: The Precision Revolution in Manufacturing
Did you know that CNC (Computer Numerical Control) machining has revolutionized manufacturing to the point where it can achieve tolerances as tight as ±0.001 inches? This level of precision is a game-changer, particularly in industries like aerospace, automotive, and medical device manufacturing, where even the slightest deviation can lead to catastrophic failures or costly recalls. With the growing demand for high-precision components, manufacturers are increasingly turning to CNC processing as a reliable solution.
So, how exactly can CNC processing meet the high-precision requirements for custom parts? This blog will delve into advanced strategies, techniques, and technologies that empower manufacturers to achieve top-notch precision in custom CNC machining.
—
Chapter 1: Understanding CNC Machining
1.1 What is CNC Machining?
CNC machining is a subtractive manufacturing process that uses computer-controlled equipment to remove material from a workpiece to achieve desired shapes, sizes, and finishes. Machines such as lathes, mills, and routers operate based on pre-programmed computer commands to produce intricate parts with precision and repeatability.
The process is favored for its ability to produce complex geometries that are difficult or impossible to fabricate using traditional methods. As industries evolve, CNC machining technology has expanded to include various materials, including metals, plastics, and composites.
1.2 The Importance of Precision
Precision in CNC machining is paramount. Components that are out of specification can lead to poor product performance and increased costs. A minute error in dimensions during manufacturing can compromise assembly, efficiency, and safety.
Achieving high precision is especially critical in sectors like aerospace, where parts are subjected to rigorous standards and must operate flawlessly under extreme conditions. With the integration of CNC machines into production processes, organizations can push the boundaries of what is possible in manufacturing.
—
Chapter 2: The Precision-Centric Features of CNC Machining
2.1 Advanced CNC Machines
Modern CNC machines come equipped with advanced features that facilitate high precision in custom parts manufacturing. These features include:
2.2 Rigidity and Stability
The physical attributes of CNC machines significantly impact their precision. Machines designed with rigidity and stability minimize vibrations during the cutting process, leading to superior dimensional accuracy. Manufacturers should consider investing in high-quality machines built with robust materials.
—
Chapter 3: Materials and Their Impact on Precision
3.1 Material Selection
Different materials have varying machinability characteristics, affecting precision during CNC processing. Metals like aluminum and titanium possess distinct properties that can influence how accurately they can be machined.
Choosing the appropriate material for the specific application is critical and should consider factors like thermal expansion, strength, and hardness.
3.2 Material Treatment
Pre-treating materials (e.g., heat treatment) can improve their machinability. Additionally, employing techniques like annealing may lead to greater consistency, reducing error rates during manufacturing.
—
Chapter 4: Precision Strategies in CNC Machining
4.1 Tolerance Standards
Understanding and adhering to tolerance standards is fundamental in CNC machining to meet high-precision requirements. Utilizing ISO (International Organization for Standardization) guidelines helps ensure that parts meet both national and international quality standards.
4.2 Software and Simulation
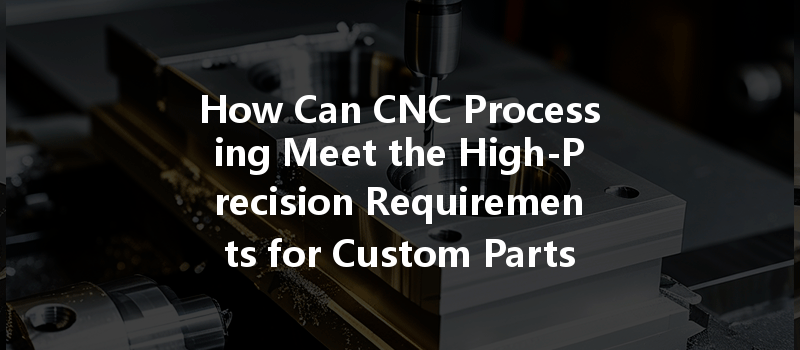
Advanced software solutions allow for modeling and simulating the manufacturing process before physical production occurs. This capability helps identify potential issues and optimize tool paths, significantly enhancing precision.
By implementing these software tools, manufacturers can visualize the entire machining process and make adjustments before production begins.
—
Chapter 5: The Role of Quality Control
5.1 Continuous Monitoring
High-precision CNC processing requires continuous monitoring to identify and correct any deviations in real-time. Techniques such as:
These methodologies help improve the consistency and accuracy of custom parts.
5.2 Post-Processing Inspection
Once parts are manufactured, thorough inspection processes ensure that the final products meet the desired specifications. Common techniques include:
—
Chapter 6: Training and Skill Development
6.1 Skilled Workforce
The precision of CNC processing is greatly dependent on the skills and experience of the operators. A well-trained workforce is crucial for achieving high-precision outcomes.
6.2 Continuous Education
Encouraging continuous education for technicians and operators through courses and practical training can dramatically improve precision in CNC processing. This not only includes technical skills but also an understanding of materials, tools, and machine operating systems.
—
Chapter 7: Future Trends in CNC Machining Precision
7.1 Automation and AI
The incorporation of automation and artificial intelligence (AI) into CNC machining is paving the way for unprecedented precision. Smart machines equipped with AI algorithms can learn from past operations, optimizing real-time processes and factors that contribute to precision.
7.2 Additive Manufacturing Integration
The convergence of CNC machining with additive manufacturing (3D printing) technology offers an avenue for achieving even higher precision and complexity in parts production. This hybrid approach allows for creating parts that require intricate features.
—
: The Path Forward in Precision CNC Processing
In summary, achieving high precision in custom CNC parts manufacturing is a multifaceted challenge that encompasses machine capabilities, material selection, software applications, quality control, skilled labor, and future technological advancements.
By focusing on these core techniques—ranging from advanced machinery and tolerance standards to continuous monitoring and workforce training—manufacturers can meet the ever-increasing demand for precision.
This blog is significant not just for manufacturers looking to improve their processes but also for anyone interested in understanding the complexities of modern manufacturing. As industries advance, understanding how precision CNC processing works can be essential for ensuring product quality, performance, and safety in numerous applications.
In a world where precision is increasingly becoming synonymous with success, reflecting upon these CNC machining approaches will not only enhance production capabilities but also pave the way for innovation.