: An Interesting Fact
Did you know that the tool life of a cutting tool can significantly impact the overall efficiency and cost-effectiveness of machining processes? In the world of CNC (Computer Numerical Control) machining, particularly when working with tough materials like 310S stainless steel, understanding how to enhance tool life is critical. This guide explores the various techniques and practices that can be implemented to improve the tool longevity when machining 310S stainless steel, a material renowned for its high-temperature resistance and corrosion resistance, widely used in industries like aerospace, oil and gas, and chemical processing.
Understanding 310S Stainless Steel
Before diving into the techniques for enhancing tool life, it is essential to fully understand 310S stainless steel and its properties.
What is 310S Stainless Steel?
310S is an austenitic stainless steel alloy primarily composed of chromium and nickel. Unlike its counterpart, 310 stainless steel, the ‘S’ designation signifies a lower carbon content, which improves its high-temperature properties. Key characteristics include:
These properties make 310S stainless steel an ideal choice for applications in extreme conditions, but they also present challenges in terms of machining.
Challenges in Machining 310S Stainless Steel
Machining 310S stainless steel can be challenging due to the following factors:
Solutions for Enhancing Tool Life in CNC Machining of 310S Stainless Steel
Achieving longer tool life in CNC machining of 310S stainless steel requires a multi-faceted approach. Below are detailed strategies and best practices:
Materials of Cutting Tools
Choosing the appropriate material for cutting tools is critical. Carbide tools, particularly coated carbide, are well-suited for machining 310S due to their hardness and wear resistance.
Optimizing Tool Geometry
The design of the cutting tool can play a significant role in determining its longevity.
Optimizing Cutting Speeds and Feeds
Cutting speeds and feed rates should be carefully calibrated.
Utilizing Coolants
Heat is a primary enemy of tool life, so managing it is paramount.
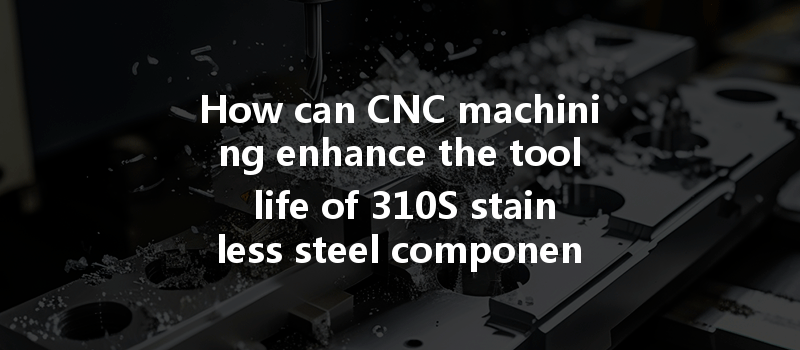
Proper Fixture and Setup
Securely holding the workpiece can prevent vibrations that lead to tool wear.
Regular Inspections
Implementing a routine for tool inspection can prevent unexpected failures.
Exploring New Technologies
Adopting modern technologies can help prolong tool life.
Employing Cutting Tool Coatings
Advanced tool coatings can elevate the performance of cutting tools.
Ensuring Operator Proficiency
Training operators in best practices can lead to improved machining outcomes.
Leveraging CNC Technology
CNC machines can collect data during manufacturing; this information can be used to optimize processes.
: The Importance of Tool Life Enhancement
In summary, enhancing the tool life of cutting tools for 310S stainless steel machining is paramount to maximizing efficiency and reducing costs in manufacturing. Key strategies include selecting the right cutting tools, optimizing tool geometry, adjusting cutting parameters, implementing effective cooling methods, and continuous monitoring and maintenance of tools.
By investing time and resources into these practices, manufacturers can see significant improvements in both the longevity of their tools and the quality of their produced parts.
Understanding and implementing these strategies not only enhances productivity but also contributes to the overall sustainability of the manufacturing process. As industries strive for higher efficiency and lower costs, the importance of tool life in CNC machining becomes increasingly clear.
Reflect on these strategies as you navigate the complex landscape of CNC machining, ensuring you remain at the forefront of efficiency and innovation in your production processes.