:
Did you know that the aerospace industry spends an estimated $2.5 billion every year on machining processes? Within this vast budget, achieving precision and quality in every component is paramount, particularly when working with metals like brass. Brass is often utilized in critical applications due to its desirable properties such as corrosion resistance, machinability, and aesthetic appeal. However, maintaining precision in CNC (computer numerical control) machining can be a daunting task, especially when surface quality is taken into account.
In the world of CNC machining, quality is not just a metric; it’s a fundamental requirement. The surface finish of machined parts can significantly influence their performance and durability. As such, having a robust system in place for surface quality inspection is not just beneficial—it’s essential. This blog delves deep into the subject, exploring how brass surface quality inspection can enhance CNC machining accuracy, followed by practical techniques and methodologies to ensure top-notch results.
The Importance of Surface Quality in CNC Machining
Before we dive into the methods of quality inspection, let’s examine why surface quality is crucial in CNC machining. The surface finish of any machined part plays a vital role in its performance, affecting everything from friction and wear to aesthetic value. Finishing techniques are often employed to reach a desired level of surface roughness, a metric that describes the texture of a surface.
In brass machining specifically, the surface finish can have implications for:
Common Challenges in Brass Surface Quality Inspection
When inspecting the surface quality of machined brass parts, manufacturers face various challenges:
Techniques for Brass Surface Quality Inspection
To effectively enhance accuracy in CNC machining, a systematic approach to surface quality inspection is necessary. Here, we outline various techniques:
Though it may seem basic, visual inspection remains a powerful tool for detecting surface defects such as scratches, pitting, and discoloration. Operators equipped with magnifying glasses or microscopes can perform visual checks. It’s crucial, however, to establish a baseline of acceptable versus unacceptable surface quality.
Surface roughness can be quantified through several methods, including:
CMMs play an integral role in quality inspection for CNC machined parts. These versatile machines can be programmed to take measurements across multiple axes, providing an in-depth analysis of the dimensions and surface profile of brass parts.
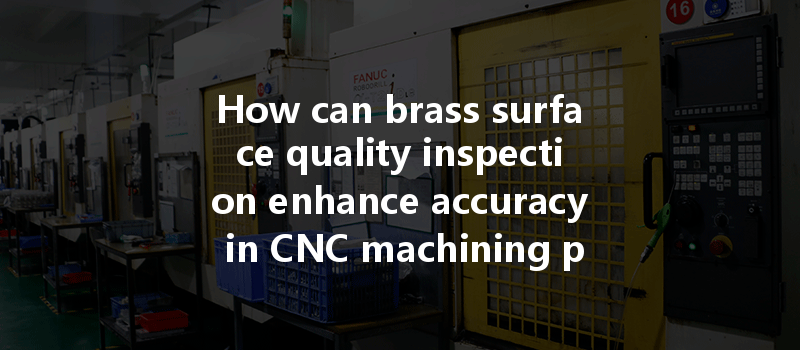
For applications requiring high magnification and detail, scanning electron microscopy can visualize surface textures at the micro and nano-scale. This technique is invaluable for understanding how machining processes affect brass surfaces at a microscopic level.
3D profiling provides a comprehensive view of surface topography, allowing manufacturers to visualize and quantify features such as peaks and valleys that affect surface quality. This technique can reveal issues that may not be apparent through 2D measurements.
Guidelines for Implementing Effective Surface Quality Inspection
To practically implement these inspection techniques, consider the following guidelines:
Integrating Inspection Results into the CNC Machining Process
Once surface quality inspections are executed, the next step is to incorporate the findings into the CNC machining processes. This can enhance accuracy and consistency in machining outcomes. Here’s how:
Technological Innovations in Inspection Processes
In recent years, numerous innovations have enhanced the effectiveness of surface quality inspection methods:
In summary, the importance of brass surface quality inspection in enhancing accuracy within the CNC machining process cannot be overstated. By adopting the right inspection techniques and implementing robust quality control measures, manufacturers can significantly improve the performance and longevity of their brass components.
Moreover, as technology continues to evolve, integrating automated inspection systems and data analytics will only amplify these benefits. Ultimately, ensuring surface quality in machining is not merely an operational necessity but a strategic advantage that can help businesses remain competitive in a constantly evolving market.
As you consider your own approaches to CNC machining and surface quality inspection, reflect on how these insights can be applied in your operations. The intricacies of metalworking may seem daunting, but the value of precision and quality speaks for itself—enhanced performance, reduced downtime, and the satisfaction of delivering high-quality products to your clients. This blog serves not just as a resource, but as a reminder of the profound impact that diligent surface quality inspection can have on the success of CNC machining endeavors.