Did you know that according to a survey by the Manufacturing Institute, 62% of manufacturers believe that automation technologies will be critical for increasing productivity in their operations? As manufacturing industries continue to evolve, technology plays a pivotal role in meeting challenges associated with production efficiency, especially for small batches and multi-variety production.
CNC (Computer Numerical Control) machining is one such technology that is revolutionizing the way parts are produced, enabling manufacturers to maintain high-quality standards and adaptability. This blog will delve into the intricacies of how CNC machining can enhance the efficiency of small batch and multi-variety production processes, addressing pain points and providing tangible solutions.
Understanding CNC Machining
Before we explore how CNC machining improves efficiency, let’s clarify what it is. CNC machining refers to a computer-controlled manufacturing process that allows for the precise automation of machine tools, such as lathes, mills, routers, and grinders. CNC machines utilize programmed commands to control the movement and operation of the tools, resulting in a more accurate and efficient manufacturing process.
Key Benefits of CNC Machining
Now that we understand the foundational concepts of CNC machining, let’s explore how it specifically enhances the efficiency of small batch and multi-variety production.
The Challenges of Small Batch and Multi-Variety Production
Small batch and multi-variety production refer to manufacturing processes where products are produced in limited quantities and often vary in design and specification. While this approach allows for customization and responsiveness to market demands, it also presents several challenges:
How CNC Machining Addresses These Challenges
Here are ways CNC machining can significantly enhance efficiency under these conditions:
CNC machining offers faster setup times compared to traditional manufacturing methods. Modern CNC machines allow manufacturers to:
Solution: Investing in advanced CNC machines equipped with quick-change tooling and smart programming capabilities can minimize setup times and alleviate the pressure during transitions between different product designs.
One of the significant advantages of CNC is its precision. The advanced capabilities of CNC machines allow for optimal material utilization, leading to fewer errors and less scrap. Here’s how:
Solution: Adopting specialized software for nesting and machining could effectively reduce excess material usage, benefiting the overall production efficiency and costs.
CNC machines can handle multiple jobs in a single setup, enabling manufacturers to produce different components without the hassle of retooling. This capability allows for:
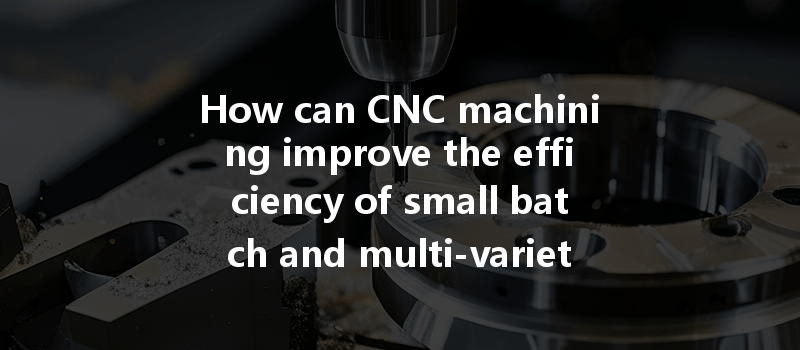
Solution: Implementing a robust production management system that integrates CNC machining tasks can streamline scheduling and enhance workflow efficiency.
Maintaining high quality across varying products can be challenging. Fortunately, CNC machining is equipped with features that ensure consistent product quality:
Solution: Leveraging real-time data analytics and quality monitoring systems can help identify defects early in the production process, ensuring superior quality across all product variations.
Adopting CNC Machining for Small Batch and Multi-Variety Production
Now that we’ve outlined how CNC machining tackles the challenges, let’s look at practical steps for implementation.
Step 1: Evaluate Production Needs
The first step is to conduct a comprehensive assessment of your production needs. Analyzing the types and volumes of parts produced will provide insight into:
Step 2: Invest in the Right Equipment
Based on your evaluation, invest in CNC machines that align with your production requirements. Considerations might include:
Step 3: Implement Advanced Software
Upgrading to modern CAD/CAM software can enhance machining operations. Key features to look for include:
Step 4: Train Your Workforce
Ensuring your team is proficient in using CNC technology is essential for maximizing efficiency. Consider:
Step 5: Monitor and Optimize
Lastly, establish a system to regularly monitor performance metrics. Key performance indicators (KPIs) to track include:
In today’s competitive manufacturing landscape, efficiency is the cornerstone of success, especially in small batch and multi-variety production. CNC machining presents a remarkable solution, helping manufacturers reduce setup times, minimize waste, enhance quality control, and streamline operations.
By systematically evaluating production needs, investing in the right technology, and ensuring a well-trained workforce, CNC machining can transform manufacturing processes. As industries continue to evolve, embracing such innovative technologies is not just an option but a necessity to achieve sustainable growth and competitiveness in the market.
This blog serves as a reminder of the importance of intelligent manufacturing solutions like CNC machining in navigating the complexities of modern production. With the right approach, companies can effectively embrace the exciting possibilities that CNC technology offers and build a more resilient manufacturing framework for the future.