Opening
Did you know that corrosion is responsible for nearly 25% of the maintenance costs in industries ranging from aerospace to manufacturing? The reality is that unchecked corrosion can lead to catastrophic failures and significant financial losses. Fortunately, CNC (Computer Numerical Control) machining offers innovative approaches to enhance corrosion resistance in custom machined parts, which is crucial for increasing durability and extending the life of components. This blog will delve into how you can leverage CNC machining, combined with effective treatment processes, to combat corrosion and ensure that your manufactured parts are not only high-quality but also resilient.
—
Understanding Corrosion and Its Implications
Corrosion is a natural process that occurs when materials, particularly metals, react chemically with their environment. This can lead to significant degradation of parts, affecting performance, safety, and aesthetic qualities. For industries that rely heavily on metal components, such as the automotive or aerospace sectors, corrosion poses serious challenges. From increased maintenance costs to reduced operational efficiency, understanding how to combat corrosion is essential.
Types of Corrosion
Understanding these types is fundamental to selecting the appropriate CNC machining and treatment options to yield maximum corrosion resistance.
—
CNC Machining: The Best Defense Against Corrosion
CNC machining has revolutionized industries by offering precision, accuracy, and efficiency. However, the true beauty of CNC lies in its ability to integrate with various post-machining treatment processes to enhance corrosion resistance further. Let’s explore how:
The first line of defense against corrosion is the choice of the material itself. Popular materials used in CNC machining include stainless steel, aluminum, and specialized alloys designed for corrosion resistance:
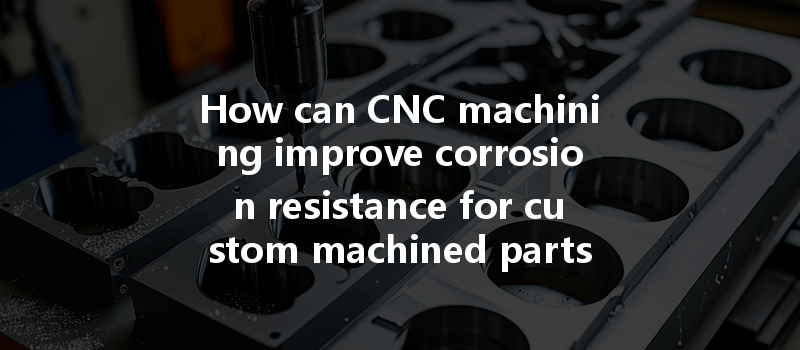
Investing in CNC machines equipped with advanced features can significantly improve part finish, thereby enhancing corrosion resistance. Here are some beneficial techniques:
Once the parts have been precisely machined, various post-processing treatment options can further enhance their corrosion resistance:
CNC machining doesn’t stop once the parts are produced. Ongoing maintenance plays a vital role in combating corrosion. Regular inspections, routine maintenance, and condition monitoring are essential for identifying potential corrosion issues before they escalate. Digital technologies, such as IoT sensors, can be employed to monitor environmental conditions and component integrity in real time.
—
Combating corrosion is a multifaceted challenge, but CNC machining paired with proper treatment processes presents a compelling solution. By carefully selecting materials, employing advanced machining techniques, and integrating effective surface treatments, companies can significantly improve the corrosion resistance of their custom machined parts.
With an ever-present threat posed by corrosion, industries must take proactive steps to ensure they leverage modern manufacturing technologies and processes effectively. By doing so, not only can they reduce maintenance costs and extend the lifecycle of parts, but they can also ensure safety and reliability in their operations.
In an age where efficiency, quality, and cost-effectiveness are paramount, investing in CNC machining to enhance corrosion resistance is not just a choice—it’s a necessity. Readers should reflect on how their current manufacturing practices align with these advancements and consider adjustments that could lead to substantial long-term benefits. The right combination of technology, treatment, and maintenance can transform the way we view corrosion—turning a daunting challenge into an opportunity for innovation and excellence.
—