Did you know that about 70% of manufacturing defects can be traced back to inadequate surface treatment? This startling statistic highlights just how critical the surface finish of machined parts is to the overall quality of a product. Within the realm of CNC (computer numerical control) machining, the surface treatment process plays an imperative role in ensuring the durability, functionality, and aesthetic appeal of components. Understanding how to prevent defects in this process can significantly affect manufacturing efficiency and competitiveness.
: The Importance of Surface Treatment in CNC Machining
CNC machining has transformed modern manufacturing, enabling companies to produce high-quality, precise components with greater speed and efficiency than ever before. However, the benefits of CNC machining can easily be undermined by surface treatment defects. These defects can lead to costly rework, scrapped parts, and ultimately, dissatisfied customers.
In this comprehensive blog, we’ll explore the common defects encountered in surface treatment, the causes behind them, and effective solutions for preventing these issues. By the end of this article, you will gain a deeper understanding of the importance of surface treatment and how to foster high-quality outcomes through the CNC machining process.
Before delving into defects, it’s essential to define what surface treatment encompasses and why it’s a vital part of CNC machining.
1.1 Definition of Surface Treatment
Surface treatment refers to various processes applied to the outer layer of a material to change its properties without affecting the bulk of the material. Possible goals include enhancing corrosion resistance, improving wear resistance, increasing aesthetic appeal, or modifying adhesion properties. Common surface treatments include:
Each of these processes has specific applications depending on the material and the desired outcome.
1.2 Importance of Surface Treatment
Surface treatment plays a crucial role in:
Understanding the potential defects that can arise during surface treatment is essential for preventing them. Here are some of the most common defects and their root causes:
2.1 Pitting and Corrosion
Definition: Pitting is localized corrosion that leads to the formation of small holes or craters on the surface of a metal.
Causes:
2.2 Poor Adhesion
Definition: Poor adhesion occurs when the surface treatment does not bond properly to the base material, leading to peeling or flaking.
Causes:
2.3 Uneven Coating Thickness
Definition: Uneven coating thickness can cause areas to be underprotected or overprotected, leading to compromised mechanical properties.
Causes:
2.4 Discoloration and Surface Imperfections
Definition: Discoloration refers to staining or uneven color on treated surfaces, while surface imperfections include scratches, dents, or bumps.
Causes:
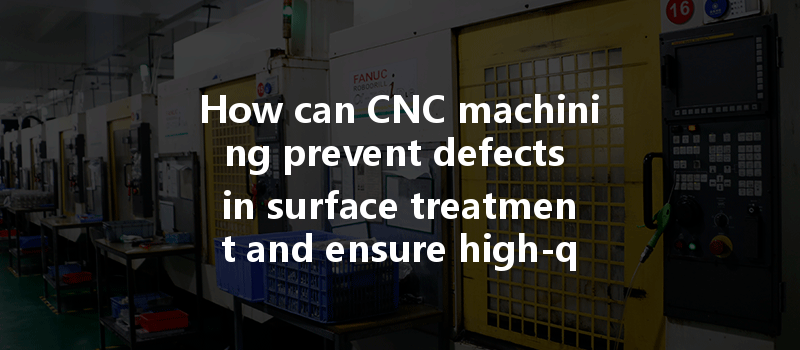
Now that we understand the common defects and their causes, let’s delve into practical strategies for preventing these issues through effective surface treatment practices.
3.1 Ensuring Proper Material Preparation
The first step in preventing surface defects is ensuring that the base material is adequately prepared:
Regularly verify cleanliness through touch and visual inspections. Use water break tests to determine if a surface is clean enough for subsequent treatments.
3.2 Quality Control of Surface Treatment Processes
Establishing a robust quality control process is crucial to monitor and maintain the effectiveness of surface treatments:
Timing and temperature control during curing processes must be monitored closely, as these can greatly affect the result.
3.3 Training and Standardization of Processes
Proper training for technicians and operators involved in surface treatment can significantly reduce errors:
Consistently ensure workers understand the intricacies of their role in preventing surface defects to reinforce accountability.
3.4 Choosing the Right Surface Treatment Method
Selecting the right technique based on the material and production needs is key:
For example, in marine applications, powder coating might offer better corrosion protection than traditional paints.
To exemplify the significance of effective surface treatment defect prevention, let’s review three real-world case studies where companies applied techniques to reduce surface treatment defects effectively.
4.1 Case Study 1: Aerospace Component Manufacturer
A leading aerospace manufacturer faced issues with pitting corrosion on aluminum structural components. By re-evaluating their anodizing process and enhancing material cleanliness, they reduced corrosion incidents by over 80%.
4.2 Case Study 2: Automotive Parts Supplier
An automotive parts supplier experienced problems with poor adhesion of coating on brake components. By refining their cleaning and surface roughening methods, they improved adhesion rates, resulting in a 50% reduction in defects.
4.3 Case Study 3: Marine Equipment Fabricator
A marine equipment fabricator struggled with variations in coating thickness on their equipment due to manual application methods. By automating their coating process and implementing rigorous quality checks, they improved coating uniformity and decreased defects by 60%.
With advancements in technology, there are new methods available to enhance surface treatment quality. Here are some innovations worth considering:
5.1 Automation and Robotics
Integrating robotics into surface treatment processes can significantly improve accuracy and consistency, minimizing human error. Automated spraying, dipping, and coating systems can be programmed to apply treatments uniformly.
5.2 Advanced Monitoring Systems
Real-time monitoring and data analytics can assist in assessing surface conditions before, during, and after treatment processes. Techniques such as optical inspection can catch surface imperfections early, preventing defects from reaching production.
5.3 Innovative Treatment Methods
Stay updated on emerging surface treatment techniques such as laser coating or nanotechnology-enhanced films that can offer superior properties compared to conventional methods.
: Ensuring Quality through Effective Surface Treatment
In conclusion, effectively preventing defects in surface treatment processes is pivotal to achieving high-quality outcomes in CNC machining. By understanding common defects, their causes, and implementing a series of proactive solutions—including proper preparation, quality control, employee training, and technology utilization—you can significantly enhance the overall quality of machined components.
As we’ve seen, recent advancements and best practices in surface treatment are crucial for maintaining competitiveness in the manufacturing industry. By focusing on these techniques, businesses can reduce production costs, increase customer satisfaction, and improve overall product performance.
Engaging with your surface treatment processes thoughtfully is not just an operational necessity; it’s an investment in your company’s reputation and success. Adopting the right strategies to prevent defects not only optimizes your production but strengthens your brand’s credibility in a fast-paced, quality-driven marketplace. Therefore, it’s worth taking the time to reflect on the essential practices covered in this blog to enhance your surface treatment processes in CNC machining.