Did you know that the precision of CNC (Computer Numerical Control) machining can reach tolerances as tight as ±0.005 inches? This incredible accuracy is not just an impressive feat of engineering; it’s a critical requirement for industries ranging from aerospace to automotive, where even the smallest discrepancy can lead to costly failures or unsafe products. As demanding as the machining process may seem, particularly for large parts, understanding how to ensure dimensional accuracy is key for manufacturers aiming for excellence.
In the world of manufacturing, maintaining dimensional accuracy during CNC machining, especially for large components, is a topic of immense importance. The challenges can become significantly more daunting with the complexity and larger sizes of the workpieces. In this extensive blog, we will delve into the factors influencing dimensional accuracy, examine the implications of failure in these areas, and outline the techniques and technologies manufacturers can implement to ensure precision and maintain machining quality.
—
CNC machining represents a cornerstone of modern manufacturing technology. By leveraging computer systems to control machinery, CNC technology offers heightened precision, repeatability, and efficiency compared to traditional machining methods. The process includes several phases: design, programming, tooling selection, setup, machining, and quality control. Despite its advantages, achieving high levels of accuracy remains a challenge, especially in larger parts where various mechanical and physical factors come into play.
Key Components of CNC Machining
Dimensional accuracy refers to how closely a machined part’s finished dimensions match the intended specifications. It encompasses several factors, including length, width, thickness, and angular measurements. A part manufactured to the required specifications not only fits with other parts but also performs its intended function without fail. It’s crucial that manufacturers thoroughly understand the dimensions critical to the parts they fabricate, as inaccuracies can lead to a range of issues—from assembly problems to operational failures.
While CNC machining is highly accurate, several factors can impair the overall dimensional accuracy of large parts:
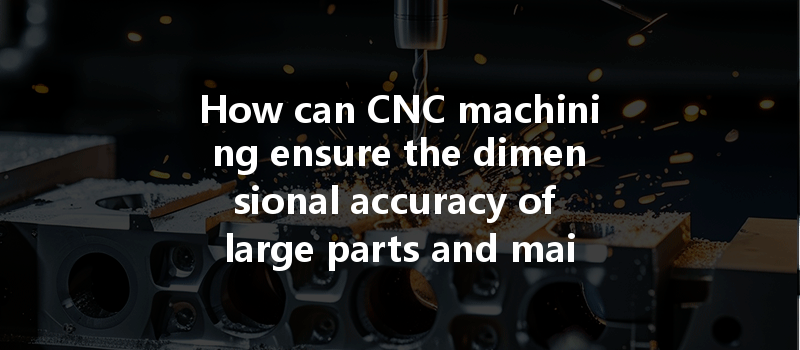
Achieving and maintaining dimensional accuracy, particularly for large parts, requires a complex interplay of techniques, tools, and technologies. Below are some effective approaches:
4.1 Proper Workpiece Fixture Design
An effective fixture design is critical for holding large workpieces securely throughout the machining process. Techniques to improve fixture stability include:
4.2 Advanced Tooling Options
Select tooling that is designed specifically for the material and geometry of the parts being machined. Consider the following:
4.3 Regular Calibration and Maintenance
Routine calibration of CNC machines and tools is essential for maintaining accuracy. Steps such as:
4.4 Error Detection and Compensation Techniques
Implementing advanced measurement systems can help identify deviations and automatically make corrections:
4.5 Utilizing Digital Twin Technology
Digital twins create a virtual representation of the physical machining processes, allowing for simulation and analysis. These models can be used to:
Let’s delve into specific examples where CNC machining has delivered precision in large part fabrication:
: The Importance of Dimensional Accuracy in CNC Machining
In the competitive world of CNC machining, particularly when dealing with large parts, accuracy isn’t just preferred—it’s essential. The costs associated with inaccuracies can range from minor setbacks to catastrophic failures impacting both safety and finances. By understanding and implementing techniques such as proper workpiece fixture design, advanced tooling options, routine calibration, error detection systems, and digital twins, manufacturers can achieve the high standards required.
As industries continue to evolve, the emphasis on precision and quality will only grow. Therefore, investing in these strategies and technologies not only ensures the success of current projects but also positions manufacturers favorably for future challenges and innovations.
Remember, the stakes in CNC machining are high, but so too are the rewards when dimensional accuracy is achieved and maintained. Understanding this critical topic is not only worth your time, it’s a crucial component of successful manufacturing in today’s high-tech world.