Did you know that the automotive industry is one of the largest consumers of CNC (Computer Numerical Control) machining services, accounting for approximately 20% of the global CNC machining market? With the ever-increasing demand for precision and efficiency in vehicle production, understanding how CNC machining meets these requirements is crucial for manufacturers and consumers alike. This blog delves into the intricacies of CNC machining in the automotive sector, exploring its methodologies, techniques, and critical role in maintaining high precision and quality standards.
CNC machining has revolutionized various industries by offering unparalleled precision and efficiency. In the automotive industry, where even the slightest variation could jeopardize performance, safety, or emissions standards, the need for accurate and reliable manufacturing processes is paramount. This article will explore how CNC machining meets precision and quality requirements, the technologies involved, and best practices for automotive manufacturers looking to optimize their production processes.
Section 1: The Importance of Precision and Quality in Automotive Manufacturing
1.1 The Role of Precision in Automotive Parts
Precision in automotive manufacturing goes beyond mere measurements. It involves creating complex parts that fit seamlessly into vehicles, ensuring optimal performance and safety. Parts like engine components, transmission systems, and braking systems require precise tolerances and specifications. A deviation of even a few micrometers can lead to catastrophic failures or malfunctioning systems.
1.2 Meeting Quality Standards
Automotive manufacturers must comply with strict quality standards set by international regulatory bodies. ISO/TS 16949, for example, outlines the quality management system requirements for the automotive industry. Compliance ensures that products are both safe and reliable, building trust with consumers.
1.3 The Cost of Poor Precision and Quality
There are significant financial implications associated with failures in precision and quality. Rework, recalls, and warranty claims can cost automotive manufacturers millions. Therefore, investing in reliable manufacturing techniques stands as a financial necessity, not just a regulatory one.
Section 2: The Basics of CNC Machining
2.1 What is CNC Machining?
CNC machining is a manufacturing process that utilizes computerized controls to operate machine tools like lathes, mills, routers, and grinders. It converts a CAD (Computer-Aided Design) file into a machine code, which is then executed by the machine to produce precise parts.
2.2 Benefits of CNC Machining
Section 3: CNC Machining Technologies in Automotive Manufacturing
3.1 Advanced CNC Machines
The latest CNC machines utilize advanced technologies like 5-axis machining and multi-spindle setups. These innovations enable manufacturers to create more complex parts while maintaining high precision.
3.2 Automation and Robotics
Automation plays a vital role in CNC machining, reducing human intervention and enhancing efficiency. Robotic arms can handle loading, unloading, and inspection tasks, which minimizes the risk of errors and improves the flow of operations.
3.3 Software Integration
Modern CNC machines often come integrated with software that facilitates programming, simulation, and process optimization. These tools enable manufacturers to visualize potential errors, optimize machining parameters, and predict maintenance requirements.
Section 4: Ensuring Precision and Quality in CNC Machining
4.1 Design Phase Considerations
The journey to precision starts with a well-designed CAD model. Engineers must consider the capabilities and limitations of the CNC machines when creating designs. Implementing design guidelines specific to CNC manufacturing can minimize issues during machining.
4.2 Best Practices for CNC Machining
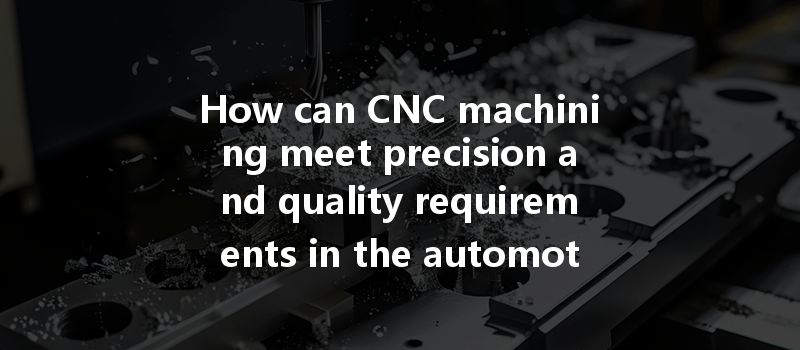
4.3 Quality Control Processes
A robust quality control process is essential to maintain precision and quality standards. This includes implementing techniques like Statistical Process Control (SPC) to monitor and control manufacturing processes.
Section 5: Challenges and Solutions in CNC Machining for the Automotive Industry
5.1 Challenges in Material Selection
Different materials have unique properties that can affect machining precision. For instance, harder metals like titanium can wear tooling quickly, while softer metals may not hold tolerances as well.
Solution: Material-Compatible Tooling
Using specially formulated cutting tools designed for specific materials can extend tool life and maintain precision. Additionally, integrating advanced coatings reduces friction and wear.
5.2 Overcoming Machining Errors
Machining errors can occur due to several factors, including tool wear, machine calibration, and operator intervention. These errors can significantly affect the quality of automotive parts produced.
Solution: Predictive Maintenance
Implementing predictive maintenance systems that use data analytics to forecast machine failures can help manufacturers schedule maintenance during downtime, reducing the risk of operational disruptions.
5.3 Environmental Factors
Temperature fluctuations, humidity, and vibrations can adversely affect CNC machining performance. These variables can lead to dimensional changes and affect overall quality.
Solution: Controlled Environments
Manufacturers can set up temperature and humidity-controlled environments to stabilize conditions for CNC machining processes, ensuring consistent quality.
Section 6: The Future of CNC Machining in the Automotive Industry
6.1 Adopting Industry 4.0
The shift toward Industry 4.0 brings advanced technologies like IoT (Internet of Things), AI (Artificial Intelligence), and machine learning into CNC machining. These technologies enable real-time monitoring and analytics, improving precision and predicting maintenance needs.
6.2 Sustainable Manufacturing
As environmental concerns grow, the automotive industry is tasked with adopting sustainable practices. CNC machining can contribute through:
6.3 Customization and Additive Manufacturing
The trend toward personalization in vehicles is also influencing CNC machining. Combining CNC machining with additive manufacturing allows for unique designs and rapid prototyping, giving manufacturers a competitive edge.
CNC machining plays a pivotal role in meeting the precision and quality requirements of the automotive industry. By combining advanced technologies, best practices, and a rigorous quality control process, manufacturers can produce high-quality, reliable automotive components that meet the demands of today’s market.
As we explored, ensuring precision is not merely a technicality but a crucial factor that influences safety, performance, and consumer trust. Technologies continue to evolve, and the industry must remain agile and responsive to harness the full potential of CNC machining.
For automotive manufacturers, understanding and implementing effective CNC machining practices is not simply beneficial; it’s essential for survival in an increasingly competitive landscape. This blog’s insights into CNC machining’s role in maintaining precision and quality serve as a reminder of the ongoing need for innovation, adaptation, and commitment to excellence in the automotive industry.
By fostering an environment of constant learning and improvement, manufacturers can enhance their production processes and meet the evolving challenges of automotive design and functionality. It’s a journey that starts today—let’s embrace the future of precision engineering together!