Did you know that the surface treatment process can significantly impact the lifespan and performance of CNC machined parts? Studies have shown that a mere 1% variation in the surface finish can lead to a 10-20% decrease in mechanical performance. This fact highlights the crucial importance of maintaining stability and consistency in surface treatment quality. For manufacturers striving to meet customer demands and industry standards, understanding how to achieve these goals is pivotal.
In this comprehensive blog, we will explore the various methods, techniques, and best practices that manufacturers can implement to ensure the stability and consistency of surface treatment quality in CNC machining. By diving deep into the processes and parameters that influence surface finishes, you’ll find actionable insights to improve your machining operations.
Understanding Surface Treatment in CNC Machining
Surface treatment involves various processes such as coating, polishing, anodizing, and shot peening, designed to enhance the physical and chemical properties of machined parts. These treatments are applied to achieve desired characteristics such as corrosion resistance, aesthetic appearance, adhesion, and increased fatigue strength.
The Importance of Consistency in Surface Treatments
Key Methods to Ensure Stable and Consistent Surface Treatments
Achieving stability and consistency in surface treatments isn’t an instantaneous process; rather, it involves a combination of scientific knowledge, engineering principles, and methodical procedures. Below are some effective approaches to attain this goal.
Before initiating any surface treatment, it’s essential to comprehend the properties of the material being processed. Different metals and alloys react differently to surface treatments. For example, aluminum requires anodizing for corrosion resistance while brass often benefits from electroplating. Make sure to:
The parameters set during surface treatment processes significantly affect the outcome. Here are some critical factors to consider:
Using machinery equipped with sensors and automation technology can aid in maintaining these parameters within designated limits.
Advancements in technology play a crucial role in stabilizing surface treatments. Many modern machining facilities now utilize:
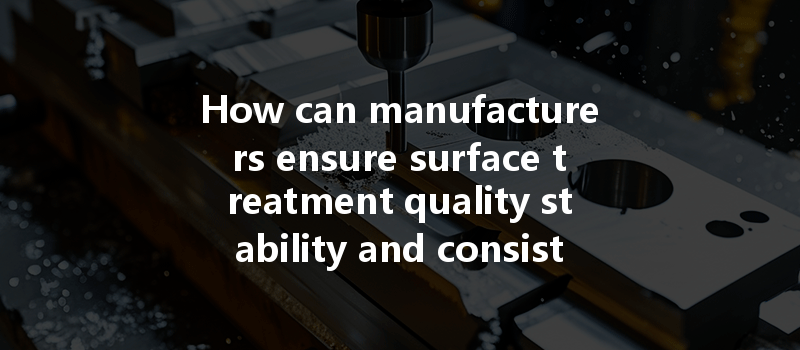
Establishing well-documented Standard Operating Procedures (SOPs) is essential for achieving consistency. An SOP serves as a benchmark for workers and includes details about:
Regular training sessions and audits can ensure that the team adheres strictly to these procedures.
Quality assurance should be integrated into every step of your CNC machining process, especially after surface treatments. Several testing methods can verify surface quality:
Establishing a routine inspection and testing schedule can detect issues early and prevent inconsistencies from reaching the final product.
Create a culture of feedback within your team. Encourage operators to report issues and improvements with the surface treatment process. Implement tools like:
Encouraging a mindset of continuous improvement will empower your team to take ownership of consistency in surface treatment.
: The Path to Consistent Quality
In summary, ensuring the stability and consistency of surface treatment quality in CNC machining is a multifaceted endeavor. It requires a comprehensive understanding of materials, careful management of process parameters, leveraging advanced technologies, adherence to SOPs, diligent quality testing, and fostering a culture of continuous improvement.
The importance of this discussion cannot be understated: high-quality, consistent surface treatments not only enhance the performance and lifespan of components but also strengthen customer satisfaction and adherence to industry standards. As manufacturing processes continue to evolve, those who commit to rigorously applying these practices will not only gain a competitive edge but also lead the way in pioneering innovations within the industry.
As you delve into your manufacturing processes, consider taking these insights to heart. Reflect on your current procedures, identify areas for improvement, and make the necessary investments in technology and training. The road may be complex, but the rewards of achieving consistency and stability in surface treatments are undoubtedly worth the effort.