When it comes to CNC machining for aluminum alloys, quality control isn’t just an afterthought—it’s the cornerstone of the process. Whether you’re creating complex components for aerospace, automotive, or electronics, the quality of your final product can make or break the success of your project. I’ve spent years working in CNC machining and, through that experience, I’ve learned firsthand how critical proper quality control and testing standards are to ensure that the job gets done right.
In this comprehensive guide, I’m going to walk you through the essential steps for maintaining top-notch quality in CNC machining of aluminum alloys. From the initial planning phase to post-processing inspections, I’ll share actionable insights and industry best practices that can help you overcome common issues like poor surface finishes, inconsistent dimensions, and material defects.
What is CNC Machining for Aluminum Alloys?
CNC machining is a process that involves the use of Computer Numerical Control (CNC) machines to remove material from a workpiece to create precise shapes and components. When applied to aluminum alloys, the process becomes even more specialized. Aluminum alloys are lightweight, strong, and highly versatile, making them ideal for a wide range of applications. However, machining aluminum alloys requires specific knowledge and tools to ensure optimal results.
Here are some of the most common CNC machining techniques used for aluminum alloys:
CNC Milling: Precision at Its Best
CNC milling is one of the most popular machining methods for aluminum alloys. In this process, a rotating cutter removes material from the aluminum workpiece. It is particularly useful for creating parts with flat surfaces, pockets, and intricate shapes.
When machining aluminum alloys, CNC milling offers the advantage of high precision and efficiency. Depending on the complexity of the part, it can achieve extremely tight tolerances, making it ideal for industries that require precise and reliable components.
CNC Turning: Best for Cylindrical Parts
If your part needs to have a circular or cylindrical shape, CNC turning is the method to go for. The process involves rotating the aluminum workpiece while a stationary cutting tool removes material. CNC turning is great for components like aluminum enclosures, shafts, and connectors.
While CNC turning offers great precision, it’s best suited for parts that are symmetrical or have rotational symmetry. If your part has more complex geometry, you might want to consider combining turning with milling.
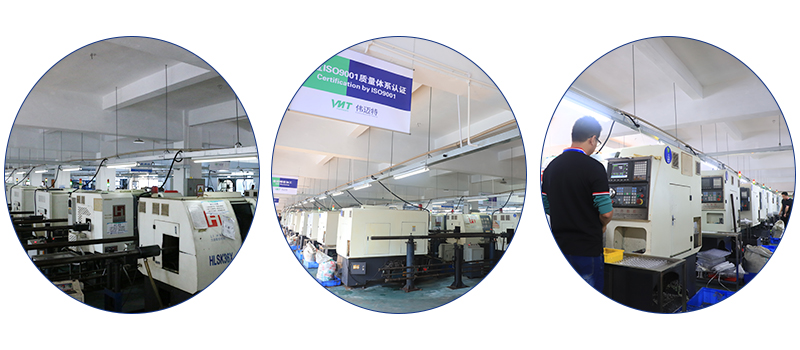
5-Axis Machining: Going Beyond the Norm
For highly complex geometries, 5-axis machining offers unparalleled flexibility. This process allows the workpiece to be manipulated along five different axes, resulting in the ability to machine parts with intricate shapes and under extremely tight tolerances. This makes 5-axis CNC machining ideal for aerospace, medical, and automotive components where precision and complexity are paramount.
In fact, for aluminum alloy machining, 5-axis machining can handle both internal and external features with greater accuracy than traditional methods, reducing the need for rework and minimizing material waste.
The Importance of Quality Control in CNC Machining for Aluminum Alloys
Now that we’ve covered the basics of CNC machining for aluminum alloys, let’s talk about quality control. No matter how advanced the machine or skilled the operator, the quality of the final part depends heavily on consistent and effective quality control practices.
In my experience, a lack of robust quality control can lead to issues such as dimensional inaccuracies, poor surface finishes, and even material defects. The result? Costly rework, project delays, and a damaged reputation. That’s why quality control isn’t just about checking the box—it’s integral to the entire process.
Key Quality Control Areas for CNC Machining of Aluminum Alloys
- Material Selection and Inspection
- The quality of the final product begins with the material itself. Choosing the right aluminum alloy is the first step in ensuring high-quality parts. Common alloys for CNC machining include 6061, 7075, and 2024, each offering different mechanical properties and machinability.
- Upon receiving the aluminum stock, it’s essential to inspect for defects like surface scratches, dents, or irregularities in thickness. Even slight imperfections in the raw material can lead to poor machining results.
