Did you know that CNC machining can improve the dimensional accuracy and structural integrity of parts significantly, but improper handling can lead to costly deformations? In the manufacturing world, especially when dealing with aluminum alloys, understanding the dynamics of CNC machining is crucial. As industries lean toward lighter and more resilient materials, aluminum alloys have become popular due to their favorable strength-to-weight ratio. However, one of the most challenging issues encountered during CNC machining is the deformation of aluminum alloy shells.
Aluminum alloys represent over 75% of non-ferrous metal used in manufacturing because of their excellent mechanical properties and corrosion resistance. As demand increases for precise components in industries like aerospace, automotive, and consumer electronics, manufacturers must ensure that the machining processes do not compromise the very attributes that make aluminum alloys desirable. This comprehensive blog will dive into the causes of deformation and the effective techniques to minimize or prevent deformation of aluminum alloy shells during CNC machining.
Understanding Deformation in CNC Machining
Deformation refers to the change in shape or dimensions of a workpiece under the influence of external forces, heat, or material properties. In the context of aluminum alloy shells during CNC machining, several factors contribute to deformation:
Techniques to Prevent Deformation of Aluminum Alloy Shells
Tool Selection
Choosing the appropriate cutting tool is imperative in reducing deformation. Use high-speed steel (HSS) or carbide tools that can withstand the mechanical and thermal stresses during the machining process.
Feed Rate and Speed
Selecting the right feed rate and cutting speed is essential. A feed rate that is too high can generate excess heat, while a feed rate that is too low may lead to pushing the tool against the workpiece too hard, causing deformation.
Coolants and Lubricants
Utilizing coolants can help reduce the heat generated during machining. Additionally, lubricants can minimize friction, leading to smoother cuts and less heat buildup.
Effective fixturing plays a crucial role in minimizing deformation. Consider these approaches:
Rigid Fixturing
Creating a rigid fixture that securely holds the workpiece minimizes unwanted vibrations and movement, allowing for consistent machining pressure without applying uneven forces.
Strategic Placement of Support Features
For complex parts, strategically placed support features, like clamps or blocks, can help maintain the geometry of the aluminum shell, reducing the likelihood of flexing during the machining process.
Use of Flexible Fixtures
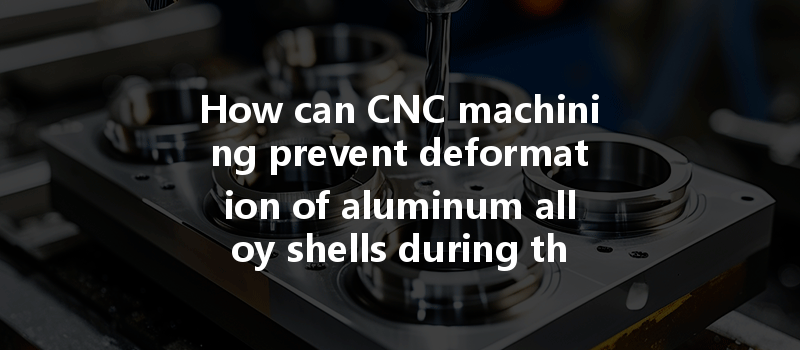
In some cases, adaptive or flexible fixturing systems can manage varied geometries and ensure even pressure distribution across the workpiece.
Before machining, consider pre-treating the aluminum alloy shells. Techniques such as stress relieving—using thermal processes or shot peening—can help mitigate residual stresses within the materials, reducing the chance of deformation during machining operations.
The design stage plays a critical role in the prevention of deformation. Thoughtful design can significantly reduce the propensity to warp during machining.
Utilize CAD and Simulation Software
Designing with computer-aided design (CAD) tools enables engineers to visualize the part and its features. Using finite element analysis (FEA) software, designers can simulate how the part will behave during machining and identify potential issues related to deformation.
Consider Material Selection
Choosing the right alloy for the specific application can impact deformation. Alloys with higher machinability ratings tend to be less prone to deformation under cutting stresses.
Once machining is complete, consider using post-processing treatments:
Heat Treatment
Utilizing heat treatment methods can align the internal structure of the aluminum, relieving residual stresses and stabilizing the material.
Anodizing and Surface Treatments
Applying anodization can not only improve corrosion resistance but also serve to increase the material’s rigidity and overall strength.
Case Studies
Case Study 1: Aerospace Component Fabrication
A leading aerospace manufacturer faced challenges with deformed aluminum alloy housings. By conducting a thorough analysis, they optimized their machining parameters, applied strategic fixturing, and utilized stress-relieving processes before machining. As a result, they saw a 30% improvement in dimensional accuracy and a reduction in rejected parts.
Case Study 2: Automotive Industry
An automotive parts supplier dealing with thin-walled aluminum components identified severe deformation during machining. They re-evaluated their tooling selection and implemented coolants more effectively. The changes led to a significant reduction in thermal deformation, enhancing the precision of the final products.
In the world of CNC machining, preventing the deformation of aluminum alloy shells requires a combination of well-thought-out strategies and techniques. From optimizing the machining process and selecting the right tools to implementing effective fixturing and post-machining treatments, every step plays a vital role in achieving the desired results.
In an industry where precision and efficiency are non-negotiable, understanding these techniques will not only help manufacturers prevent costly errors but also enhance their competitivity in the ever-evolving market landscape.
By applying the insights shared in this blog, manufacturers can ensure that the deformation of aluminum alloy shells becomes a manageable challenge rather than an insurmountable issue, ultimately leading to higher quality products and greater customer satisfaction.