Did you know that over 60% of CNC machinists consider burr formation one of the most persistent and frustrating challenges in machining processes? Burrs can affect the functionality, aesthetics, and overall quality of machined parts, especially when using materials like polypropylene (PP)—a thermoplastic known for its versatility. The presence of burrs not only leads to additional processing time and costs but can also compromise the integrity of assembled products. This blog will dive into the intricate world of CNC machining, focusing specifically on the strategies to mitigate burr formation while working with polypropylene materials.
Understanding Burrs in CNC Machining
Before we delve into solutions, it’s essential to understand what burrs are and why they form during CNC machining. Burrs are unwanted protrusions or rough edges that remain after a machining operation. They can occur due to various factors, including machine settings, tooling, workpiece properties, and even the ambient environment.
In the context of polypropylene—the choice material for applications such as packaging, automotive components, and consumer goods—burrs can be particularly troublesome. Polypropylene is known for its high impact resistance and flexibility; however, its tendency to deform during machining can result in a high incidence of burr formation.
Factors Contributing to Burr Formation in Polypropylene
Strategies to Avoid Burrs in CNC Machining of Polypropylene
Now that we have discussed the contributing factors, let’s explore effective strategies to minimize or eliminate burr formation when machining polypropylene materials.
Choosing the right tooling is paramount. Here are some tips:
Optimizing cutting parameters can significantly reduce burrs:
Cooling and lubrication are effective methods to control temperature and enhance cut quality:
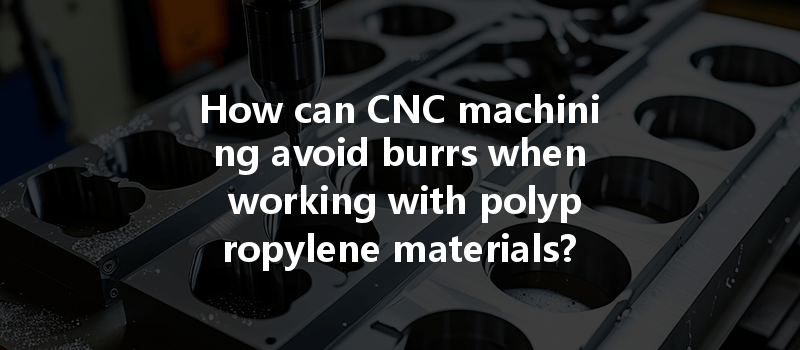
Innovative machining techniques can lead to improved results:
Even with robust machining practices, some burrs may remain. Effective post-machining techniques can smoothen surfaces:
Implementing Quality Control Measures
To ensure that the strategies implemented are effective, it’s crucial to establish quality control measures:
Case Studies
Case Study 1: Aerospace Industry
In an aerospace project utilizing polypropylene for lightweight components, a manufacturer faced significant issues with burrs, resulting in higher processing costs. After implementing sharper tooling and optimizing cutting parameters, they achieved a 40% reduction in burr formation.
Case Study 2: Automotive Sector
A company specializing in automotive components faced challenges with product finishes. By utilizing high-speed machining and post-treatment deburring processes, the firm improved surface quality and reduced manual labor time by 30%.
Burr formation during CNC machining of polypropylene is a multifaceted challenge that can jeopardize the quality and efficiency of production processes. By understanding the factors contributing to burr formation and implementing targeted strategies—such as selecting the right tooling, optimizing parameters, and adopting advanced machining techniques—manufacturers can significantly minimize burr issues.
Being proactive in addressing burr formation not only enhances product quality but also decreases production costs and time. As industries increasingly rely on precision machining for competitive advantage, mastering these techniques is more important than ever.
In summary, this blog has highlighted the core techniques and considerations for managing burrs in CNC machining of polypropylene. Engaging in these best practices is vital for any machinist or manufacturer concerned with maintaining the highest standards in their production processes. Stay ahead in the competitive landscape of CNC machining by focusing on quality and efficiency, which begins with effectively controlling burr formation.