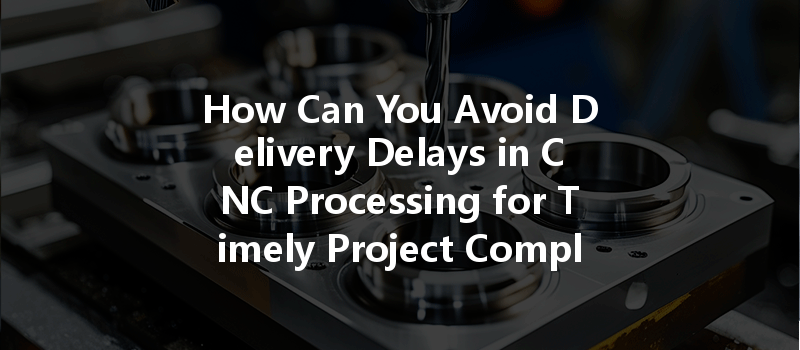
Streamline Operations
Lean manufacturing aims to reduce waste in all forms, including time delays. Consider integrating lean principles into your CNC processes by:
Transparent Communication
Keep your clients informed. When issues arise, a proactive approach to communication can make all the difference:
Educate the Client
Sometimes, clients may have unrealistic expectations due to a lack of understanding of CNC processes. Educate them on lead times, production processes, and potential variables that could affect timelines.
Optimize Job Scheduling
Careful job scheduling can minimize downtime and increase productivity. Techniques include:
Implement Automation
Incorporating automation and robotics can streamline production processes, leading to faster turnaround times:
Regular Training
Training employees ensures they are up-to-date with the latest technologies and methods in CNC processing:
Conduct Post-Project Reviews
Analyzing completed projects helps you identify what went well and what didn’t. In these reviews:
In conclusion, avoiding delivery delays in CNC processing requires a multi-faceted approach that encompasses careful planning, effective communication, efficient operations, and continuous improvement. By selecting the right partner, fostering good relationships, and employing strategic practices, companies can minimize delays and maximize productivity.
This blog serves as a reminder of how paramount timely project completion is to overall business success. With the fast-paced nature of today’s market, delays not only impact financials but also damage client relationships. Reflecting on the methods and strategies provided here can position your business for success, enabling you to manage timelines effectively and deliver satisfactory results consistently. The commitment to optimize processes and minimize delays ensures your operations thrive in this competitive landscape.