Did you know that nearly 50% of all machining-related failures can be traced back to improper cooling? In the world of CNC (Computer Numerical Control) machining, the balance between temperature, friction, and material properties is crucial for success. As manufacturers strive for precise specifications and optimal production efficiency, understanding the significance of coolant usage becomes indispensable.
In this extensive guide, we will delve into how effective coolant application can enhance machining results in CNC operations. From understanding the role of coolant to exploring best practices and case studies, this blog aims to equip you with actionable insights to optimize your machining processes. So, whether you’re an experienced machinist or a novice, you’ll find valuable information to improve your CNC machining results significantly.
Understanding the Role of Coolants in CNC Machining
What is CNC Machining?
CNC machining is a manufacturing process that utilizes computer-controlled machines to produce complex parts. Precision and speed are crucial in this process, where accuracy is often measured in micrometers. CNC machining is commonly employed in various industries, including aerospace, automotive, and medicine, making it essential for manufacturers to optimize every facet of the process.
The Purpose of Coolants
Coolants play an essential role in CNC machining by:
Types of Coolants
Before diving deeper into how CNC machining can improve results through coolant usage, it’s vital to understand the different types of coolants available:
Improving Machining Results with Effective Coolant Usage
Choosing the proper coolant is the first step toward improved machining results. Since different materials require different cooling solutions, it’s essential to assess your specific application and machining parameters. Factors to consider include:
The method of coolant application is just as important as the coolant choice. Here are some effective coolant application techniques for CNC machining:
a. Flood Cooling
Flood cooling is a conventional technique that involves pumping coolant directly over the cutting area continuously. This method effectively removes chips, flushes debris, and keeps the cutting edge cool. However, it may require extensive cleanup efforts and could result in wastage if not managed properly.
b. Mist Cooling
Mist cooling uses vaporized coolant particles that form a fine mist over the cutting surface. This reduces coolant usage and is excellent for applications where flooding is impractical. However, it may not provide sufficient cooling in heavy-cutting applications or when machining harder materials.
c. Jet Cooling
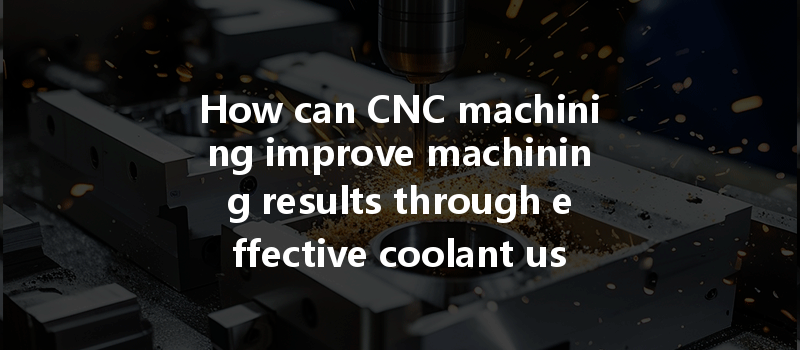
Jet cooling focuses a high-pressure stream of coolant on the cutting tool. This allows it to penetrate the interface efficiently, providing enhanced cooling while minimizing the risk of thermal distortion. Jet cooling is particularly effective during high-speed machining.
d. Minimum Quantity Lubrication (MQL)
MQL applies minimal amounts of lubricant to the cutting area, enhancing tool life while preserving materials. This method significantly reduces environmental impacts but requires appropriate equipment to control application effectively.
Efficient temperature management is vital for maintaining optimal machining processes. Here are techniques to monitor and control temperature effectively:
a. Thermal Imaging
Utilizing thermal imaging cameras can provide real-time monitoring of temperature changes during machining. This practice helps operators adjust coolant flow rates and pressure based on temperature readings, ensuring optimal conditions.
b. In-Process Sensors
Implementing sensors that continuously monitor the cutting temperature allows for real-time adaptations. When coupled with automated control systems, this can significantly improve machining accuracy and reduce downtime.
The effectiveness of cooling systems declines over time due to contamination, evaporation, and other factors. Regular maintenance ensures that the coolant performs optimally and contributes positively to the machining process. Key maintenance activities include:
Training employees on proper coolant usage, maintenance, and handling is essential for optimizing machining processes. Key points to cover include:
Once coolant practices are implemented, it’s crucial to evaluate their effectiveness. Adopting a data-driven approach allows businesses to refine their machining processes continuously.
Utilize the following methods for analyzing results after implementing new coolant strategies:
As we’ve explored in this blog, the effective use of coolants in CNC machining significantly enhances results, leading to improved tool life, better part finishes, and enhanced process efficiency. By carefully selecting the right type of coolant, implementing appropriate application techniques, monitoring temperatures, maintaining coolant systems, and training employees, manufacturers can optimize their CNC operations.
Ultimately, understanding the importance of coolant usage in CNC machining is a significant step toward improving production quality and competitiveness within the industry. As you consider your machining processes, remember that minor adjustments in coolant strategies can lead to substantial improvements in results, and investing time in these practices will pay dividends in the long run.
Incorporating effective coolant usage into your CNC machining processes is not just an operational necessity—it’s a pathway to excellence in manufacturing.