- Dimensional Accuracy
- Maintaining the correct dimensions throughout the machining process is crucial, especially for parts that need to fit into complex assemblies. I’ve learned that checking the dimensions early and often is one of the most effective ways to avoid future problems.
- Tools like calipers, micrometers, and coordinate measuring machines (CMM) are essential for ensuring that the parts meet the specified tolerances. At YL-Machining, we perform regular checks using CMM to ensure that every part matches the design specifications down to the smallest detail.
- Surface Finish Quality
- Aluminum alloys can be prone to surface imperfections like tool marks, scratches, or rough finishes, especially when using CNC milling. In industries like electronics or aerospace, a clean, smooth surface finish is not just a matter of aesthetics—it can affect performance and durability.
- To inspect surface finish, we use profilometers that measure surface roughness. Typically, the Ra (Roughness Average) value is used to quantify the smoothness of the surface. For many aluminum components, I aim for a finish with an Ra value of 0.8 microns or less.
- Functional Testing
- After machining, I always recommend performing functional testing on prototypes or first-articles to check for fit, form, and function. If you’re making aluminum enclosures for sensitive electronics, for example, you need to ensure that components fit properly and that the enclosure will protect the internals as intended.
- In my experience, these tests can reveal small issues early on—like misalignments or holes that don’t match up—which can save a lot of headaches down the road.
The Role of Testing Standards in CNC Machining
When working with aluminum alloys, having clear testing standards in place ensures that quality isn’t left to chance. These standards help maintain consistency and ensure that every part produced is reliable and within spec. Let’s take a closer look at the various testing standards that should be applied in CNC machining of aluminum alloys.
1. Dimensional and Tolerance Testing
- As I mentioned earlier, dimensional accuracy is critical. The key is to measure the final product against the original CAD drawing and ensure that all measurements fall within the specified tolerances.
- I recommend using CMM (Coordinate Measuring Machines) or laser scanners for dimensional checks. These machines use highly precise probes or lasers to measure the part’s dimensions from multiple angles, ensuring absolute accuracy.
2. Surface Finish and Texture Testing
- The surface of your aluminum part should match the desired finish quality, whether that’s a smooth matte finish or a polished look. This is where surface roughness testing becomes crucial.
- Profilometers and other surface inspection tools are widely used to ensure the final product meets the required Ra or other relevant roughness standards.

3. Material and Strength Testing
- If you’re working with more demanding applications, like aerospace or automotive, you need to ensure that the material itself has the necessary strength and durability. Tensile testing, hardness testing, and impact testing are key methods to verify that the material properties meet the requirements.
- Aluminum alloys, for example, can vary significantly in strength depending on the specific alloy and heat treatment. It’s vital to verify that the material properties match the specifications outlined in your design.
4. Post-Machining Process Testing
- After machining, aluminum parts often go through additional processes such as anodizing, coating, or heat treating. These processes can affect the final dimensions and surface finish, which is why additional checks are necessary.
- I always recommend doing a final round of testing after any secondary processes to ensure that nothing was compromised.
Overcoming Common CNC Machining Challenges
Throughout my years working in CNC machining, I’ve faced my fair share of challenges. In fact, some of the most common issues include:
- Delays in Delivery: One of the biggest frustrations for clients is when projects fall behind schedule. A large part of this issue can stem from poor communication or a lack of clear timelines. To avoid this, I make sure to set realistic expectations and keep clients updated at every stage of production.
- Quality Control Issues: No one likes receiving parts that are out of spec or have surface defects. However, with careful planning and regular inspections, you can minimize the chances of quality problems creeping up.
- Poor After-Sales Service: When something goes wrong, you need a reliable partner to fix the problem quickly. At YL-Machining, we make it a point to offer responsive after-sales support, so if issues arise, we’re ready to address them immediately.
Conclusion: The Importance of Quality Control in CNC Machining
To sum up, CNC machining for aluminum alloys requires attention to detail, careful planning, and most importantly, stringent quality control and testing standards. Whether you’re using CNC milling, CNC turning, or 5-axis machining, maintaining high standards throughout the entire process will ensure that your parts are accurate, functional, and aesthetically pleasing.
If you’re looking to find a reliable CNC machining partner to meet your quality standards and deadlines, you want a company like YL-Machining—a team that understands the importance of precision, quality, and timely delivery.
Do you have any specific challenges with CNC machining of aluminum alloys that you’d like help with? I’d love to hear about it and share