Did you know that a staggering 70% of manufacturing companies report issues with product quality? In an industry driven by precision and efficiency, maintaining consistent product quality is critical for success and customer satisfaction. This is especially true in the Computer Numerical Control (CNC) machining sector, where even the smallest deviation from specifications can lead to significant functional failures or production halts.
The question then arises: How can CNC processing manufacturers ensure regular product quality inspections that not only maintain standards but also enhance operational efficiencies? In this comprehensive guide, we will explore strategies and solutions that CNC manufacturers can implement to ensure meticulous quality inspections. We will cover best practices, advanced technologies, and continuous improvement methodologies that can be integrated into the quality management system.
Understanding the Importance of Quality Inspections in CNC Machining
Quality inspections are not just a procedural step; they are a commitment to excellence that has far-reaching ramifications:
In light of these benefits, CNC manufacturers must devise a robust framework for regular quality inspections.
Key Strategies for Ensuring Regular Product Quality Inspections
A comprehensive Quality Management System is the backbone of product quality in CNC machining. By adhering to standards such as ISO 9001, manufacturers can demonstrate their commitment to quality.
Steps to Implement a QMS:
Utilizing advanced inspection technologies can drastically enhance the quality inspection process.
a. Automated Inspection Systems
Incorporating automated systems such as Automated Optical Inspection (AOI) can help in real-time detection of defects. By integrating cameras and software algorithms, you can quickly identify issues such as misalignment, surface defects, or dimensional inaccuracies.
b. Coordinate Measuring Machines (CMM)
CMMs are vital in measuring the physical geometrical characteristics of an object. Using CMMs, manufacturers can gain precise dimensional measurements, ensuring that the CNC machined parts meet exact specifications.
c. Laser Scanning and 3D Imaging
Laser scanning technology can create a detailed digital reproduction of a part, allowing manufacturers to compare it against its CAD model. This technology not only enhances precision but also minimizes human error in measurements.
Statistical Process Control (SPC) involves using statistical methods to monitor and control a process. This strategy can detect variations in production that may affect quality.
Steps to Implement SPC:
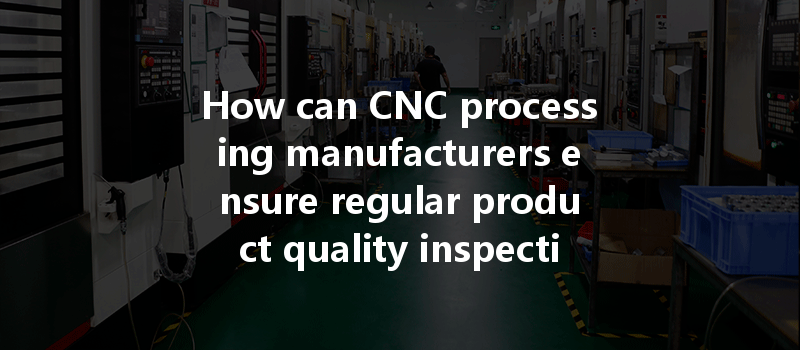
Creating a culture of quality within the organization is crucial for enhancing product inspections. When quality becomes part of the organizational ethos, employees are more likely to take ownership of their roles in maintaining it.
Strategies to Build a Quality Culture:
Adopting continuous improvement methodologies like Lean and Six Sigma can help CNC manufacturers enhance their quality inspection processes.
Lean Manufacturing
The focus of Lean manufacturing is to eliminate waste and enhance value. By conducting regular evaluations and streamlining processes, manufacturers can minimize defects and optimize quality inspections.
Six Sigma
Six Sigma methodologies use data-driven approaches to improve process quality. This method aims for near perfection in production by reducing the number of defects to an acceptable threshold.
Collaboration with suppliers is essential in maintaining product quality. Establishing clear communication regarding quality expectations can improve incoming material quality, which often directly influences the finished product.
Steps for Supplier Quality Management:
Providing continuous training and professional development for employees involved in quality inspections is paramount. Knowledgeable employees are more competent in identifying potential quality issues and maintaining high standards.
Training Area Focus:
Establishing feedback channels is crucial for gauging customer satisfaction and gathering insights to improve quality processes. Use surveys, interviews, and direct feedback from customers to continually refine your inspection processes.
Leveraging data analytics can provide valuable insights into product quality trends. By utilizing predictive analytics, manufacturers can anticipate potential quality issues before they disrupt production.
Implementing quality management software can centralize and automate quality inspection processes. This software often includes features like document control, workflow management, and real-time dashboard metrics, making it easier to track and manage product quality.
To wrap it up, ensuring regular product quality inspections in CNC processing is not merely about checking specifications but entails cultivating a holistic approach to quality management. By leveraging advanced technologies, building a culture of quality, engaging in continuous improvement practices, and maintaining open lines of communication with suppliers, manufacturers can achieve consistent output and customer satisfaction.
This blog serves as an essential guide, emphasizing that maintaining product quality is an ongoing commitment that requires diligence, innovation, and collaboration. As the CNC industry continues to evolve, companies that prioritize and invest in quality inspection processes will distinguish themselves and thrive in a competitive landscape. Quality is not just a goal; it is an enduring journey that shapes the foundation of successful CNC manufacturing. Remember, what you produce today shapes your reputation tomorrow!