Did you know that approximately 50% of all machining problems arise from heat generation during the cutting process? This startling statistic highlights the critical need for manufacturers and engineers to develop effective methods for managing heat in CNC milling, particularly when it comes to prototype machining. As industries increasingly rely on rapid prototyping and precision machining techniques, understanding how to reduce cutting heat has never been more vital.
In this comprehensive blog post, we will dive deep into the world of CNC machining, exploring the intricacies of cutting heat, its impact on performance and product quality, particularly in prototype machining. We will provide practical solutions and strategies that can help you mitigate heat-related challenges, ultimately leading to more efficient and precise machining processes.
—
1.1 What is CNC Machining?
CNC (Computer Numerical Control) machining is a manufacturing process where pre-programmed computer software dictates the movement of machinery and tools. This technique allows for high precision and complex designs to be achieved with minimal human intervention.
1.2 What is Prototype Machining?
Prototype machining refers to the process of creating a prototype—a working model or sample of a product. This is particularly critical in industries such as aerospace, automotive, and medical devices, where prototypes are essential for testing form, fit, and function before full-scale production.
—
2.1 What Causes Cutting Heat?
Cutting heat is primarily generated during the interaction between the cutting tool and the workpiece material. Factors contributing to heat generation include:
2.2 Effects of Cutting Heat
Excessive cutting heat can lead to multiple adverse effects, such as:
—
3.1 Optimize Cutting Parameters
One of the most effective strategies in heat management is optimizing cutting parameters, including cutting speed, feed rate, and depth of cut.
3.2 Tool Selection and Geometry
The choice of cutting tool plays a significant role in managing cutting heat. Key considerations include:
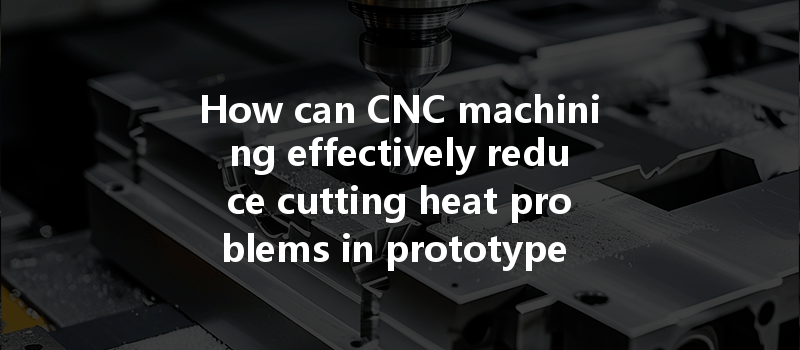
3.3 Cooling and Lubrication Techniques
Cooling methods are essential in managing cutting heat. Two main types of cooling and lubrication techniques to consider are:
3.4 Use of Specialized Cutting Tools
Utilizing specialized cutting tools designed for heat resistance can greatly impact the overall performance during CNC machining. For example, tools made from polycrystalline diamond (PCD) or cubic boron nitride (CBN) may provide better thermal stability.
—
4.1 Temperature Measurement Techniques
Monitoring the temperature generated during machining is crucial for identifying overheating incidents early. Some effective measurement techniques include:
4.2 Data Analysis
Utilizing software for data analysis can help in predicting and controlling thermal behavior, allowing for timely adjustments in the machining process.
—
Here, we will discuss some industry case studies that exemplify effective techniques to reduce cutting heat in prototype machining.
5.1 Aerospace Industry
In the aerospace sector, where precision is paramount, one company transitioned from traditional machining to a more advanced CNC setup featuring better temperature control measures. As a result, they improved tool life by 30% and achieved a 20% reduction in machining time for their aluminum parts.
5.2 Automotive Industry
An automotive manufacturer implemented MQL techniques in their CNC operations, which not only reduced heat generation but also cut down on coolant disposal costs by 40%. They reported fewer defects in their prototype parts as a result.
—
6.1 Adaptive Machining Systems
Emerging technologies in adaptive machining systems promise to revolutionize the way heat management is approached. These systems can automatically adjust cutting parameters in real-time based on the heating response of the material.
6.2 Advanced Materials
Research into advanced materials with enhanced thermal characteristics is ongoing. The implementation of alloys specifically designed to reduce heat generation and improve machinability will be a game-changer.
—
In recapitulation, reducing cutting heat in CNC machining, particularly during prototype machining, is essential for improving overall productivity and quality. Through smart choices in cutting parameters, tool selection, cooling methods, and continuous monitoring, manufacturers can effectively mitigate heat-related issues.
This blog has outlined not just the problems associated with cutting heat, but also practical solutions and innovations currently available. As industries continue to evolve, those who are proactive in addressing machining challenges like heat management will lead the way. Remember, thoughtful consideration of these techniques is not just an option but a necessity for staying competitive in the fast-paced manufacturing landscape.
By keeping the conversation about cutting heat alive, we can foster partnerships, encourage innovations, and elevate the standards of precision machining across various industries. Stay curious, and remember that every degree counts in the journey toward machining excellence!